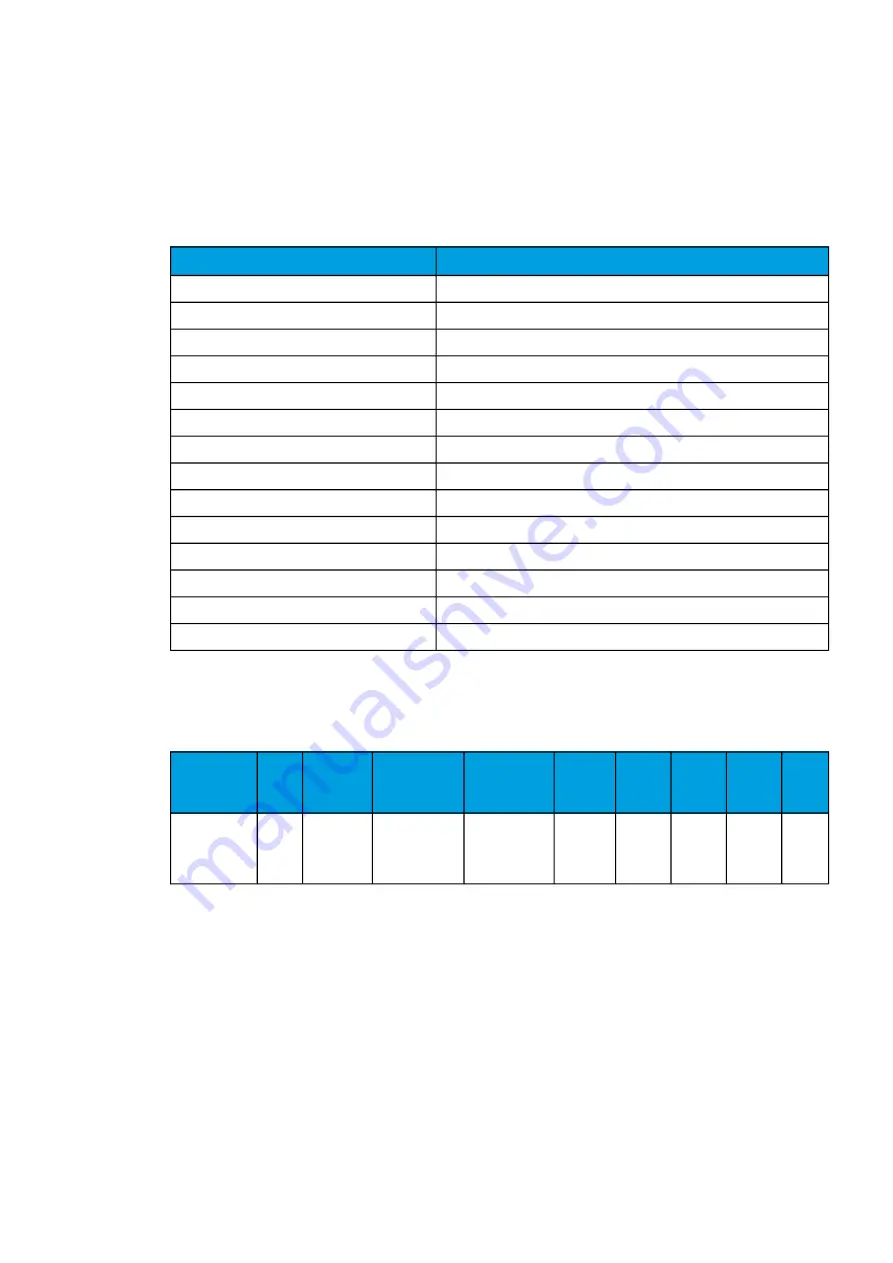
Events and registers
The motor start/locked rotor monitoring function (abbreviated "LCR" in event block names) generates
events from the detected motor status. The data register is available, based on the changes in the
events.
Table. 5.3.18 - 159. Event messages.
Event block name
Event names
LCR1
Max. Start time exceed ON
LCR1
Max. Start time exceed OFF
LCR1
Set start time exceed ON
LCR1
Set start time exceed OFF
LCR1
Speed Switch not received ON
LCR1
Speed Switch not received OFF
LCR1
Start ON
LCR1
Start OFF
LCR1
Set time Trip ON
LCR1
Set time Trip OFF
LCR1
Max cap Trip ON
LCR1
Max cap Trip OFF
LCR1
Blocked ON
LCR1
Blocked OFF
The function registers its operation into the last twelve (12) time-stamped registers. The table below
presents the structure of the function's register content.
Table. 5.3.18 - 160. Register content.
Date and
time
Event
Start/
Stall time
Max. time
used
Set time
used
Thermal
cap.
used
L1
current
L2
current
L3
current
SG
used
dd.mm.yyyy
hh:mm:ss.mss
Event
name
Recorded
duration of
stall/start
Percentage
used from max
safe stall time
Percentage
used from user
set max time
Thermal
capacity
used
Phase
L1
current
x I
n
Phase
L2
current
x I
n
Phase
L3
current
x I
n
Used
setting
group
5.3.19 Frequent start protection (N>; 66)
The frequent start protection function is used for monitoring and preventing the starting of the motor to
happen too frequently. This function monitors the number of the starts the motor has used within a
given time frame to ensure that the start stress does not exceed the limits stated by the manufacturer.
The start-up situation is most stressful normal operation situation for motors that are started with Direct
On Line; the manufacturer gives safe start limits with a specified time frame for both cold and hot
motors in order to guarantee the motor's lifetime. Usually the manufacturers also specify the time
between consequent starts. When a set number of starts have been used or a new start or start
attempt is made too quickly after the previous start or start attempt, further starting attempts should be
blocked by using the N> function, thus allowing the motor to cool down sufficiently before the next start
attempt.
A
AQ
Q-M255
-M255
Instruction manual
Version: 2.06
© Arcteq Relays Ltd
IM00020
197
Содержание AQ-M255
Страница 1: ...AQ M255 Motor protection IED Instruction manual...
Страница 2: ......
Страница 384: ...Figure 7 4 189 Example block scheme A AQ Q M255 M255 Instruction manual Version 2 06 382 Arcteq Relays Ltd IM00020...
Страница 405: ...Figure 8 14 211 Device installation A AQ Q M255 M255 Instruction manual Version 2 06 Arcteq Relays Ltd IM00020 403...