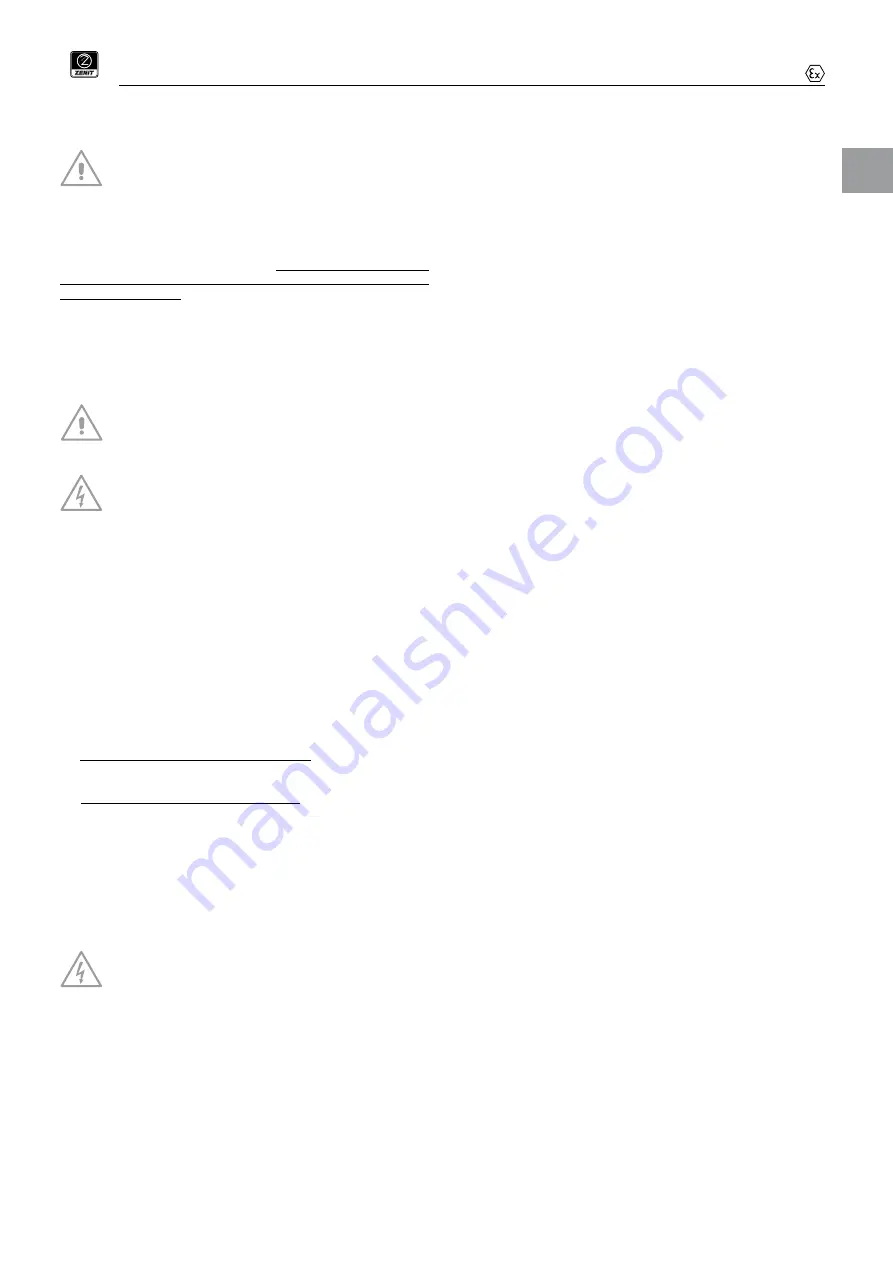
EN
9
better together
User and maintenance manual – Translation of original instructions
All of the instructions in the manual only apply to electric submer-
sible pump which are used in areas with a potentially explosive
atmosphere
WARNING: Failure to follow the safety instructions could
cause explosions!
ATEX electric pumps, identifiable by the -EX acronym, are certified
according to the antideflagrant protection mode recorded on the plate
for the operation within shafts, tanks and, in the version including co
-
oling jacket, in drying chambers where explosive gas/dust is present
or in any area classified as Zone 1 or 21;
it is the duty of the user to
assure that the dust on the surface of the pump does not exceed
a thickness of 50mm.
WARNING: in order to guarantee the stated ATEX conformity, the
liquid level must never be lower the pump body during regular
operation. To the purpose, a level control system is provided
through the use of float switches, level probes or, alternatively,
or guarded operation (human presence).
WARNING:
any intervention which modifies the pump com
-
ponents can create a DANGER of EXPLOSION.
The pumps MUST be used ONLY in areas compatible with
the characteristics recorded on the label.
WARNING:
during handling, installation or disinstallation
operations the pump must be disconnected from the power
supply panel.
1. TECHNICAL CHARATERISTICS
•
Tension of Power Supply: Single-phase or three-phase power sup
-
ply in accordance with the metal plaque;
Maximum voltage variation allowed for rated value:
•
±
10% for electro pumps with power cable length up to 30m;
•
±
5% for electro pumps with power cable length greater than 30m
but not exceeding 200m.
WARNING: the -EX pump is not intended for use with a fre-
quency changer
•
Immersion Depth: Max. 30 metres under liquid level;
•
Surrounding temperature: -2-20°C ≤ Ta ≤ +40°C;
•
Maximum permissible number of start-ups per minute: see the tech-
nical specifications
•
Protection Category IP 68;
•
Service Factor:
-
For electric pumps without a cooling jacket: S1 if fully immersed,
S3 with percentage indicated on the metallic plaque and sticky label,
for a partially immersed pump;
-
For electric pumps with a cooling jacket: S1 for use in a drying
chamber or for a partially immersed pump.
•
Usage: drainage, evacuation and/or removal of waste from sewers
and septic tanks in areas with the PRESENCE OF GAS AND EX
-
PLOSIVE DUST (-EX); removal of liquids containing solid and fila
-
mentous particles; drainage water, purification water and washing
water from civil and industrial processes in atmospheres containing
group II A and/or B gas (usually hydrocarbon gas) and/or atmosphe
-
res containing a mix of combustible dusts.
2. HANDLING AND SHIPPING
NEVER use the power cable or the float switch cable
to lift or move the pump. Always use the appropriate
handle or lifting hook.
For models weighing 25kg or less lifting and moving may be performed
manually using the handle fitted on the upper part of the pump.
For models weighing more than 25kg and in all cases where it is not
possible to maintain a correct and natural posture, lifting and moving
must be carried out using a rope or chain attached to lifting hook or
handle fitted on the upper part of the pump, and an appropriate me-
chanical device.
Check that there is no visible damage to the packaging and its contents
If there is any sign of significant damage, contact Zenit immediately.
Check that the characteristics recorded on the metal plaque corre-
spond to the product purchased.
Within a hazardous area, handle any moving with caution, avoi-
ding bumps or friction of the pump with other metallic objects as
this could cause sparks, therefore increasing the risk of explo-
sions.
3. STORAGE
During storage, the electric pump must be kept in a suitable place, out
of the reach of children or those with diminished responsibility, suitably
secured against falling and protected from damp, dust, vibrations and
extreme temperatures (below -5°C and above +40°C).
WARNING:
Turn the impeller by hand occasionally (at least every
month) through the outlet or intake, to prevent the mechanical seals
from sticking together.
Following storage, inspect the electric pump to make sure there is
no damage, check the oil level in the mechanical seals chamber and
make sure the impeller spins freely
If the electric pump needs to be stored for more than six months, prior
to commissioning it, change the oil in the mechanical seals chamber
and take it to an authorised disposal centre. Do not dispose of the oil
as household waste.
4. INSTALLATION
Before proceeding with the installation, carefully read the following
precautions:
•
While installing/uninstalling, the electric pump must be moved using
a rope or chain anchored to the handle.
•
Within a hazardous area, perform installation with caution, avoiding
bumps or friction of the pump with other metallic objects as this
could cause sparks, therefore increasing the risk of explosions.
•
The shaft in which the pump is installed must be of such dimensions
that the float switch, if present, may move freely.
•
In the presence of level control devices in the processed liquid,
make sure that the maximum number of start-ups allowed per hour
is respected.
•
WARNING:
the shock from built up electrostatic charges on isolated
components could cause an explosion. -EX pumps do not have iso-
lated components that are electrostatically chargeable and they are
all equipped with screw for connection to the equipotential ground
network. Any additional components installed in the hazardous area
must be connected to the earthing network according to the EN
1127-1 rule, part 6.4.7.
•
WARNING:
check the suitability for use in potentially explosive at
-
mospheres of each additional component installed in the hazardous
area.
•
When installing with coupling devices, pay utmost attention when
lifting or lowering the pump in the shaft as the rubbing together of
metallic parts can cause sparks.
•
To avoid cavitation problems caused by air aspiration, make sure
that the fluid entrance in the tank is not near the pump or pointed
towards it and that the difference between the entrance level of the
fluids and the minimum fluid allowed inside the tank is not exceeded.
•
The minimum level of fluid within the tank must never fall below the
top cover of the pump in order to ensure adequate cooling of the
motor.
•
In case of installation of models with cooling jacket or for which it is
allowed to be run dry, the minimum level of fluid can fall below the
top cover of the pump but must always be above the pump body in
order to avoid the formation of vortices with a consequent entry of
air.
•
Check that minimum level of fluid is correct also in relation to the
working point in order to obtain a smooth operation of the pump.
•
Make sure that the pump does not operate outside its characteristic
curve.
4.1 Free-standing installation (fig. 1 page 126) and
fixed installation (fig. 2 page 126)
Place into the bottom on the tank.
If the model does not have integrated support feet, the specific base
must be used to guarantee perfect stability for the pump and the cor
-
rect height of the aspiration tube.
4.1.1 Free-standing installation (fig. 1 page 126):
Use a hose union
to connect the pump’s delivery pipe to a flexible hose pipe which has
an internal diameter not less than that of the delivery pipe. A hose with
spiral reinforcement or a semi-rigid type is recommended to ensure
that the free passage remains constant even in bends or points where
it changes direction
4.1.2 Fixed installation (fig. 2 page 126):
Connect the pump to
Summary of Contents for DGN 250-300/2/G65V-65-80
Page 43: ...EL 43 better together 10 O ring OFF O R O R...
Page 64: ...BG 64 better together 10 OFF 9 4 20000 7000 9 5 20000 7000 9 6 O R O R...
Page 121: ...RU 121 better together 9 4 20000 7000 9 5 20000 7000 9 6 10 OFF...
Page 128: ...128 better together 13 DGF DRF MAF SMF GRF APF 13 DGN DRN MAN GRN APN A B C D E F A B C D E F...
Page 142: ...142 better together...
Page 143: ......
Page 144: ...zenit com better together Cod 27270101613200000 Rev 8 01 11 19...