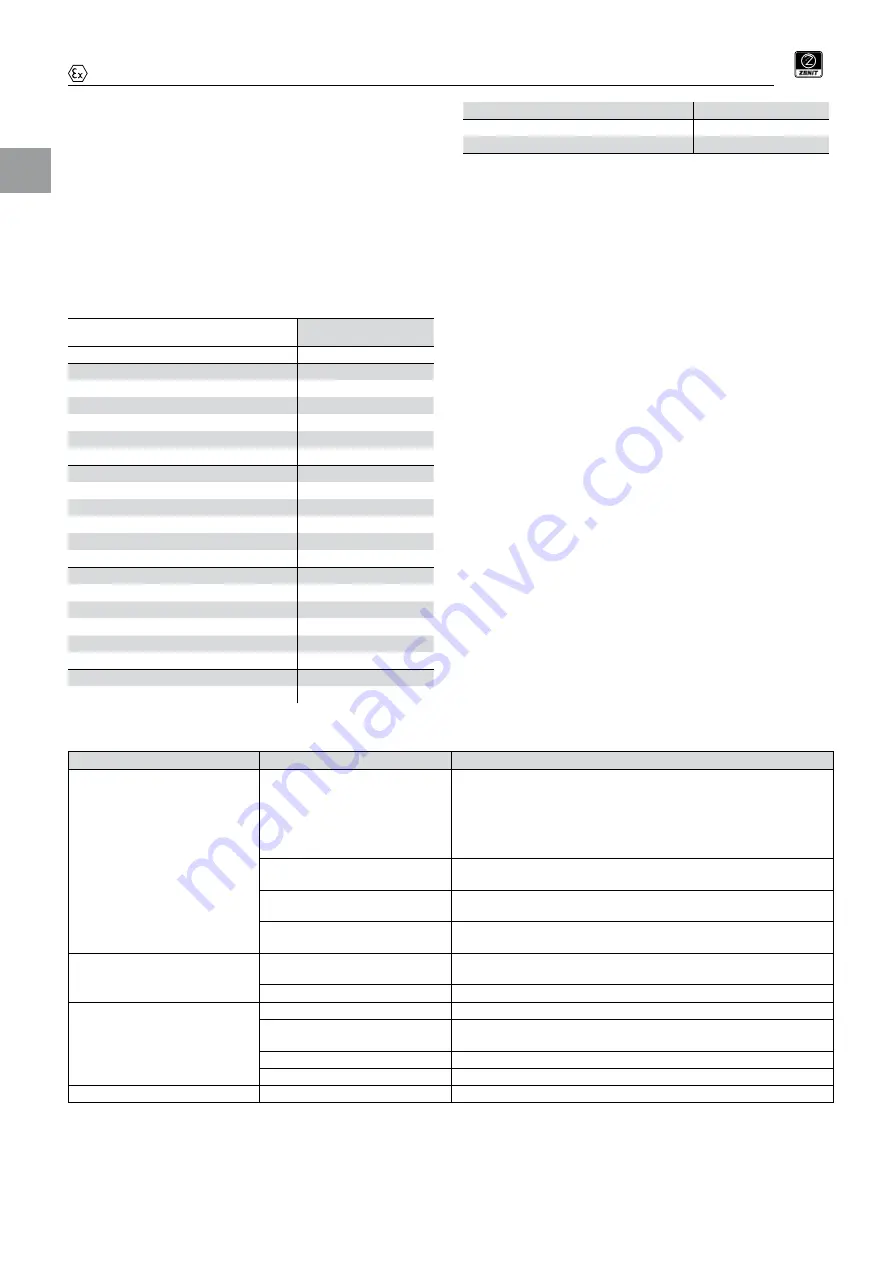
EN
12
better together
User and maintenance manual – Translation of original instructions
•
Check that the oil is free of water, this indicates that the mechanical
seal is still in good condition and the chamber can be refilled with
fresh oil;
•
If a very small quantity of water is detected in the bottom of the shaft,
this will be due to condensation and is considered normal, rather
than a sign of any fault with the mechanical seal;
•
If there is a substantial quantity of water in the oil chamber, the me
-
chanical seal needs to be inspected and perhaps replaced by a new
one;
•
Any replacement of the mechanical seal must be carried out by an
authorised Service Centre;
•
Fill the chamber completely with biodegradable oil, CASTROL PRO
-
DUCT L 320 or similar. If none of these oils are available, contact
Zenit.
The quantity of oil required is reported in the table.
Model
min
ml
max
ml
DGF - DRF - MAF - SMF - GRF - APF
195
210
DGN 250-300/2/G65V-65-80
395
430
DGN 400-550/2/65-80
600
650
DGN 200/4/65-80-100
600
650
DGN 300-400/4/65-80-100
905
980
DGN 150/6/65-80-100
600
650
DGN 250/6/100-150
905
980
DRN 250-300/2/65-80
395
430
DRN 400-550/2/65-80-100
600
650
DRN 200/4/80-100
600
650
DRN 300-400/4/80-100
905
980
DRN 150/6/80-100
600
650
DRN 250/6/100-150
905
980
MAN 250-300/2/G65V-65-80
395
430
MAN 400-550/2/65-80-100
600
650
MAN 200/4/80-100
600
650
MAN 300-400/4/80-100
905
980
MAN 150/6/80-100
600
650
MAN 250/6/100-150
905
980
GRN 250
-300
/2/G40H
395
430
GRN 400-550/2/G50H
905
980
GRN 300-400/4/80-100
905
980
APN 250-300/2/G40H
395
430
APN 400-550/2/G40H
905
980
•
Once finished, tighten the cap and re-install the pump.
9.4 Checking the bearings
The estimated length of safe operation of the bearings is 20,000 hours
of duty, after which they need to be replaced.
Check the state of the bearings every 7,000 hours and every working
year.
It the case where excessive noise, contact the said manufacturer or an
authorised Service Centre in order to obtain a replacement.
9.5 Mechanical Seals
The estimated length of safe operation of the mechanical seals is
20,000 hours of duty in normal conditions and 7,000 hours of duty in
abnormal operating conditions (dry or in presence of soiled liquids),
after which they need to be replaced.
9.6 Maintenance of the cooling system
•
Installation with a cooling jacket requires periodic maintenance in or
-
der to keep the gap between the body and the jacket clean and free
from encrusting. The frequency of maintenance intervention varies
depending on the liquid used for cooling.
•
To clean inside the jacket, proceed as follows:
•
undo the screws from the tightened sealing ring of the jacket and
remove;
•
unthread the jacket from the side of the pump motor, making sure
not to damage the cables or electrical connections;
•
thoroughly clean the inlet and drain pipes for cooling liquid, the O.R.
base, the external surface of the body and the inside of the cooling
jacket, taking care to remove any crusting;
•
throughout this operation, the cables remain inside the jacket, pay
utmost attention not to damage them;
•
replace the lubricated O.R. and mount them back into their place;
•
position the jacket into its place and fasten it with the sealing ring;
•
tighten the fastening screws in a “cross” order
10. TROUBLESHOOTING GUIDE
PROBLEM
CAUSE
REMEDY
The pump doesn’t work
Electrical protections tripping
Check the calibration of the protections.
Carry out an insulation test: if the result is negative, contact an autho
-
rised service centre for repair.
Impeller blocked: contact an authorized service centre.
In case of repeated protection tripping, contact an authorised service
centre.
Humidity sensor tripping
Contact an authorised service centre to verify the integrity of mechani
-
cal seals and O-ring.
Faulty level control
Check the correct operation of the float and if it can move freely or is
held in the OFF position.
Thermal protector tripping
Allow the pump to cool down and reset the thermal protector from the
electrical panel.
The thermal protection trips after
a short operating time
The pump is immersed in a liquid
which is too hot
Check the temperature of the liquid and allow to cool if necessary.
Wait until the pump has cooled.
Impeller blocked:
Contact an authorised service centre.
The pump works but the capacity
is reduced or nil
Foreign bodies inside the pump
Contact an authorised service centre.
Foreign bodies in the discharge
pipe or valve
Clean the hydraulic components.
Wrong direction of rotation
Invert the electrical connections of two of the three phases.
Gate valve partially closed
Fully open the gate valve.
Vibration or excessive noise
Bearing damaged or worn
Contact an authorised service centre.
Summary of Contents for DGN 250-300/2/G65V-65-80
Page 43: ...EL 43 better together 10 O ring OFF O R O R...
Page 64: ...BG 64 better together 10 OFF 9 4 20000 7000 9 5 20000 7000 9 6 O R O R...
Page 121: ...RU 121 better together 9 4 20000 7000 9 5 20000 7000 9 6 10 OFF...
Page 128: ...128 better together 13 DGF DRF MAF SMF GRF APF 13 DGN DRN MAN GRN APN A B C D E F A B C D E F...
Page 142: ...142 better together...
Page 143: ......
Page 144: ...zenit com better together Cod 27270101613200000 Rev 8 01 11 19...