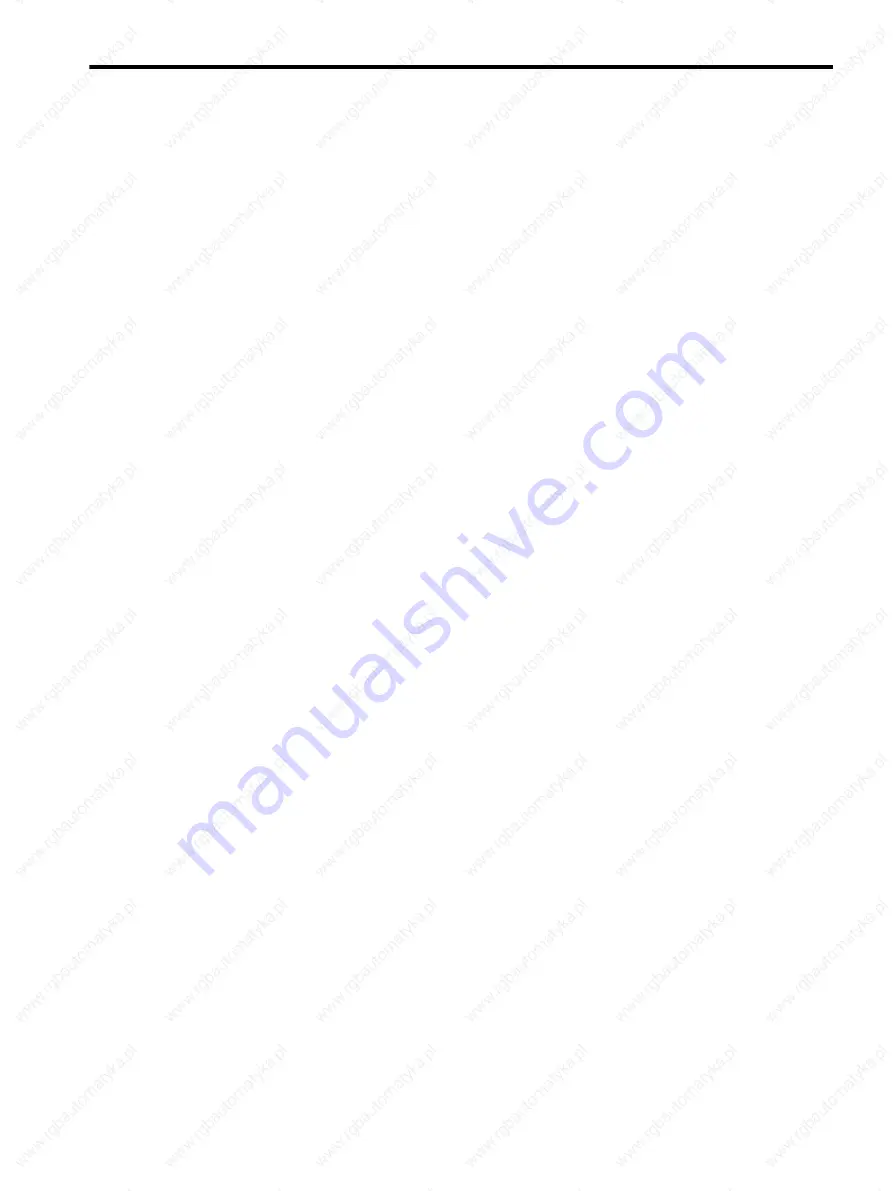
8.2 Normal Autotuning
8-7
8.2 Normal Autotuning
8.2.1 Normal Autotuning
Normal autotuning calculates the load moment of inertia during operation of the SERVOPACK and sets
parameters so that the servo gains consistent with the Machine Rigidity setting during normal (Fn001) are
achieved.
Normal autotuning may not be effective in the following cases.
• The load moment of inertia varies in less than 200 ms.
• The rotational speed is higher than 100 RPM or the acceleration reference is very even.
• Load rigidity is low and mechanical vibration occurs easily, such as a belt-driven mechanism, or a friction
is high.
• The speed reference is a stepwise reference.
If your system’s operation conditions include any of these above or the desired system performance could not be
obtained after having executed normal autotuning, try the following operations.
• Execute advanced autotuning.
• Set the Moment of Inertia Ratio (Pn103), and execute one-parameter autotuning or manual tuning.
The following utility function is also available for normal autotuning.
Fn007: Writes the load moment of the inertia calculation results obtained by normal autotuning to parameter
Pn103, and uses the result as the default value for the next calculation.
Summary of Contents for SGDS Sigma III Series
Page 3: ...SGDS Sigma III Servo Amplifier User Manual for Mechatrolink II Communications...
Page 21: ......
Page 59: ...2 System Selection 2 5 4 Regenerative Resistors 2 28...
Page 68: ...3 3 SERVOPACK Internal Block Diagrams 3 9 3 3 3 Three phase 200 V 1 0 kW...
Page 82: ...3 7 Dimensional Drawings of Base mounted SERVOPACK Model SGDS 12A 12A 3 23 Three phase 1 5kW...
Page 133: ...5 Wiring 5 7 2 Connecting Externally Regenerative Resistors 5 28...
Page 229: ...7 Operation 7 7 4 Absolute Encoder Home Position Offset 7 38...