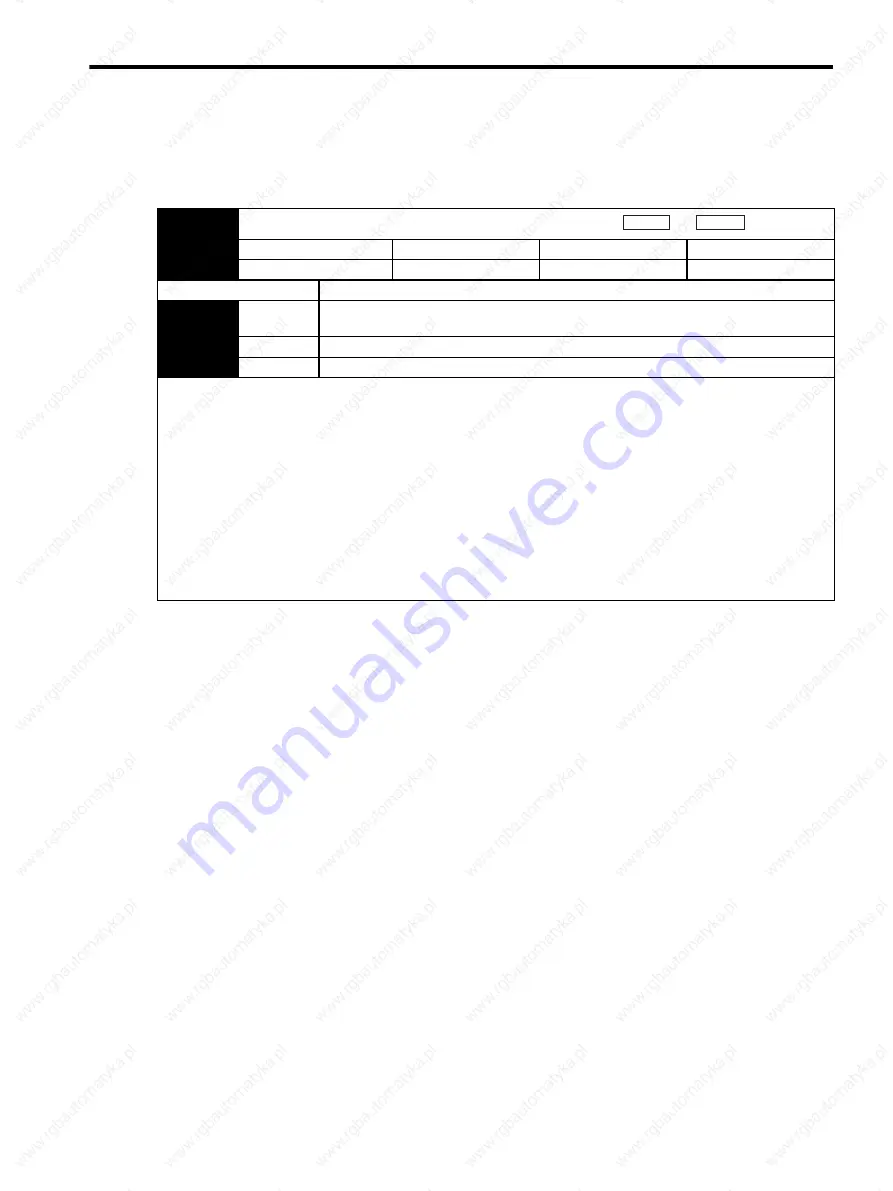
8.2 Normal Autotuning
8-9
8.2.3 Selecting the Normal Autotuning Execution Method
There are three methods that can be used for normal autotuning: At start of operation, constantly, and none. The
selection method is described next.
Pn110
Normal Autotuning Switches
Setting Range
Setting Unit
Factory Setting
Setting Validation
−
−
0012
Required
Parameter Meaning
Pn110
n.
0
Normal autotuning is preformed only after the first time power is turned ON. (Factory
Setting)
n.
1
Normal autotuning (moment of inertia calculations) are performed continuously.
n.
2
Normal autotuning is not performed.
The factory setting is n.
0. This setting is recommended for applications in which the load moment of inertia does not
change much or if the load moment of inertia is not known. The moment of inertia calculated at the beginning of operation
is used continuously. In this case, differences in machine status and operation references at the beginning of operation may
cause minor differences in the calculation results of the load moment of inertia, causing differences in the SERVOPACK
responsiveness each time the power supply is turned ON. If this occurs, overwrite Pn103 (Moment of Inertia Ratio) with the
load moment of inertia in Fn007 (Save moment of inertia ratio data obtained from normal autotuning) and set Pn110 to
n.
2 to disable normal autotuning.
The setting n.
1 is used when the load moment of inertia varies constantly. This setting enables a consistent
responsiveness even when the load moment of inertia changes. If the load moment of inertia changes in less than 200 ms,
however, the autotuning accuracy will deteriorate, in which case Pn110.0 should be set to 0 or 2.
The setting n.
2 is used when normal autotuning is not possible, when the load moment of inertia is known and the
moment of inertia ratio is set in Pn103 to perform advanced autotuning with Fn017 or one-parameter autotuning with
Fn01A, when performing adjustments manually, or any other time the normal autotuning function is not going to be used.
Speed
Position
Summary of Contents for SGDS Sigma III Series
Page 3: ...SGDS Sigma III Servo Amplifier User Manual for Mechatrolink II Communications...
Page 21: ......
Page 59: ...2 System Selection 2 5 4 Regenerative Resistors 2 28...
Page 68: ...3 3 SERVOPACK Internal Block Diagrams 3 9 3 3 3 Three phase 200 V 1 0 kW...
Page 82: ...3 7 Dimensional Drawings of Base mounted SERVOPACK Model SGDS 12A 12A 3 23 Three phase 1 5kW...
Page 133: ...5 Wiring 5 7 2 Connecting Externally Regenerative Resistors 5 28...
Page 229: ...7 Operation 7 7 4 Absolute Encoder Home Position Offset 7 38...