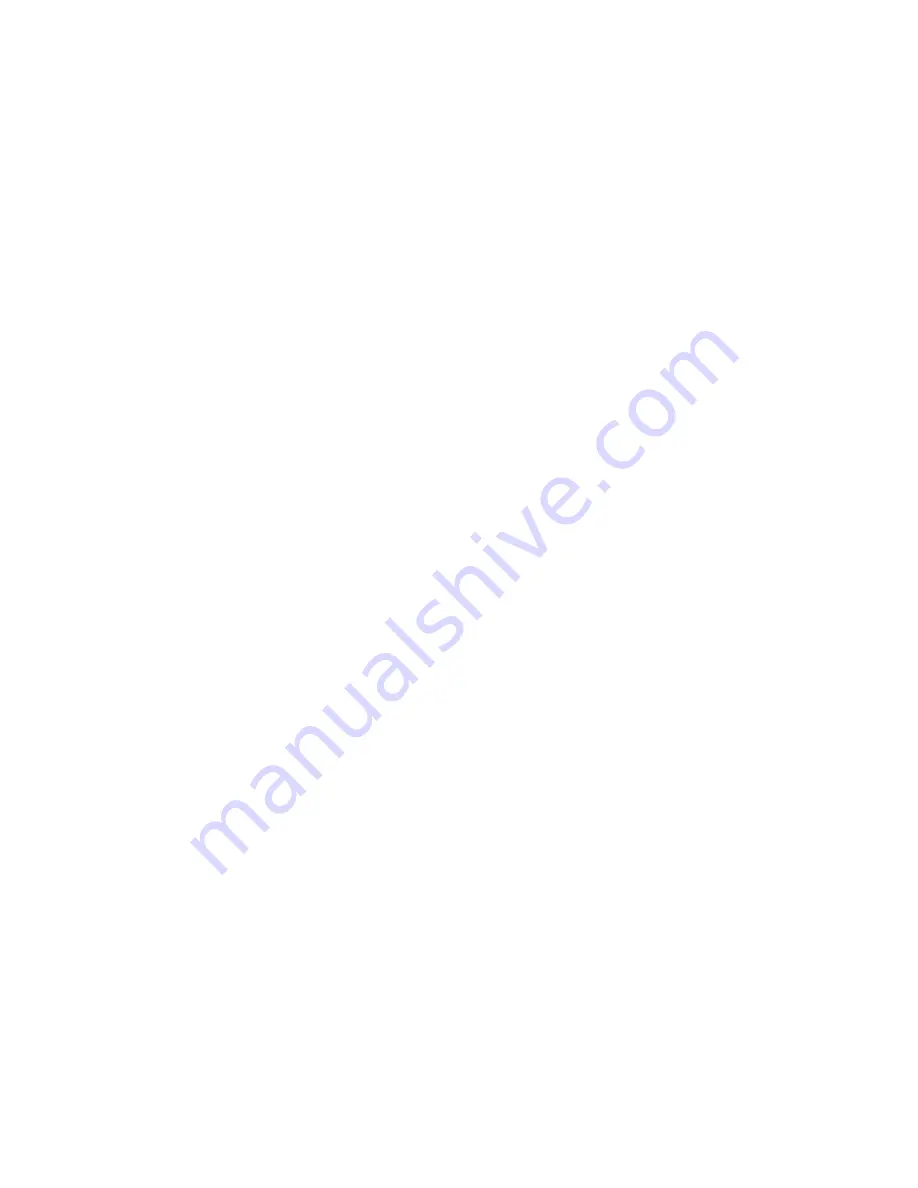
Physical Installation 1 - 8
Bypass Product Options
Option C
Motor Circuit Protector (MCP)/Disconnect: Replaces the standard input disconnect switch and provides short circuit protection
integral with the Drive and Bypass package. The MCP includes a through the door, padlockable operator mechanism. Without
this option, short circuit protection must be provided by others on the input side of the Drive and Bypass unit.
Option F
Drive Input Fuses: Fuses capable of protecting semiconductor devices, rated at 200 kAIC are connected to the line side of the
Drive, between the input disconnect and the Drive, to protect the Drive semiconductors when motor or output conductor short
circuit faults occur.
Option G
Drive Input Disconnect Switch: Provides a disconnect means for the input side of the Drive, for Drive isolation capability
during Bypass operation. This disconnect is located inside the enclosure with no external handle.
Option H
Drive Input Fused Disconnect Switch: Provides both a disconnect means and short circuit protection for the input side of the
Drive. A combination of options F and G.
Option J
Enable Embedded Serial Communications: A no cost option. The Drive in a Bypass unit is capable of network communication
via one of 3 embedded protocols. Specifying option J will enable the Metasys N2 protocol and will provide the necessary
parameter settings and wiring (jumpers) to be network ready when delivered (Project specific H5-0X parameters are setup by
the user).
Option L
Serial Communication, Echelon LonWorks: An isolated RS-422/485 circuit board provides LonTalk protocol for network
communication to a BAS. This option plugs into the CN2 connection on the Drive control circuit board.
Option N
Input Capacitive Network Radio Frequency Interference Filter: Electronic equipment can be sensitive to low levels of voltage
distortion and electrical noise. This passive wye-delta capacitve filter is intended for installation on the VFD input in order to
protect other sensitive electronic loads, it provides attenuation of conducted RFI and EMI.
Option P
Pressure to Electrical Transducer: This transducer is employed when converting a pneumatic signal to an electrical signal for
use as the Drive speed command input. The need for this option comes up on retrofit applications when the pneumatic signal
that formerly controlled the pneumatic actuator on Inlet Guide Vanes (IGV), for example, is now to be used to control the fan
speed via the Drive. This option is wired to terminals TB5-7, TB5-8 and TB5-9, parameters H3-10 and H3-11 are used for
final field calibration of this input if there is jobsite variation from the typical 3 to 15 PSIG pneumatic signal input range.
Option R
3% Input Line Reactor: Employed on the input side of the Drive for Total Harmonic Distortion (THD) suppression. A line
reactor also minimizes the potential for Drive input diode damage from line transients and reduces voltage peaks on the DC
bus capacitors. This option is installed on the input power side of the Drive, between the input contactor and the Drive.
Summary of Contents for E7LBA002
Page 1: ...E7L Drive Bypass Technical Manual Model E7L Document Number TM E7L 01 ...
Page 8: ...Introduction vi Notes ...
Page 12: ...Table of Contents x Notes ...
Page 54: ...Electrical Installation 2 22 Wiring Diagram ...
Page 55: ...Electrical Installation 2 23 ...
Page 87: ...Start Up and Operation 4 9 Notes ...
Page 202: ...Diagnostic Troubleshooting 6 30 Notes ...
Page 248: ...Capacity Related Parameters B 6 Notes ...
Page 279: ...Communications D 27 Note ...
Page 280: ...Communications D 28 ...
Page 292: ...Spare Parts F 6 ...
Page 304: ...Index 12 ...
Page 305: ......