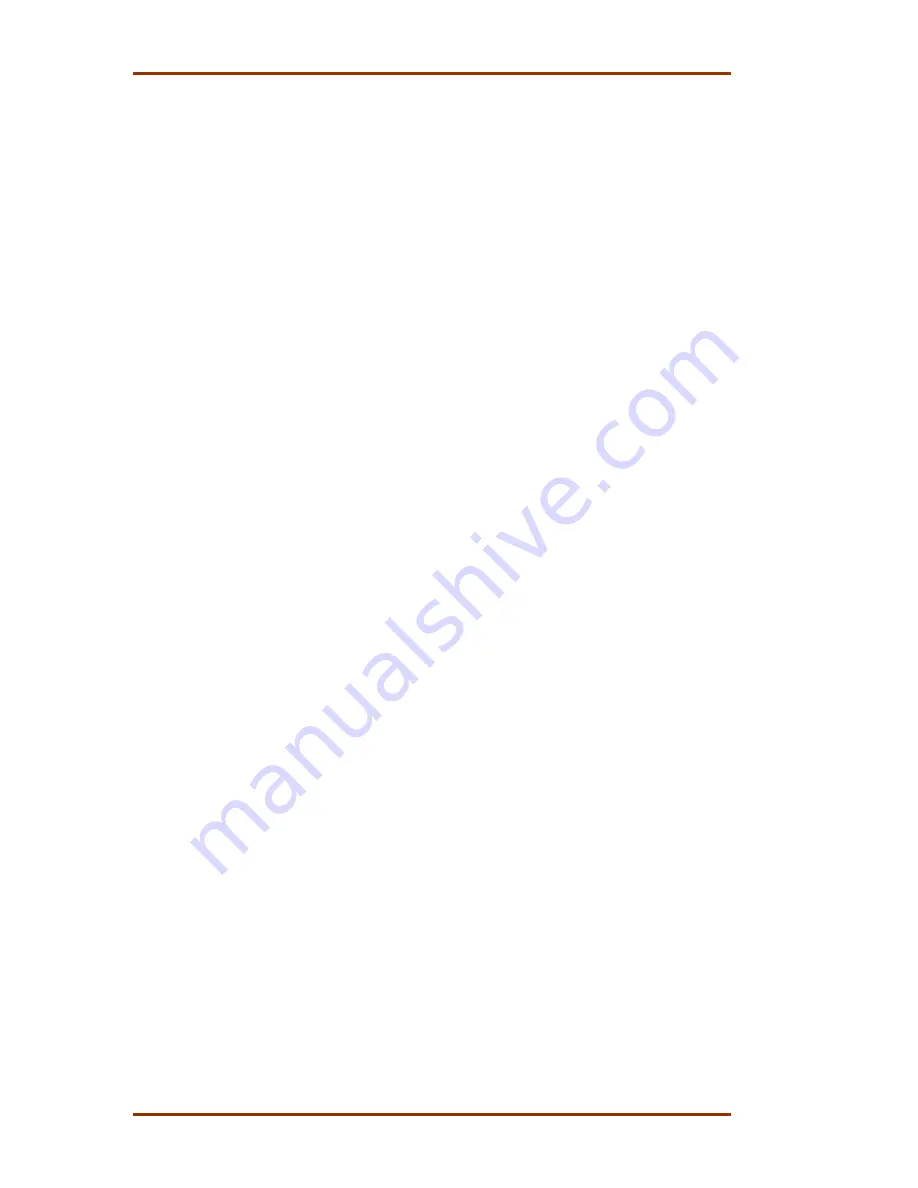
5009 Installation/Hardware
Manual 85580V2
54
Woodward
•
SIO-A port 2 (RS-232) functions as an interface port to Woodward’s
servPanel program.
•
SIO-A port 3 (RS-232/422/485) functions as Modbus #1 port 1.
•
SIO-A port 4 (RS-232/422/485) functions as Modbus #2 port 1 or DDE
communication for PCI.
•
SIO-B Port 1 (RS-232) functions as an Alarm/Trip Printer driver port
•
SIO-B port 2 (RS-232) functions as an interface port to Woodward’s
servPanel program.
•
SIO-B port 3 (RS-232/422/485) functions as Modbus #1 port 2 or DDE
communication for PCI.
•
SIO-B port 4 (RS-232/422/485) functions as Modbus #2 port 2.
All communication ports can interface with other devices via RS-232
communication. RS-232 communication is limited to a distance of 15 m (50 ft). In
cases where a device which is being interfaced to is located a distance of greater
than 15 m (50 ft) from the control, it is recommended to use SIO cards. It is
possible also to use RS-232 to RS-422/485 converters. CPU communication
ports are considered less reliable than SIO port. As a consequence, if Modbus
communication is used as a main interface device, it is recommended to use SIO
cards. If Modbus redundant lines are required, it is recommended to use SIO
cards.
RS-422 and RS-485 communication support multidropping (multiple slaves on a
single communication line); RS-232 communication does not.
To allow an RS-232 based port to reach farther than 15 m/50 ft, a Model 285
Superverter from Telebyte Technology Inc. of Greenlawn NY, or equivalent, can
be used as an RS-422 or RS-485 interface converter. RS-422 and RS-485
communications also support multidropping (multiple slaves on a single
communications line); RS-232 communications does not.
Each SIO module includes four serial ports. Ports 1 and 2 are RS-232
communications based ports only. Ports 3 and 4 can be configured for RS-232,
RS-422, or RS-485 communications. With the use of RS-422 or RS-485
communications, the control can interface with a device through serial
communications up to 1219 m (4000 ft) from the control. Alternatively one or two
SIO modules may be installed within the control’s chassis.
Figures 4-16 and 4-17 show the control’s communication port connections. The
5009 control can simultaneously communicate with up to four Modbus based
devices via the CPU-A port, CPU-B port, SIO-A port 3, and SIO-B port 3 using
ASCII or RTU Modbus transmission protocols. Refer to Volume 3 of this manual
for a list of all the Modbus commands and parameters available.
The CPU-C port is dedicated for DDE communications and is intended to be
used as the main interface with the system engineering workstation (PCI
program software loaded onto a computer). Optionally port 4 on any installed
SIO module may also be used for DDE communications. Refer to Volume 3 of
this manual for details on DDE communications and the PCI program. An
RS-232 based null-modem cable (W20) is provided with the system to use when
interfacing between a computer and the control. Upon a failure of the CPU-C port
or kernel-C CPU, the control can be configured to use the CPU-B port as the PCI
interface port.
Three port filter assemblies (one per CPU) are provided with each system to
protect the CPU from external system noise. These filter assemblies are shipped
separately from the control and can be easily installed if use of the CPU port is
required. Refer to Chapter 2 of this volume for installation instructions.
Summary of Contents for MicroNet TMR 5009
Page 8: ...5009 Installation Hardware Manual 85580V2 vi Woodward...
Page 23: ...Manual 85580V2 5009 Installation Hardware Woodward 15 Figure 3 1 Hardware Identification...
Page 33: ...Manual 85580V2 5009 Installation Hardware Woodward 25 Figure 3 7 DIN Rail ATM Outline Drawing...
Page 35: ...Manual 85580V2 5009 Installation Hardware Woodward 27 Figure 3 9 DTM Outline Drawing...
Page 36: ...5009 Installation Hardware Manual 85580V2 28 Woodward Figure 3 10 DTM Mounting Configuration...
Page 68: ...5009 Installation Hardware Manual 85580V2 60 Woodward Figure 4 19 System Cable Layout Diagram...
Page 69: ...Manual 85580V2 5009 Installation Hardware Woodward 61 Figure 4 20 Power Supply Wiring Diagram...
Page 70: ...5009 Installation Hardware Manual 85580V2 62 Woodward Figure 4 21 ATM 1 Wiring Diagram...
Page 71: ...Manual 85580V2 5009 Installation Hardware Woodward 63 Figure 4 22 ATM 2 Wiring Diagram...
Page 72: ...5009 Installation Hardware Manual 85580V2 64 Woodward Figure 4 23 DTM 1 Wiring Diagram...
Page 73: ...Manual 85580V2 5009 Installation Hardware Woodward 65 Figure 4 24 DTM 2 Wiring Diagram...
Page 74: ...5009 Installation Hardware Manual 85580V2 66 Woodward Figure 4 25 DTM 3 Wiring Diagram...
Page 75: ...Manual 85580V2 5009 Installation Hardware Woodward 67 Figure 4 26 DTM 4 Wiring Diagram...
Page 89: ...Manual 85580V2 5009 Installation Hardware Woodward 81 Table 5 3 Discrete In Cable Connections...
Page 90: ...5009 Installation Hardware Manual 85580V2 82 Woodward Table 5 4 Relay Cable Connections...
Page 91: ...Manual 85580V2 5009 Installation Hardware Woodward 83 Table 5 4 Relay Cable Connections cont...
Page 92: ...5009 Installation Hardware Manual 85580V2 84 Woodward Table 5 5 Analog Combo Module...
Page 103: ...Manual 85580V2 5009 Installation Hardware Woodward 95 Figure 8 2 Operator Control Panel...
Page 108: ...5009 Installation Hardware Manual 85580V2 100 Woodward Figure 8 6 Real Power Sensor...
Page 115: ......
Page 116: ...Declarations...
Page 117: ......