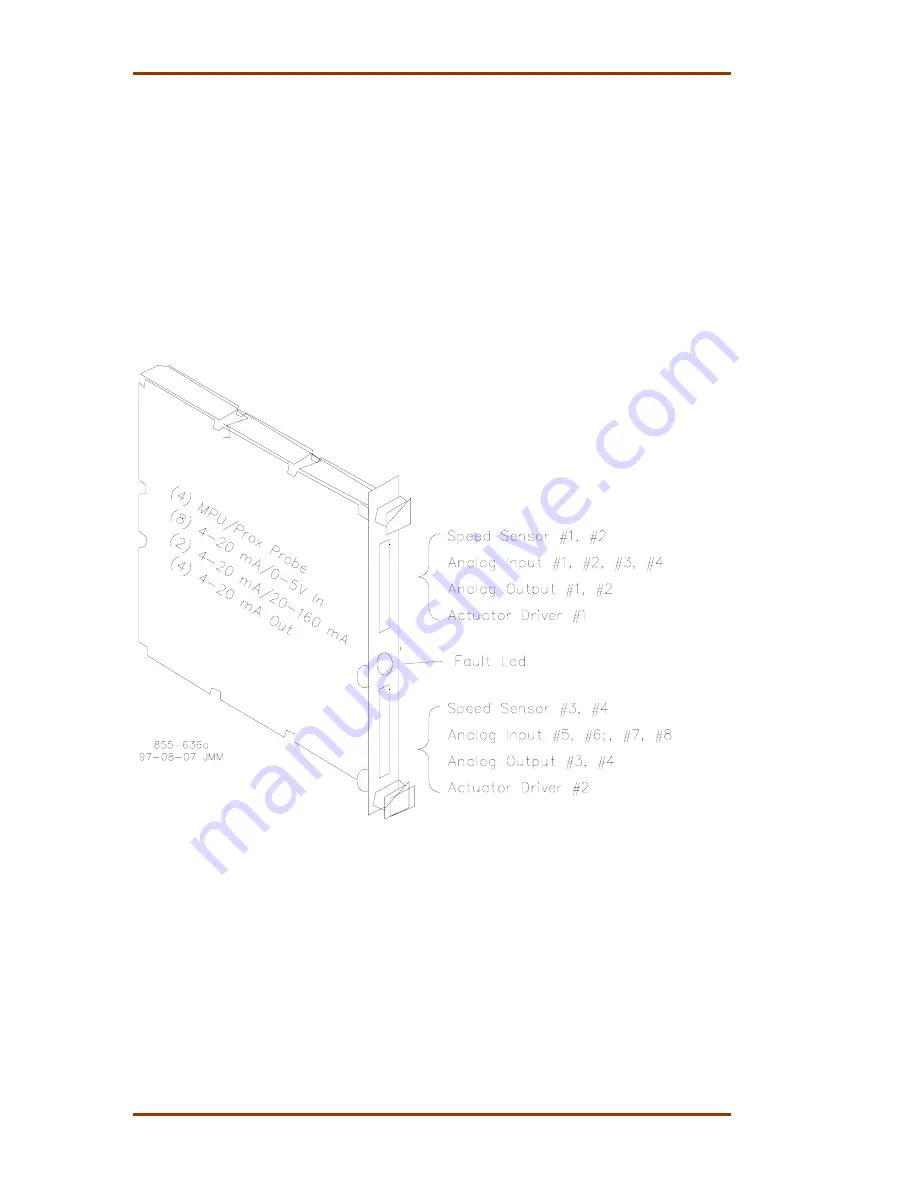
5009 Installation/Hardware
Manual 85580V2
8
Woodward
MPU and Analog I/O Module (A3)
Each analog module contains circuitry for four speed sensor inputs, eight analog
inputs, four analog outputs, and two proportional actuator outputs. An on-board
micro-controller scales inputs and outputs using calibration constants stored in
EEPROM, and schedules outputs to occur at the proper time. Refer to Figure
2-5. This module includes no potentiometers and requires no calibration. When a
channel or module fault is detected, the control annunciates the fault, disables
the channel or module and does not use the channel/module’s data in system
calculations or control.
Each CPU sends and receives information to and from its respective MPU &
Analog I/O module via the VME bus. Each input value is stored in a register and
addressed by the CPU as required. Outputs are driven by the CPU, through the
module’s associated output drivers.
Figure 2-5. MPU and Analog I/O Module
Analog Termination Modules
Analog Termination Modules (ATMs) mount external to the 5009 chassis on a
standard DIN rail. The analog termination modules are used to connect analog
field wiring to the 5009 control. An ATM houses circuitry to:
•
route each input signal to the system’s three independent (rack mounted)
analog modules
•
produce each output signal by summing the three independent analog
modules’ respective outputs
Summary of Contents for MicroNet TMR 5009
Page 8: ...5009 Installation Hardware Manual 85580V2 vi Woodward...
Page 23: ...Manual 85580V2 5009 Installation Hardware Woodward 15 Figure 3 1 Hardware Identification...
Page 33: ...Manual 85580V2 5009 Installation Hardware Woodward 25 Figure 3 7 DIN Rail ATM Outline Drawing...
Page 35: ...Manual 85580V2 5009 Installation Hardware Woodward 27 Figure 3 9 DTM Outline Drawing...
Page 36: ...5009 Installation Hardware Manual 85580V2 28 Woodward Figure 3 10 DTM Mounting Configuration...
Page 68: ...5009 Installation Hardware Manual 85580V2 60 Woodward Figure 4 19 System Cable Layout Diagram...
Page 69: ...Manual 85580V2 5009 Installation Hardware Woodward 61 Figure 4 20 Power Supply Wiring Diagram...
Page 70: ...5009 Installation Hardware Manual 85580V2 62 Woodward Figure 4 21 ATM 1 Wiring Diagram...
Page 71: ...Manual 85580V2 5009 Installation Hardware Woodward 63 Figure 4 22 ATM 2 Wiring Diagram...
Page 72: ...5009 Installation Hardware Manual 85580V2 64 Woodward Figure 4 23 DTM 1 Wiring Diagram...
Page 73: ...Manual 85580V2 5009 Installation Hardware Woodward 65 Figure 4 24 DTM 2 Wiring Diagram...
Page 74: ...5009 Installation Hardware Manual 85580V2 66 Woodward Figure 4 25 DTM 3 Wiring Diagram...
Page 75: ...Manual 85580V2 5009 Installation Hardware Woodward 67 Figure 4 26 DTM 4 Wiring Diagram...
Page 89: ...Manual 85580V2 5009 Installation Hardware Woodward 81 Table 5 3 Discrete In Cable Connections...
Page 90: ...5009 Installation Hardware Manual 85580V2 82 Woodward Table 5 4 Relay Cable Connections...
Page 91: ...Manual 85580V2 5009 Installation Hardware Woodward 83 Table 5 4 Relay Cable Connections cont...
Page 92: ...5009 Installation Hardware Manual 85580V2 84 Woodward Table 5 5 Analog Combo Module...
Page 103: ...Manual 85580V2 5009 Installation Hardware Woodward 95 Figure 8 2 Operator Control Panel...
Page 108: ...5009 Installation Hardware Manual 85580V2 100 Woodward Figure 8 6 Real Power Sensor...
Page 115: ......
Page 116: ...Declarations...
Page 117: ......