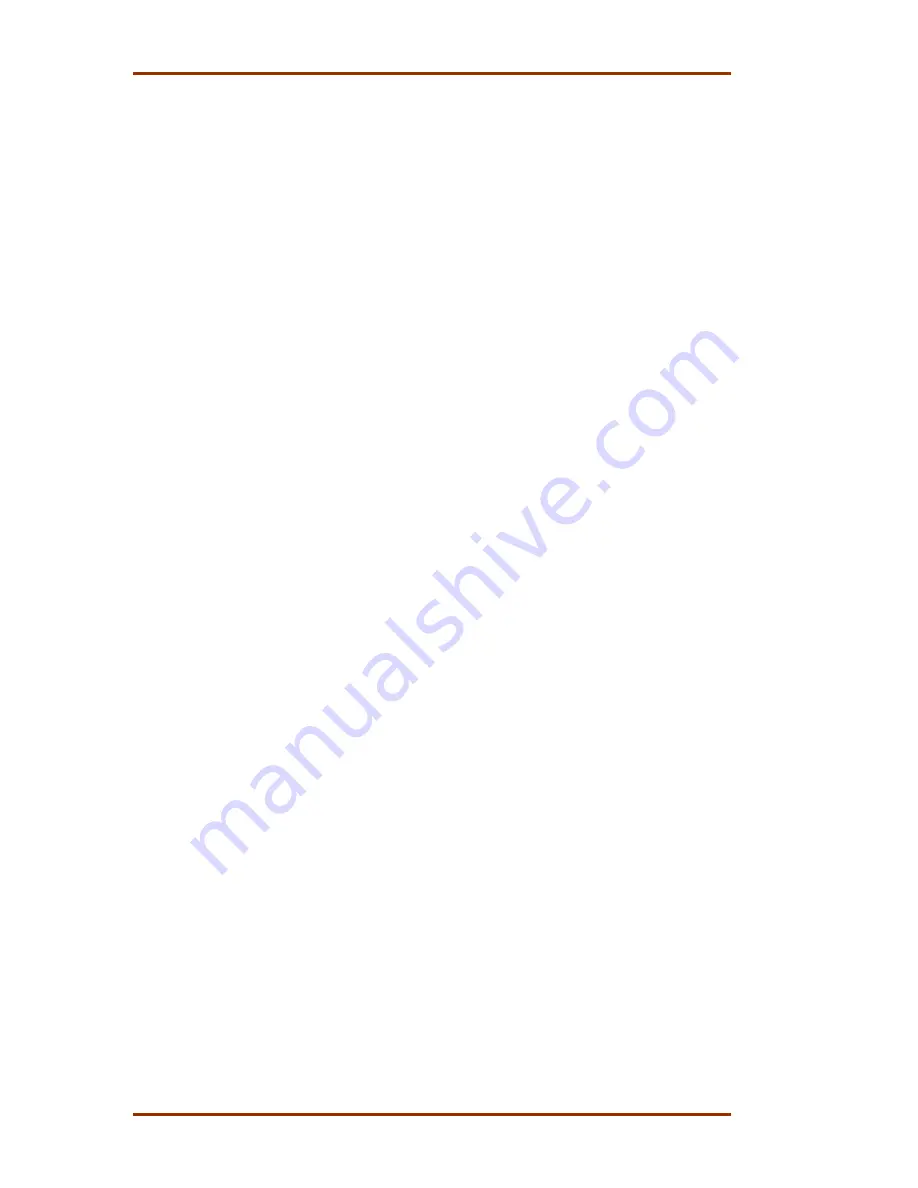
5009 Installation/Hardware
Manual 85580V2
46
Woodward
•
The combined current draw through terminals 27, 28, 29, 30, 31, and 32
cannot exceed 400 mA or the Discrete I/O module’s on-board power
converter will current limit.
•
It is recommended that 0.75 mm² (20 AWG) or larger wire be used between
each discrete input and the DTM.
•
DTM terminals accept wires from 0.08–2.5 mm² (27–12 AWG) wire.
•
If 125 Vdc Contact Power is used, the Power Supply must meet IEC 6164-1,
Overvoltage Category II.
•
With the use of 125 Vdc contact power, it is recommended that the contact
power be removed before connecting or disconnecting any 5009-to-DTM
cable.
DTM Relay Outputs (F/T Relay Outputs)
There are twelve relay outputs available from the 5009 control, with three outputs
per DTM. Of the available relay outputs, two are dedicated to functions, and the
other ten are user-configurable. The dedicated outputs are:
•
Shutdown relay—De-energizes for any shutdown condition
•
Alarm relay—Energizes for any alarm condition
The remaining ten relay outputs can be programmed to energize upon a function
change of state or an analog value level. Applications requiring programmable
relay outputs must have the desired switch condition or specific analog value
assigned to them within the control’s program. Refer to Volume 3 of this manual
for a complete list of programmable relay output options.
The 5009 control system does not have the capability to provide circuit power to
external circuits interfacing with a relay output. All external circuits interfacing
with control relay outputs must have circuit power provided externally. All relays
are dust-tight, magnetic blow-out type relays with Form-C type contacts.
Refer to Chapter 6 of this volume for all relay ratings.
Latent Fault Detection
Because a fault tolerant system can tolerate a single fault, it is possible for this
fault to go undetected. This is called a latent fault. If another fault occurs when a
latent fault exists, it could cause a shutdown. This is why it is important to detect
latent faults in a fault tolerant system.
Each relay output can be individually configured to use latent fault detection to
identify relay failures without affecting a relay output’s state. A fault tolerant relay
configuration consists of 6 relays, driven by two discrete outputs from each
kernel. The relays are configured in three legs of two relays each. See Figure
4-15. Customer circuit power is connected to one side of the resulting
configuration, and customer load to the other side. Field selectable jumpers,
located on system DTMs, are provided to allow each output’s latent fault
detection logic to be compatible with the circuit being interfaced to.
Six individual relays make up one relay output. When a relay output is closed,
the contacts of all six relays are closed. Because of the series-parallel
configuration that the relays are in, the failure of any two individual relays will not
cause the output to be open. The relay output would continue to be closed. Once
a relay output is closed, the output’s individual relays are periodically opened and
re-closed, to ensure that they were in the correct state, and that they change
state.
Summary of Contents for MicroNet TMR 5009
Page 8: ...5009 Installation Hardware Manual 85580V2 vi Woodward...
Page 23: ...Manual 85580V2 5009 Installation Hardware Woodward 15 Figure 3 1 Hardware Identification...
Page 33: ...Manual 85580V2 5009 Installation Hardware Woodward 25 Figure 3 7 DIN Rail ATM Outline Drawing...
Page 35: ...Manual 85580V2 5009 Installation Hardware Woodward 27 Figure 3 9 DTM Outline Drawing...
Page 36: ...5009 Installation Hardware Manual 85580V2 28 Woodward Figure 3 10 DTM Mounting Configuration...
Page 68: ...5009 Installation Hardware Manual 85580V2 60 Woodward Figure 4 19 System Cable Layout Diagram...
Page 69: ...Manual 85580V2 5009 Installation Hardware Woodward 61 Figure 4 20 Power Supply Wiring Diagram...
Page 70: ...5009 Installation Hardware Manual 85580V2 62 Woodward Figure 4 21 ATM 1 Wiring Diagram...
Page 71: ...Manual 85580V2 5009 Installation Hardware Woodward 63 Figure 4 22 ATM 2 Wiring Diagram...
Page 72: ...5009 Installation Hardware Manual 85580V2 64 Woodward Figure 4 23 DTM 1 Wiring Diagram...
Page 73: ...Manual 85580V2 5009 Installation Hardware Woodward 65 Figure 4 24 DTM 2 Wiring Diagram...
Page 74: ...5009 Installation Hardware Manual 85580V2 66 Woodward Figure 4 25 DTM 3 Wiring Diagram...
Page 75: ...Manual 85580V2 5009 Installation Hardware Woodward 67 Figure 4 26 DTM 4 Wiring Diagram...
Page 89: ...Manual 85580V2 5009 Installation Hardware Woodward 81 Table 5 3 Discrete In Cable Connections...
Page 90: ...5009 Installation Hardware Manual 85580V2 82 Woodward Table 5 4 Relay Cable Connections...
Page 91: ...Manual 85580V2 5009 Installation Hardware Woodward 83 Table 5 4 Relay Cable Connections cont...
Page 92: ...5009 Installation Hardware Manual 85580V2 84 Woodward Table 5 5 Analog Combo Module...
Page 103: ...Manual 85580V2 5009 Installation Hardware Woodward 95 Figure 8 2 Operator Control Panel...
Page 108: ...5009 Installation Hardware Manual 85580V2 100 Woodward Figure 8 6 Real Power Sensor...
Page 115: ......
Page 116: ...Declarations...
Page 117: ......