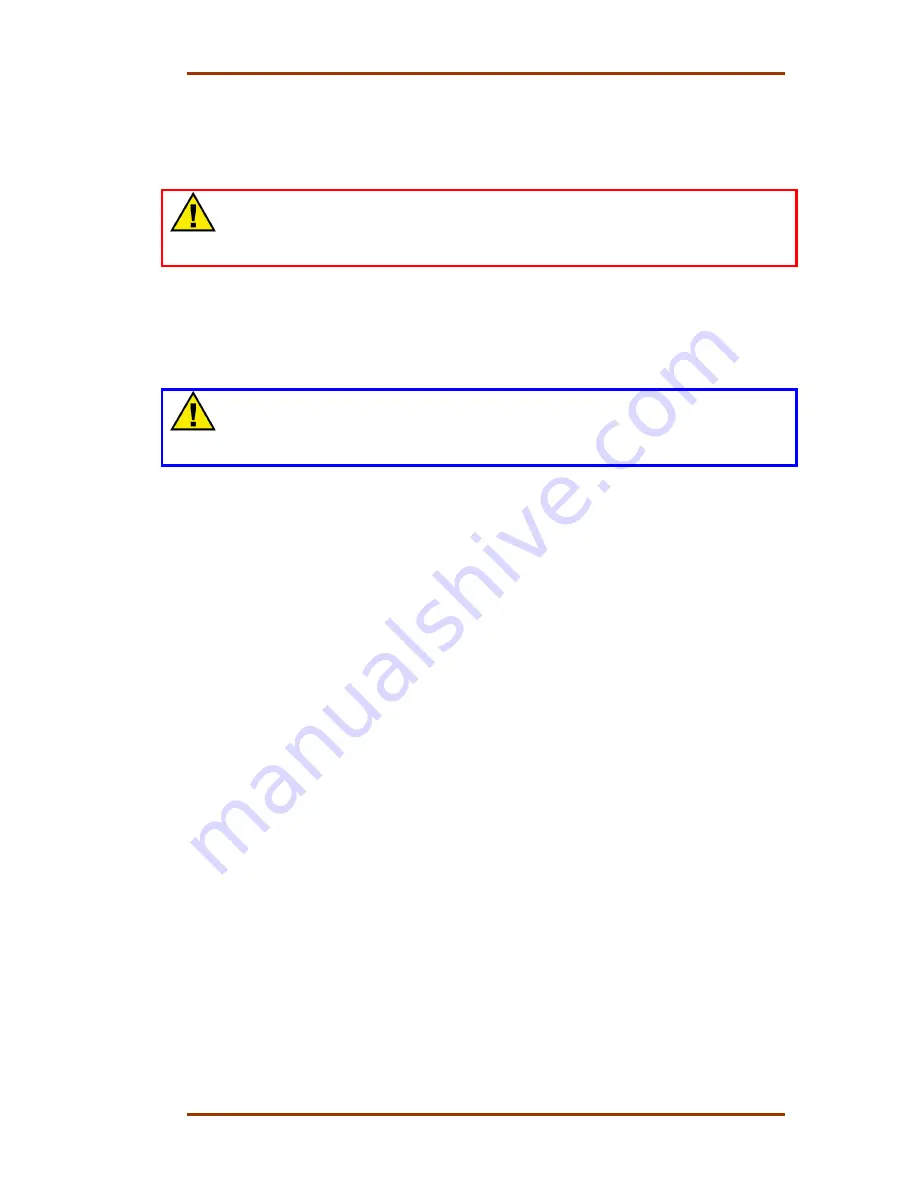
Manual 85580V2
5009 Installation/Hardware
Woodward
11
•
route each contact input signal to the system’s three independent (rack
mounted) discrete modules
•
provide an open / closed contact output based on associated discrete
module commands
•
indicate the health of all relays (latent fault detection)
WARNING—HAZARDOUS LOCATIONS
This equipment is not suitable for use in Class I, Division 2 hazardous
locations if an F/T Relay module is installed in the cabinet. It must be used in
ordinary or non-hazardous locations only.
Discrete input power (contact wetting voltage) can be supplied by the 5009
control or from an external source. The 5009 control provides an isolated 24 Vdc
power source for contact wetting. The external source may be 24 Vdc or 125 Vdc
(North American installations only). Separate discrete input terminals are
provided based on the level of contact wetting voltage used. See Figure 4-9.
CAUTION—MAXIMUM VOLTAGE
To comply with CE Marking under the European Low Voltage Directive
(LVD), the maximum external circuit voltage for both the Discrete Inputs and
Relay Output circuit are limited to 18–32 Vdc maximum.
The discrete output relays are mounted on sockets, with 18 relays per DTM. Six
relays, are used to create each relay output (normally open and normally closed
contacts) and allow latent fault detection. See Figure 4-15. This configuration
allows independent testing of each relay output (latent fault detection) without
concern of relay position. Customer power is connected to one side of the
configuration and load to the other.
Discrete outputs can be configured to use latent fault detection to identify output
relay failures without affecting operation. When the contacts are closed, they are
periodically opened in pairs, to ensure that they are in the correct state, and that
they change state. When they are open, they are periodically closed individually,
to ensure that they close. Any failures are annunciated, and further testing is
disabled.
Summary of Contents for MicroNet TMR 5009
Page 8: ...5009 Installation Hardware Manual 85580V2 vi Woodward...
Page 23: ...Manual 85580V2 5009 Installation Hardware Woodward 15 Figure 3 1 Hardware Identification...
Page 33: ...Manual 85580V2 5009 Installation Hardware Woodward 25 Figure 3 7 DIN Rail ATM Outline Drawing...
Page 35: ...Manual 85580V2 5009 Installation Hardware Woodward 27 Figure 3 9 DTM Outline Drawing...
Page 36: ...5009 Installation Hardware Manual 85580V2 28 Woodward Figure 3 10 DTM Mounting Configuration...
Page 68: ...5009 Installation Hardware Manual 85580V2 60 Woodward Figure 4 19 System Cable Layout Diagram...
Page 69: ...Manual 85580V2 5009 Installation Hardware Woodward 61 Figure 4 20 Power Supply Wiring Diagram...
Page 70: ...5009 Installation Hardware Manual 85580V2 62 Woodward Figure 4 21 ATM 1 Wiring Diagram...
Page 71: ...Manual 85580V2 5009 Installation Hardware Woodward 63 Figure 4 22 ATM 2 Wiring Diagram...
Page 72: ...5009 Installation Hardware Manual 85580V2 64 Woodward Figure 4 23 DTM 1 Wiring Diagram...
Page 73: ...Manual 85580V2 5009 Installation Hardware Woodward 65 Figure 4 24 DTM 2 Wiring Diagram...
Page 74: ...5009 Installation Hardware Manual 85580V2 66 Woodward Figure 4 25 DTM 3 Wiring Diagram...
Page 75: ...Manual 85580V2 5009 Installation Hardware Woodward 67 Figure 4 26 DTM 4 Wiring Diagram...
Page 89: ...Manual 85580V2 5009 Installation Hardware Woodward 81 Table 5 3 Discrete In Cable Connections...
Page 90: ...5009 Installation Hardware Manual 85580V2 82 Woodward Table 5 4 Relay Cable Connections...
Page 91: ...Manual 85580V2 5009 Installation Hardware Woodward 83 Table 5 4 Relay Cable Connections cont...
Page 92: ...5009 Installation Hardware Manual 85580V2 84 Woodward Table 5 5 Analog Combo Module...
Page 103: ...Manual 85580V2 5009 Installation Hardware Woodward 95 Figure 8 2 Operator Control Panel...
Page 108: ...5009 Installation Hardware Manual 85580V2 100 Woodward Figure 8 6 Real Power Sensor...
Page 115: ......
Page 116: ...Declarations...
Page 117: ......