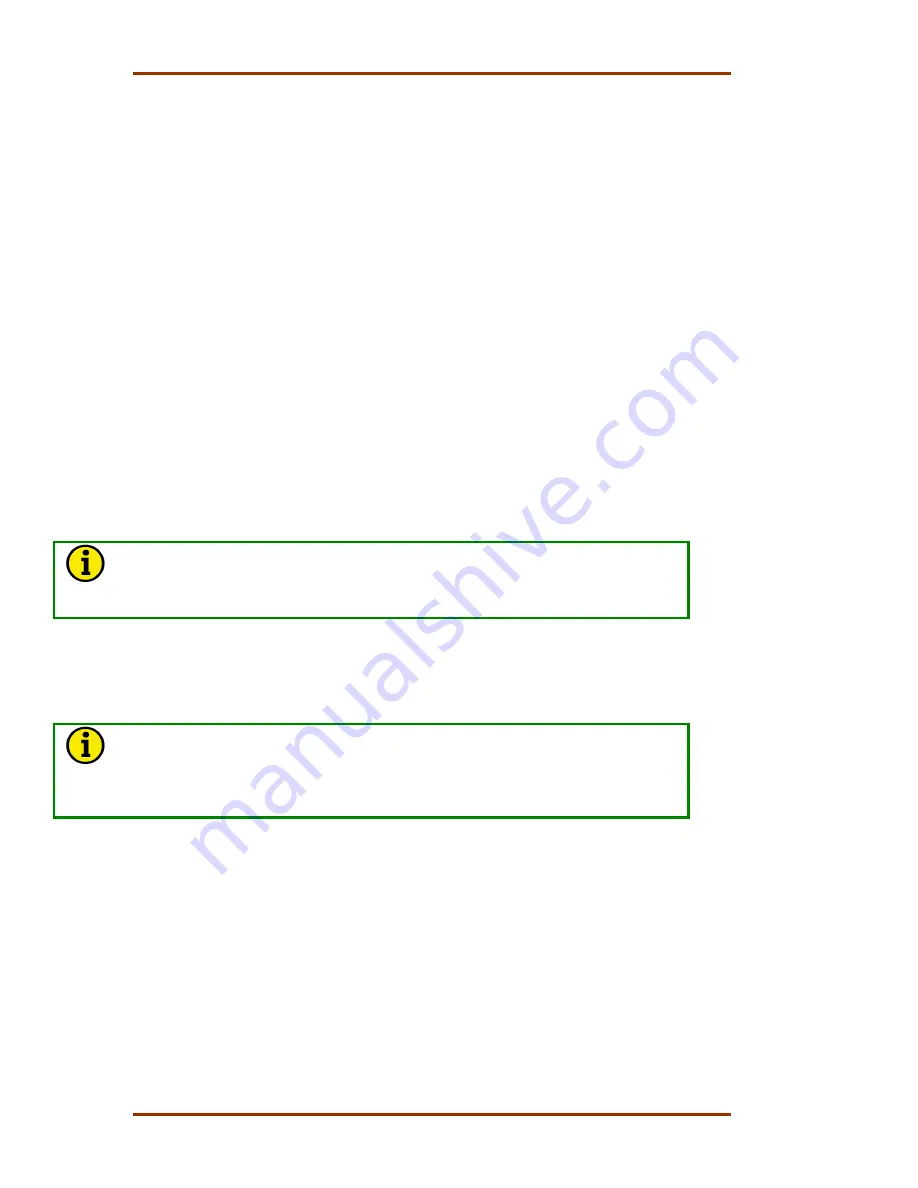
5009 Installation/Hardware
Manual 85580V2
38
Woodward
Each ATM connects to the control’s MPU & Analog I/O modules through
individual cables, and provides a common cage-clamp terminal connection for
customer field wiring. Figures 4-2 and 4-3 illustrate the different input wiring
configurations based on the type of speed sensing probes used.
Wiring Notes:
•
Refer to Figures 4-21 and 4-22 for Speed Sensor wiring connections on the
ATMs.
•
Each Speed input channel can only accept one MPU or one Proximity probe
at a time.
•
MPUs only—Jumpers must be added to each channel as shown in Figure
4-2 to allow the “C” analog module to sense speed.
•
Proximity Probes only—Individual 12 Vdc and 24 Vdc sources, with isolation
diodes on the power, common, and output source lines, are provided with
each speed input to power system proximity probes (100 mA fuses are used
on the 24 V output, the 12 V is current limited to 100 mA and located on the
ATMs).
•
Proximity Probes only—External pull-up resistors are required when
interfacing with an open collector type of proximity probe.
•
It is recommended that twisted shielded wiring be used between each probe
and ATM.
•
Shields should be connected to earth ground at all intermediate terminal
blocks, as well as terminated at the control terminal block. The exposed wire
length, beyond the shield, should be limited to 25 mm (1”).
•
ATM terminals accept wires from 0.08–2.5 mm² (27–12 AWG).
NOTE
If the speed signals are not within the following limits, the 5009 control will
respond with a speed sensor frequency error during the program checking
procedure.
(TxMxR)/60 must be < 25 000 Hz
T = Gear Teeth
M = (Overspeed Test Limit Setting x 1.02)
R = Gear Ratio
NOTE
If the MPU device is not providing a voltage greater than 1.5 Vrms, the MPU
device should be moved closer to the gear where speed is being monitored.
The following graph shows the minimum voltage necessary to detect speed
at the various frequencies.
Summary of Contents for MicroNet TMR 5009
Page 8: ...5009 Installation Hardware Manual 85580V2 vi Woodward...
Page 23: ...Manual 85580V2 5009 Installation Hardware Woodward 15 Figure 3 1 Hardware Identification...
Page 33: ...Manual 85580V2 5009 Installation Hardware Woodward 25 Figure 3 7 DIN Rail ATM Outline Drawing...
Page 35: ...Manual 85580V2 5009 Installation Hardware Woodward 27 Figure 3 9 DTM Outline Drawing...
Page 36: ...5009 Installation Hardware Manual 85580V2 28 Woodward Figure 3 10 DTM Mounting Configuration...
Page 68: ...5009 Installation Hardware Manual 85580V2 60 Woodward Figure 4 19 System Cable Layout Diagram...
Page 69: ...Manual 85580V2 5009 Installation Hardware Woodward 61 Figure 4 20 Power Supply Wiring Diagram...
Page 70: ...5009 Installation Hardware Manual 85580V2 62 Woodward Figure 4 21 ATM 1 Wiring Diagram...
Page 71: ...Manual 85580V2 5009 Installation Hardware Woodward 63 Figure 4 22 ATM 2 Wiring Diagram...
Page 72: ...5009 Installation Hardware Manual 85580V2 64 Woodward Figure 4 23 DTM 1 Wiring Diagram...
Page 73: ...Manual 85580V2 5009 Installation Hardware Woodward 65 Figure 4 24 DTM 2 Wiring Diagram...
Page 74: ...5009 Installation Hardware Manual 85580V2 66 Woodward Figure 4 25 DTM 3 Wiring Diagram...
Page 75: ...Manual 85580V2 5009 Installation Hardware Woodward 67 Figure 4 26 DTM 4 Wiring Diagram...
Page 89: ...Manual 85580V2 5009 Installation Hardware Woodward 81 Table 5 3 Discrete In Cable Connections...
Page 90: ...5009 Installation Hardware Manual 85580V2 82 Woodward Table 5 4 Relay Cable Connections...
Page 91: ...Manual 85580V2 5009 Installation Hardware Woodward 83 Table 5 4 Relay Cable Connections cont...
Page 92: ...5009 Installation Hardware Manual 85580V2 84 Woodward Table 5 5 Analog Combo Module...
Page 103: ...Manual 85580V2 5009 Installation Hardware Woodward 95 Figure 8 2 Operator Control Panel...
Page 108: ...5009 Installation Hardware Manual 85580V2 100 Woodward Figure 8 6 Real Power Sensor...
Page 115: ......
Page 116: ...Declarations...
Page 117: ......