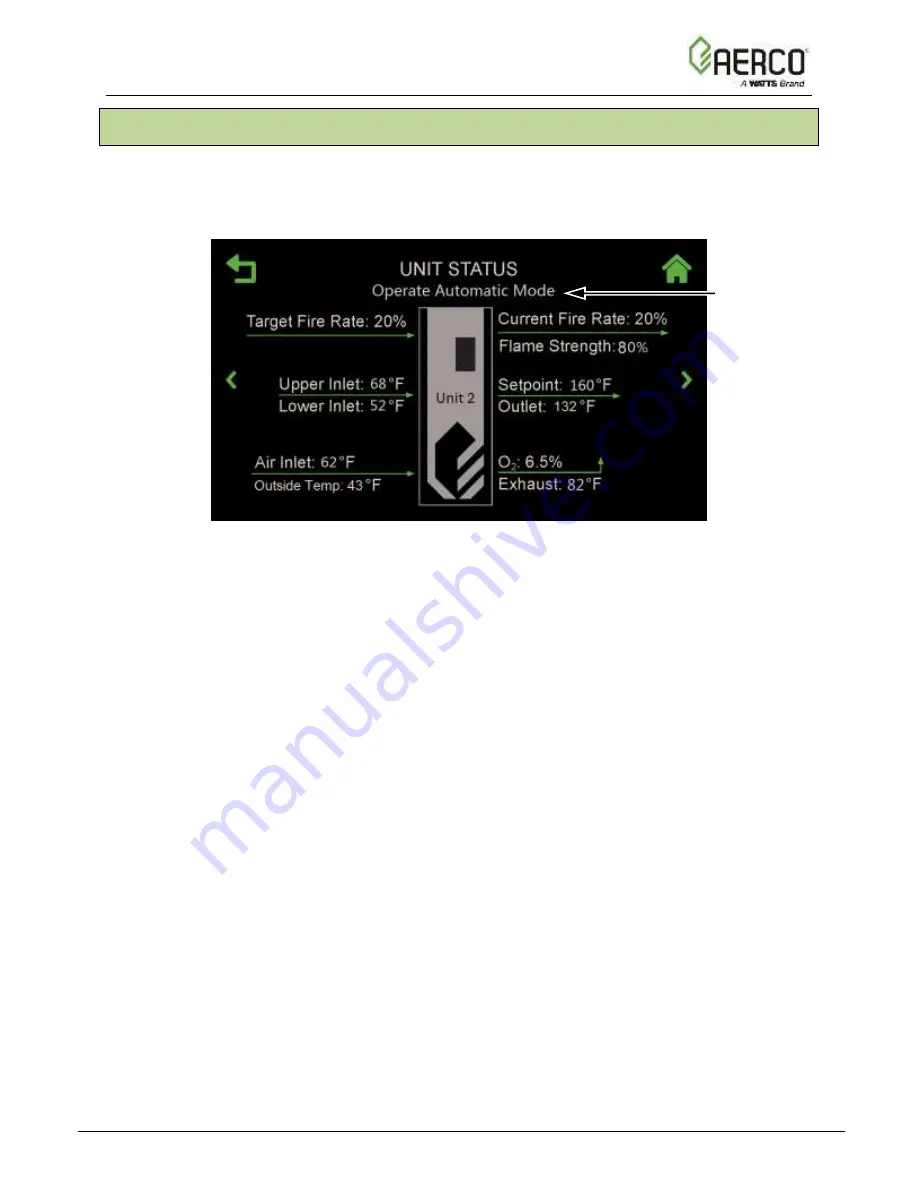
Edge [ii] Controller Operation Manual
SECTION 7
– UNIT STATUS
OMM-139_E
• 8/25/2020 Technical Support • (800) 526-0288 • Mon-Fri, 8 am - 5 pm EST Page
173
of
196
7.2 Unit Status
The
Unit Status
screen is the default Operating screen. It also appears when the unit powers
on (post the splash screen), comes out of sleep mode or has a successful flame. The system
automatically transitions to the Ignition screen during the Ignition sequence.
Figure 7.2: Example Unit Status Screen
In normal operation, the area just below the screen heading displays operating status. However,
if
there’s an operating error, it displays the error condition in red, as shown above.
The following notes apply to this screen:
•
For boilers with a single inlet port, the Unit Status screen will not display the upper Inlet
data and associated tag.
•
The
Flame Strength
is displayed in %, up to 100%.
•
The
Setpoint
is not displayed if the unit is part of a
“Client” in a BST cascade.
•
The
Max. Fire Rate
parameter is displayed when the max fire rate is set to a value
other than 100% and the unit Target Fire Rate is -1% or more from the Max Fire Rate.
STATUS
MESSAGE