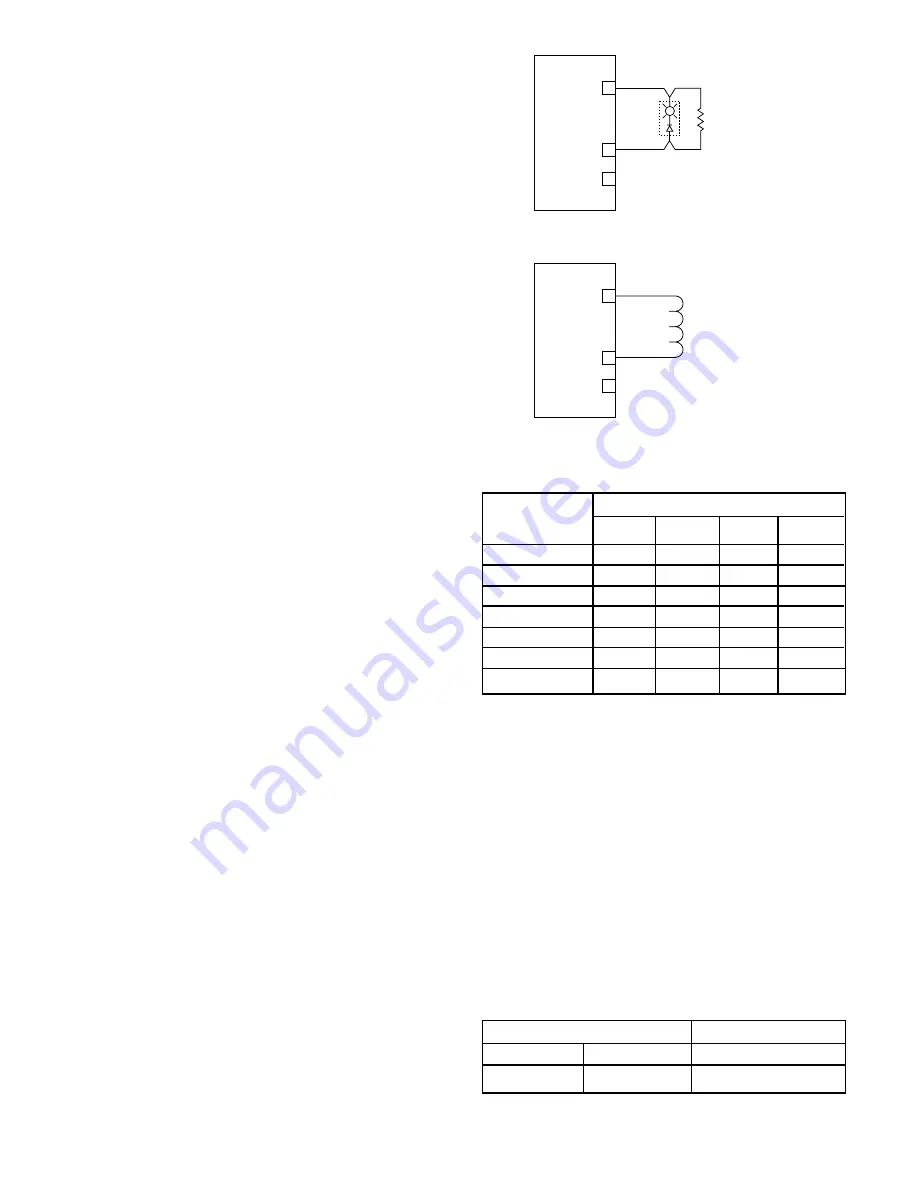
3-43
7.1
95-8533
Supervised Output
Notification Supervised for Open & Short Circuits
Connect external system wiring to the appropriate terminals
on the terminal block. See Figure 3-58.
The output of the IPM supervises the notification circuit by
reversing the polarity of the monitoring circuit. Polarity must
be observed when connecting the notification device. It is
essential to utilize a notification device approved for fire
alarm notification. These devices are polarized and would
not require the use of an external diode for the supervision of
the circuit. Wire one or more notification devices to the
output, with a 10 K ohm, 1/4 watt EOL resistor in parallel
across the last device.
No connection should be made to “+ Supply” terminal.
Each output channel is individually activated for response
pattern:
– supervisory
– continuous output
– 60 beats per minute
– 120 beats per minute
– temporal
– trouble.
Channels 7 and 8, Terminals 19 to 24
Supervised Output Agent Release
Connect external system wiring to the appropriate terminals
on the terminal block. See Figure 3-59.
Wire one or more releasing devices to the module output.
No connection should be made to “+ Supply” terminal.
The output of the IPM supervises the releasing circuit via the
coil of the releasing solenoid. It is essential to utilize a
releasing device approved for use with this output module.
This type of output does not require the use of EOL resistors
or diodes to supervise the circuit.
The output can be configured for continuous or timed response.
To ensure adequate operating voltage for the output device,
the maximum wiring length from the power source to the output
device must not exceed the values shown in Table 3-15 for
automatic release applications or Table 3-16 for deluge and
pre-action applications.
For solenoids, this wire length includes both the wiring from the
power supply to the IPM and the wiring from the module to the
solenoid.
NOTe
For FM system approval listing, pre-action and deluge
applications require that only FM approved deluge
valves can be wired into the IPM module. Remember
that the valves must utilize 24 vdc and must not exceed
2 amperes current draw.
NOTe
Squibs are not compatable with this output. If squib
actuation is required, use eQ2500ARM.
CONFIGURATION
Setting Module Network Address
One unique network address must be assigned to
each intelligent protection module. The address is set
by the 8 switch DIP assembly on the module. The
address is binary coded and is the sum of all switches
placed in the “closed” position.
Each discrete point of an intelligent protection module
has a tag number and a descriptor for identification.
Det-Tronics S
3
Safety System Software is used for
device configuration. The following shows the
minimum software/firmware releases:
Table 3-15—Maximum Wire Length for Releasing Applications
Device
Maximum Wire Length in Feet
12 AWG 14 AWG 16 AWG 18 AWG
890181*
150
100
60
899175*
150
100
60
895630*
150
100
60
897494*
190
120
75
486500*
1500
1000
600
400
31-199932-004*
150
100
60
2 Amp Load
190
120
75
*Fenwal Solenoid
+ SUPPLY A
IN– / OUT+ B
COMMON C
16
17
18
EOL
RESISTOR
10 K
Ω
B2094
Figure 3-58—CH-6: Supervised Output Configuration (Notification)
+ SUPPLY A
IN– / OUT+ B
COMMON C
19
20
21
NOTE: SHUNT/FLYBACK DIODES DO NOT NEED
TO BE INSTALLED ON THE FIELD DEVICE.
CIRCUIT PROTECTION IS PROVIDED
WITHIN THE IPM.
Figure 3-59—CH-7&8: Supervised Output Configuration (Agent Release)
Controller Firmware
S3
Revision
Version
Version
B
3.06
2.9.0.1
Summary of Contents for DET-TRONICS 95-8533
Page 128: ...7 1 95 8533 A 4 Figure A 1 System Drawing 007545 001 ...
Page 129: ...95 8533 A 5 7 1 Figure A 2 System Drawing 007545 001 ...
Page 131: ...95 8533 7 1 B 2 Figure B 1 Drawing 007546 001 ...
Page 132: ...95 8533 7 1 B 3 Figure B 2 Drawing 007546 001 ...
Page 134: ...95 8533 7 1 C 2 Figure C 1 Drawing 007547 001 ...
Page 141: ...95 8533 7 1 D 7 Figure D1 System Drawing 007545 001 ...
Page 143: ...APPENDIX E E 1 95 8533 7 1 ...