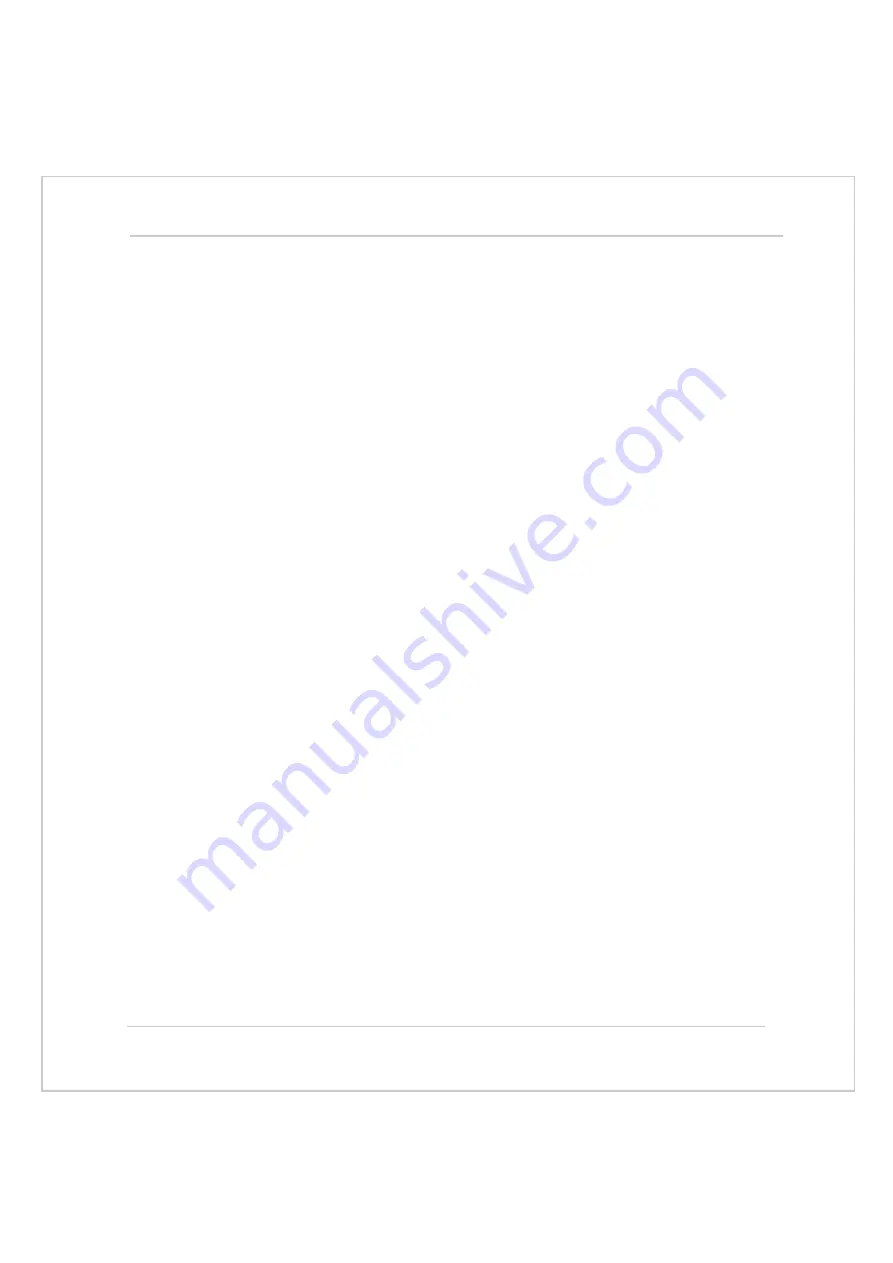
Motion Coordinator
Technical Reference Manual
Trio BASIC Commands 8-35
Motion and Axis Commands
The values specified are scaled using the UNIT CONVERSION FACTOR, axis parameter
UNITS
. Therefore if, for example, an axis has 4000 encoder edges/mm the
UNITS
for that axis is 4000. The command
MOVEABS(6)
would move to a position 6 mm
from the zero position.
The first parameter in the list is sent to the axis specified with the AXIS command or
to the current
BASE
axis, the second to the next axis, etc. By changing the
BASE
axis
uninterpolated, unsynchronised multi-axis motion can be achieved. Absolute moves
can be merged together for profiled continuous path movement. Axis parameter
MERGE
should be set to ON. In multi-axis systems the speed, acceleration and decel-
eration employed for the movement are taken from the BASE AXIS for the group.
Note2:
The position of the axis zero positions can be moved by the commands:
OFF-
POS,DEFPOS,REP_DIST,REP_OPTION
, and
DATUM
.
Example 1:
An X-Y plotter has a pen carousel whose position is fixed relative to the plotter
absolute zero position. To change pen an absolute move to the carousel position will
find the target irrespective of the plot position when commanded.
MOVEABS(20,350)
Example 2:
A pallet consists of a 6 by 8 grid in which gas canisters are inserted 85mm apart by a
packaging machine. The canisters are picked up from a fixed point. The first posi-
tion in the pallet is defined as position 0,0 using the
DEFPOS()
command. The part
of the program to position the canisters in the pallet is:
FOR x=0 TO 5
FOR y=0 TO 7
'MOVE TO PICK UP POINT:
MOVEABS(-340,-516.5)
'PICK UP SUBROUTINE:
GOSUB pick
PRINT “MOVE TO POSITION: “;x*6+y+1
MOVEABS(x*85,y*85)
'PLACE DOWN SUBROUTINE:
GOSUB place
NEXT y
NEXT x
Summary of Contents for Motion Coordinator Euro 205
Page 4: ......
Page 11: ...C H A P T E R CHAPTER0INTRODUCTION...
Page 12: ......
Page 27: ...C H A P T E R CHAPTER0HARDWARE OVERVIEW...
Page 28: ......
Page 35: ...Motion Coordinator Technical Reference Manual Hardware Overview 2 9 Motion Coordinator MC202...
Page 75: ...C H A P T E R CHAPTER0INSTALLATION...
Page 76: ......
Page 88: ...3 14 Installation EMC Considerations Trio Motion Technology...
Page 89: ...C H A P T E R CHAPTER0DAUGHTER BOARDS...
Page 90: ......
Page 126: ...4 38 Daughter Boards Profibus Daughter Board Trio Motion Technology...
Page 127: ...C H A P T E R CHAPTER0EXPANSION MODULES...
Page 128: ......
Page 158: ...5 32 Expansion Modules Communications Adaptors Trio Motion Technology...
Page 159: ...C H A P T E R CHAPTER0SYSTEM SETUP AND DIAGNOSTICS...
Page 160: ......
Page 173: ...C H A P T E R CHAPTER 0PROGRAMMING...
Page 174: ...7 2 Programming Trio Motion Technology...
Page 190: ...7 18 Programming Command Line Interface Trio Motion Technology...
Page 191: ...C H A P T E R CHAPTER0TRIO BASIC COMMANDS...
Page 192: ......
Page 200: ...8 10 Trio BASIC Commands Trio Motion Technology VERIFY 8 178 VFF_GAIN 8 178 VP_SPEED 8 179...
Page 254: ...8 64 Trio BASIC Commands Input Output Commands Trio Motion Technology...
Page 372: ...8 182Trio BASIC Commands Axis Parameters Trio Motion Technology...
Page 373: ...C H A P T E R CHAPTER 0PROGRAMMING EXAMPLES...
Page 374: ......
Page 389: ...C H A P T E R CHAPTER0SUPPORT SOFTWARE...
Page 390: ......
Page 472: ...10 84Support Software Project Autoloader Trio Motion Technology...
Page 473: ...C H A P T E R CHAPTER0FIBRE OPTIC NETWORK...
Page 474: ......
Page 486: ...11 14Fibre Optic Network Network Specification Trio Motion Technology...
Page 487: ...C H A P T E R CHAPTER0USING THE TRIO ACTIVEX CONTROL...
Page 488: ......
Page 518: ...12 32Using the Trio ActiveX Control Events Trio Motion Technology...
Page 519: ...C H A P T E R CHAPTER0COMMUNICATIONS PROTOCOLS...
Page 520: ......
Page 551: ...A P P E N D I X CHAPTER 0REFERENCE...
Page 552: ......