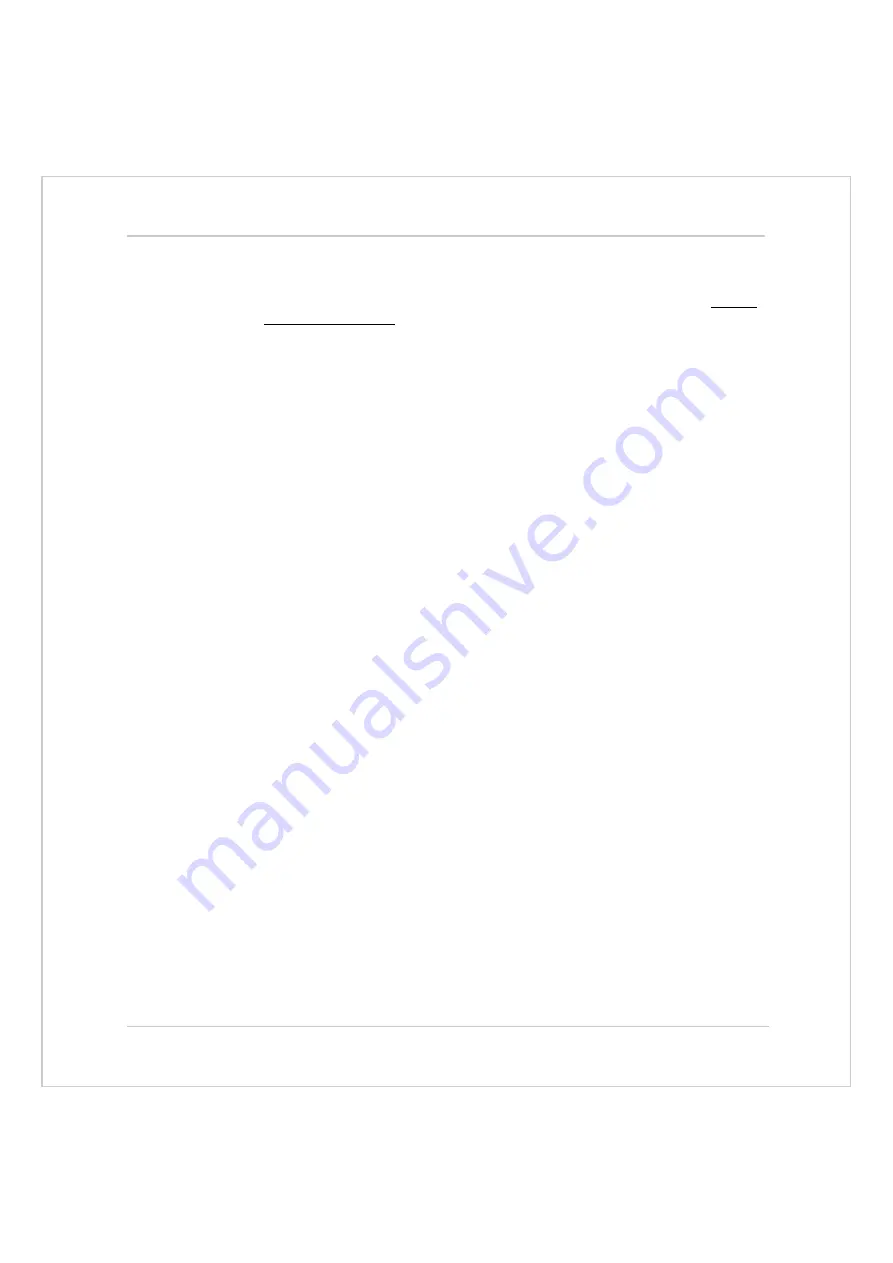
6-4
System Setup and Diagnostics
Preliminary Concepts:
Trio Motion Technology
Preliminary checks
All wiring should be checked for possible misconnection and integrity before
any power is applied.
• Disconnect all external connectors from the system, apart from the
CANBus and ribbon cable bus (only required if using an Axis Expander
module)
• Check bank selector switches on any Axis Expander modules, and the
module address DIP switches on the CAN I/O
• Apply power to system and check the 24v power input on master module.
• Connect a serial lead between serial port 0 (or connector A) on the
controllerand an unused serial port on your PC.
Checking Communications and System Configuration
• Ensure that the serial lead is connected between the Motion Coordinator
master (serial connector A) and a free serial port on the computer.
• Apply 24v to the Motion Coordinator.
• Run Motion Perfect on the computer. When Motion Perfect detects a
controller press the OK button. If this is the first time you have connected
you will need to select the “New Project” option when Motion Perfect tries
to ensure that your “Project” on the controller matches its copy on disk.
• When the “Project Consistent” message is received in the “Check Project”
window you know:
1
Motion Perfect has made a serial connection between your PC and the
controller.
2
Motion Perfect has an exact copy of the programs on the controller.
• The controller hardware configuration can now be checked using the
“Controller configuration” option under the “Controller” menu. Motion
Perfect draws a graphical representation of your system, as shown below.
Summary of Contents for Motion Coordinator Euro 205
Page 4: ......
Page 11: ...C H A P T E R CHAPTER0INTRODUCTION...
Page 12: ......
Page 27: ...C H A P T E R CHAPTER0HARDWARE OVERVIEW...
Page 28: ......
Page 35: ...Motion Coordinator Technical Reference Manual Hardware Overview 2 9 Motion Coordinator MC202...
Page 75: ...C H A P T E R CHAPTER0INSTALLATION...
Page 76: ......
Page 88: ...3 14 Installation EMC Considerations Trio Motion Technology...
Page 89: ...C H A P T E R CHAPTER0DAUGHTER BOARDS...
Page 90: ......
Page 126: ...4 38 Daughter Boards Profibus Daughter Board Trio Motion Technology...
Page 127: ...C H A P T E R CHAPTER0EXPANSION MODULES...
Page 128: ......
Page 158: ...5 32 Expansion Modules Communications Adaptors Trio Motion Technology...
Page 159: ...C H A P T E R CHAPTER0SYSTEM SETUP AND DIAGNOSTICS...
Page 160: ......
Page 173: ...C H A P T E R CHAPTER 0PROGRAMMING...
Page 174: ...7 2 Programming Trio Motion Technology...
Page 190: ...7 18 Programming Command Line Interface Trio Motion Technology...
Page 191: ...C H A P T E R CHAPTER0TRIO BASIC COMMANDS...
Page 192: ......
Page 200: ...8 10 Trio BASIC Commands Trio Motion Technology VERIFY 8 178 VFF_GAIN 8 178 VP_SPEED 8 179...
Page 254: ...8 64 Trio BASIC Commands Input Output Commands Trio Motion Technology...
Page 372: ...8 182Trio BASIC Commands Axis Parameters Trio Motion Technology...
Page 373: ...C H A P T E R CHAPTER 0PROGRAMMING EXAMPLES...
Page 374: ......
Page 389: ...C H A P T E R CHAPTER0SUPPORT SOFTWARE...
Page 390: ......
Page 472: ...10 84Support Software Project Autoloader Trio Motion Technology...
Page 473: ...C H A P T E R CHAPTER0FIBRE OPTIC NETWORK...
Page 474: ......
Page 486: ...11 14Fibre Optic Network Network Specification Trio Motion Technology...
Page 487: ...C H A P T E R CHAPTER0USING THE TRIO ACTIVEX CONTROL...
Page 488: ......
Page 518: ...12 32Using the Trio ActiveX Control Events Trio Motion Technology...
Page 519: ...C H A P T E R CHAPTER0COMMUNICATIONS PROTOCOLS...
Page 520: ......
Page 551: ...A P P E N D I X CHAPTER 0REFERENCE...
Page 552: ......