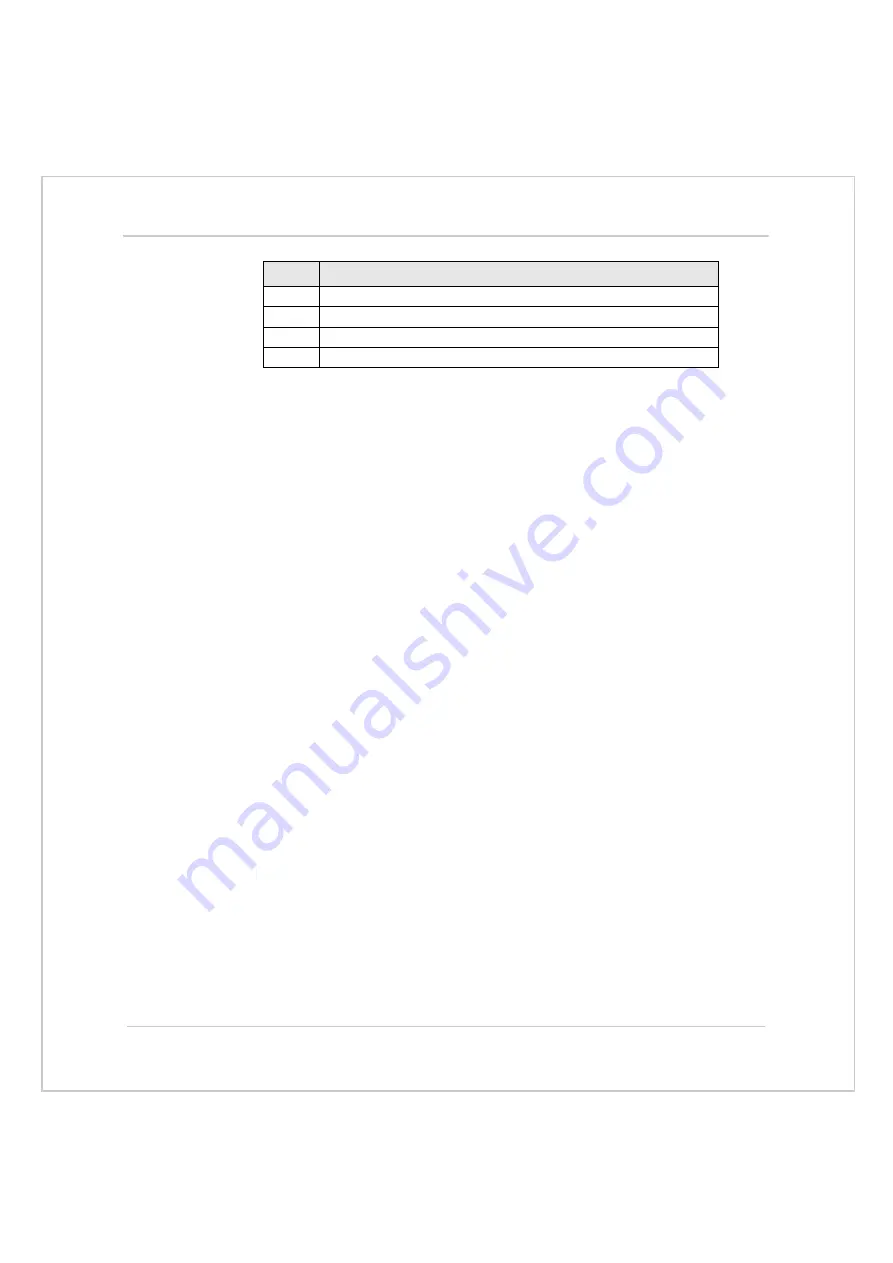
Motion Coordinator
Technical Reference Manual
Daughter Boards 4-17
Reference Encoder Daughter Board
The encoder may be powered from the +5V supply output on the daughter board,
provided it requires less than 150mA supply current. If the encoder is situated so
far from the module that the supply is inadequate an external supply should be
used and regulated locally to the encoder. In this case the +5V connection from
pin 8 should not be used and the external supply 0v should be connected to pin 5
(0V).
If the encoder does not have complementary outputs, pins 2, 4 and 7 should be
connected to a +2.5v bias voltage. This may be simply derived from a pair of 220
Ohm resistors in series with one end of the pair connected to 0v and the other
end to +5v. The centre point of the pair will form approximately 2.5v.
If the encoder does not have a marker pulse, pins 6 and 7 may be left uncon-
nected.
Registration Input
The registration input is a 24v dc input connected through high-speed opto-isola-
tion into the encoder counter circuit. An alternative 5v input pin is available on
the encoder port. The internal circuitry can be used to capture the position at
which the registration input makes a transition from low to high or vice-versa.
This function is accessed in software from the
REGIST
command. The input is
measured relative to the 0v input on the servo daughter board which must be
connected if the registration input is used. Note that this is the same 0v as the
encoder port.
7
marker (Z) complement
8
+5V (150 mA max) - This output is short circuit protected
9
Registration Input 5v Input pin
shell
protective ground
Pin.
function
Summary of Contents for Motion Coordinator Euro 205
Page 4: ......
Page 11: ...C H A P T E R CHAPTER0INTRODUCTION...
Page 12: ......
Page 27: ...C H A P T E R CHAPTER0HARDWARE OVERVIEW...
Page 28: ......
Page 35: ...Motion Coordinator Technical Reference Manual Hardware Overview 2 9 Motion Coordinator MC202...
Page 75: ...C H A P T E R CHAPTER0INSTALLATION...
Page 76: ......
Page 88: ...3 14 Installation EMC Considerations Trio Motion Technology...
Page 89: ...C H A P T E R CHAPTER0DAUGHTER BOARDS...
Page 90: ......
Page 126: ...4 38 Daughter Boards Profibus Daughter Board Trio Motion Technology...
Page 127: ...C H A P T E R CHAPTER0EXPANSION MODULES...
Page 128: ......
Page 158: ...5 32 Expansion Modules Communications Adaptors Trio Motion Technology...
Page 159: ...C H A P T E R CHAPTER0SYSTEM SETUP AND DIAGNOSTICS...
Page 160: ......
Page 173: ...C H A P T E R CHAPTER 0PROGRAMMING...
Page 174: ...7 2 Programming Trio Motion Technology...
Page 190: ...7 18 Programming Command Line Interface Trio Motion Technology...
Page 191: ...C H A P T E R CHAPTER0TRIO BASIC COMMANDS...
Page 192: ......
Page 200: ...8 10 Trio BASIC Commands Trio Motion Technology VERIFY 8 178 VFF_GAIN 8 178 VP_SPEED 8 179...
Page 254: ...8 64 Trio BASIC Commands Input Output Commands Trio Motion Technology...
Page 372: ...8 182Trio BASIC Commands Axis Parameters Trio Motion Technology...
Page 373: ...C H A P T E R CHAPTER 0PROGRAMMING EXAMPLES...
Page 374: ......
Page 389: ...C H A P T E R CHAPTER0SUPPORT SOFTWARE...
Page 390: ......
Page 472: ...10 84Support Software Project Autoloader Trio Motion Technology...
Page 473: ...C H A P T E R CHAPTER0FIBRE OPTIC NETWORK...
Page 474: ......
Page 486: ...11 14Fibre Optic Network Network Specification Trio Motion Technology...
Page 487: ...C H A P T E R CHAPTER0USING THE TRIO ACTIVEX CONTROL...
Page 488: ......
Page 518: ...12 32Using the Trio ActiveX Control Events Trio Motion Technology...
Page 519: ...C H A P T E R CHAPTER0COMMUNICATIONS PROTOCOLS...
Page 520: ......
Page 551: ...A P P E N D I X CHAPTER 0REFERENCE...
Page 552: ......