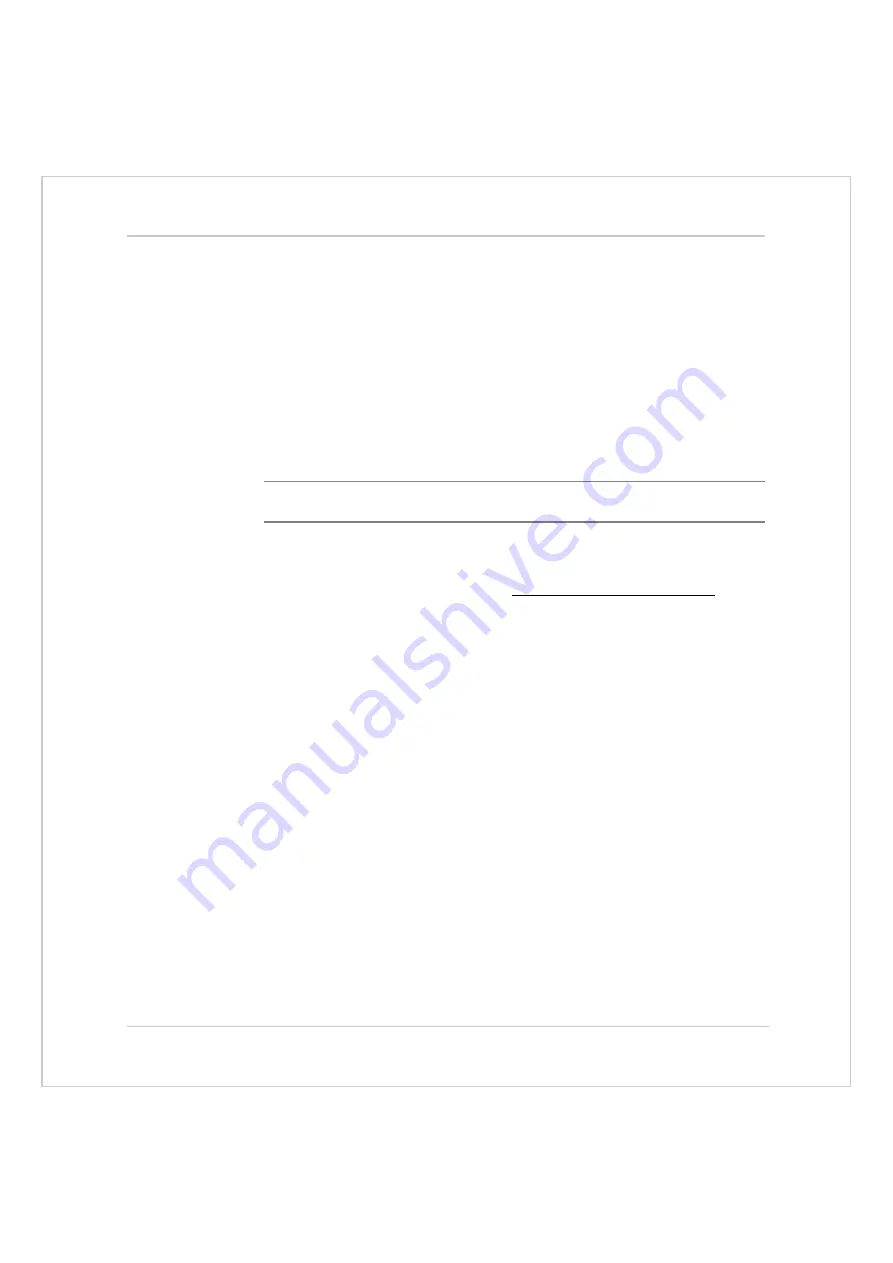
6-6
System Setup and Diagnostics
Preliminary Concepts:
Trio Motion Technology
Input/Output Connections:
• Check each of the 24v input connections with a meter then connect them to
the controller.
• Test each of the input channels being used for correct operation in turn.
These may be easily viewed in the I/O window. Use “IO Status” under the
“Tools” menu.
• Switch each output being used in turn for correct operation. These may be
easily set with the IO status window.
Connecting a Servo Motor to a Servo Daughter Board
Note:
This description assumes the motor / drive combination has been already
tested and is functioning optimally.
Each servo axis should be connected in turn.
• With the servo drive off or inhibited connect the motor encoder only (or the
encoder emulation output from the servo drive).
• Check the encoder counts both up and down by looking at the measured
axis position
MPOS
in the Axis parameter window of Motion Perfect (“Axis
parameters” under the “Tools” menu) whilst turning the axis by hand.
• Ensure the
SERVO
axis parameter is set OFF (0) in the Axis parameter and
that the
DAC
axis parameter is set to 0. It may be necessary to use the scroll
buttons to view these parameters. This will force 0 volts out of the +/-10v
output for the axis. Now connect the servo drive to the V+/V- connections.
• Enable the servo drive by clicking the “Drives disabled” button on the
control panel. If the axis runs away the motor/drive combination must be
re-checked. (Note: clicking “Drives disabled/ Drives enabled” is equivalent
to issuing a
WDOG=ON
or
WDOG=OFF
command).
The servo motor should now be powered and is likely to be creeping in one
direction as the position servo has been switched OFF.
• Set a small positive output voltage by setting
DAC=25
. The motor should
then move slowly forward - Check the encoder is counting up by looking at
the
MPOS
axis parameter. If this is correct check that the motor reverses
and the encoder counts down when
DAC=-25
.
• If the encoder counts down when a positive
DAC
voltage is applied. The
motor or position feedback needs to be reversed.
This can be achieved by:
•
Swap A and /A connections on the encoder input, or
Summary of Contents for Motion Coordinator Euro 205
Page 4: ......
Page 11: ...C H A P T E R CHAPTER0INTRODUCTION...
Page 12: ......
Page 27: ...C H A P T E R CHAPTER0HARDWARE OVERVIEW...
Page 28: ......
Page 35: ...Motion Coordinator Technical Reference Manual Hardware Overview 2 9 Motion Coordinator MC202...
Page 75: ...C H A P T E R CHAPTER0INSTALLATION...
Page 76: ......
Page 88: ...3 14 Installation EMC Considerations Trio Motion Technology...
Page 89: ...C H A P T E R CHAPTER0DAUGHTER BOARDS...
Page 90: ......
Page 126: ...4 38 Daughter Boards Profibus Daughter Board Trio Motion Technology...
Page 127: ...C H A P T E R CHAPTER0EXPANSION MODULES...
Page 128: ......
Page 158: ...5 32 Expansion Modules Communications Adaptors Trio Motion Technology...
Page 159: ...C H A P T E R CHAPTER0SYSTEM SETUP AND DIAGNOSTICS...
Page 160: ......
Page 173: ...C H A P T E R CHAPTER 0PROGRAMMING...
Page 174: ...7 2 Programming Trio Motion Technology...
Page 190: ...7 18 Programming Command Line Interface Trio Motion Technology...
Page 191: ...C H A P T E R CHAPTER0TRIO BASIC COMMANDS...
Page 192: ......
Page 200: ...8 10 Trio BASIC Commands Trio Motion Technology VERIFY 8 178 VFF_GAIN 8 178 VP_SPEED 8 179...
Page 254: ...8 64 Trio BASIC Commands Input Output Commands Trio Motion Technology...
Page 372: ...8 182Trio BASIC Commands Axis Parameters Trio Motion Technology...
Page 373: ...C H A P T E R CHAPTER 0PROGRAMMING EXAMPLES...
Page 374: ......
Page 389: ...C H A P T E R CHAPTER0SUPPORT SOFTWARE...
Page 390: ......
Page 472: ...10 84Support Software Project Autoloader Trio Motion Technology...
Page 473: ...C H A P T E R CHAPTER0FIBRE OPTIC NETWORK...
Page 474: ......
Page 486: ...11 14Fibre Optic Network Network Specification Trio Motion Technology...
Page 487: ...C H A P T E R CHAPTER0USING THE TRIO ACTIVEX CONTROL...
Page 488: ......
Page 518: ...12 32Using the Trio ActiveX Control Events Trio Motion Technology...
Page 519: ...C H A P T E R CHAPTER0COMMUNICATIONS PROTOCOLS...
Page 520: ......
Page 551: ...A P P E N D I X CHAPTER 0REFERENCE...
Page 552: ......