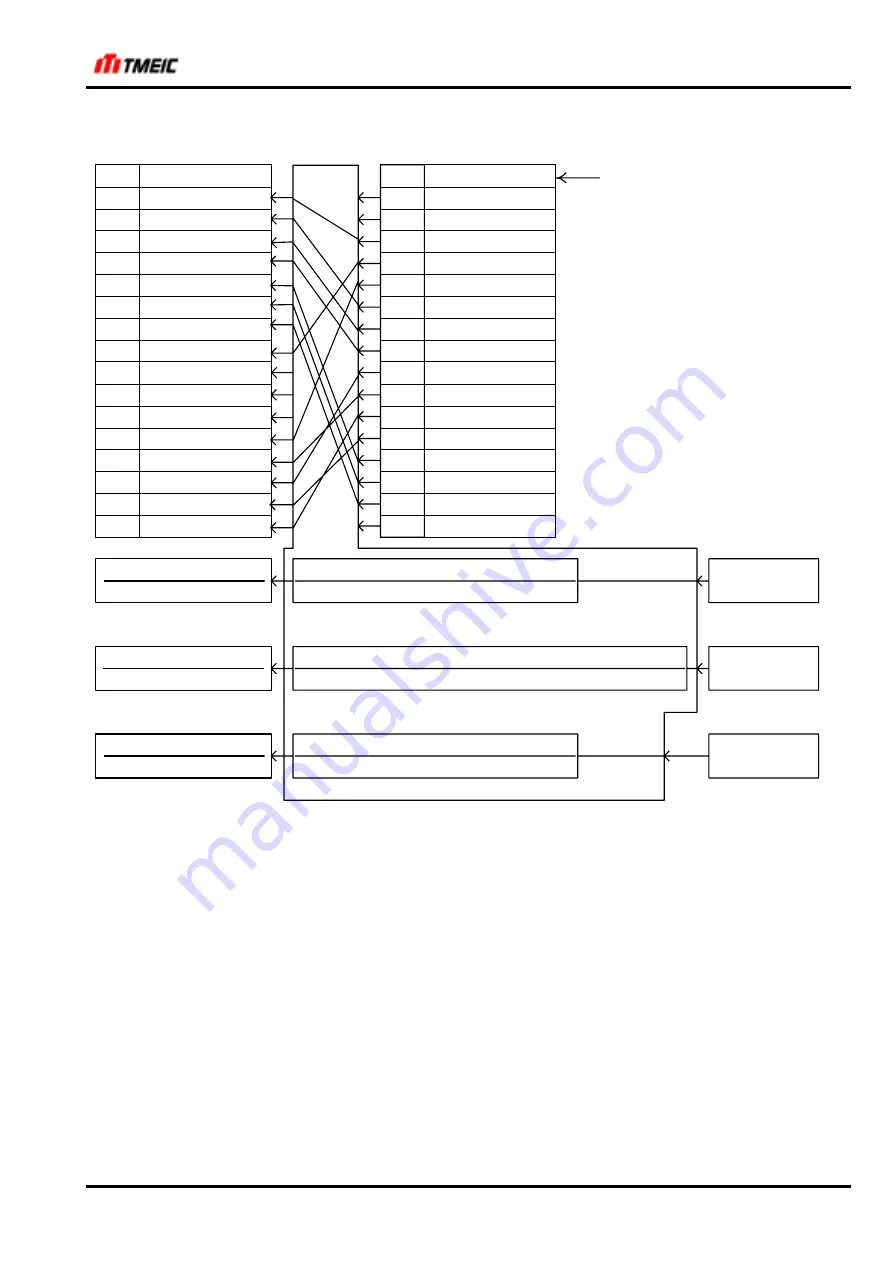
— 64 —
6F3A4768
DeviceNet Master
PLC etc.
DeviceNet slave
Drive equipment
Address defined by
$SCAN_WR02_AS
BIT
F
E
D
C
B
A
9
8
7
6
5
4
3
2
1
0
BIT
F
E
D
C
B
A
9
8
7
6
5
4
3
2
1
0
SSEQ_OUT1
BLR
UVA
UV
READY
C_L
RNTD
FLDR
FD
RD
FAULT
ALARM
C_FN
CUT
SP_LMT
HB
Sequence output
UVA
C_L
RNTD
FLDR
C_FN
CUT
SP_LMT
UV
At Reference
Ref From Net
Ctrl From Net
Ready
Running 2 (Rev)
Running 1 (Fwd)
Warning
Faulted
Speed Feedback [min
-1
]
2
$DNET_SP_SCALE
2
$DNET_SP_SCALE
x $CS_MOTOR_RPM [min
-1
]
25000
SP_F_OUT
[25000/100%]
Address defined by
$SCAN_WR01_AS
Torque Feedback [Nm]
2
$DNET_TR_SCALE
2$DNET_TR_SCALE x 974 x $MA_MOTOR_KW [kW] x 98
4 x $CS_MOTOR_RPM [min-1] x $CS_SP_BASE [1000/100%]
Address defined by
$SCAN_WR05_AS
T_R_OUT
[4000/100%]
Process Feedback [%]
2
$DNET_PRC_SCALE2
2
$DNET_PRC_SCALE
$DNET_PRC_GAIN2
I1_F_DSP
[4000/100%]
Address defined by
$SCAN_WR04_AS
ex.)
ARND-8127
*1
*2
ex.) SSEQ_OUT1, 2, 4
*1) Indefinite value (Do not use At
Reference)
*2) BIT 6: Net Ref of Command input
(See Fig.3.4.7)
Fig. 3.4.10
DeviceNet 4W/4W Mode (Send)
StockCheck.com