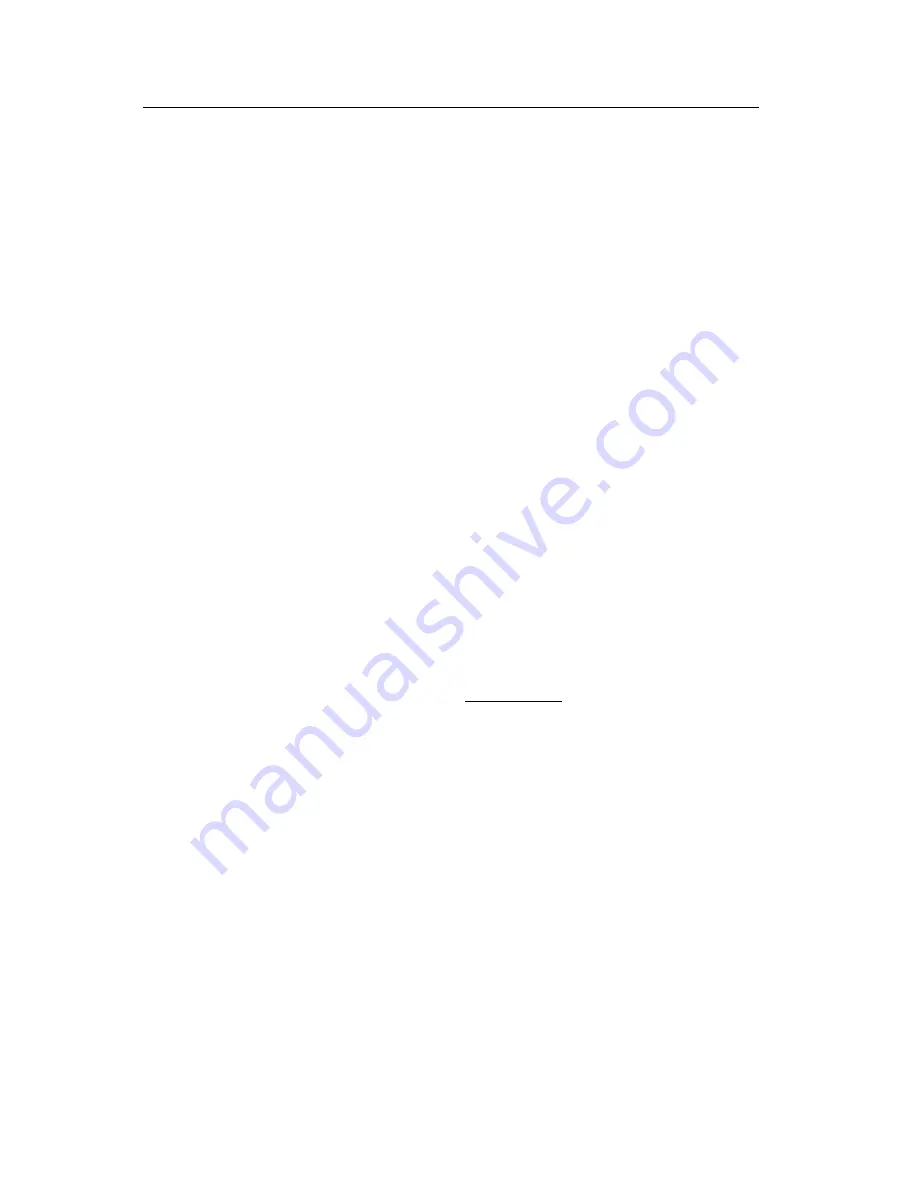
User Manual
EM100 Mini Inverter
1
Preface
Thank you for purchasing EM100 series mini inverter.
Document No.: 31010008
Version No.:103
Issue Date: 06/03/2013
EM100 mini inverter is a compact, intuitive, reliable and performing AC variable speed
drive for 3-phase induction motors.
This manual offers the general information of installation, wiring, function parameters,
daily maintenance, and fault diagnosis of EM100 mini inverter.
It is the duty of any user to perform the appropriate, correct installation or configuration
of the optional parameters of the devices. Neither SINEE nor its distributors shall be
responsible or liable for misuse of the information contained herein or mismatching the
inverter with the motor.
In the interests of commitment to a policy of continuous development and improvement,
SINEE reserves the right to update the specification of the product or its performance, or
the content herein without notice.
More updates and information are available at www.sinee.cn.