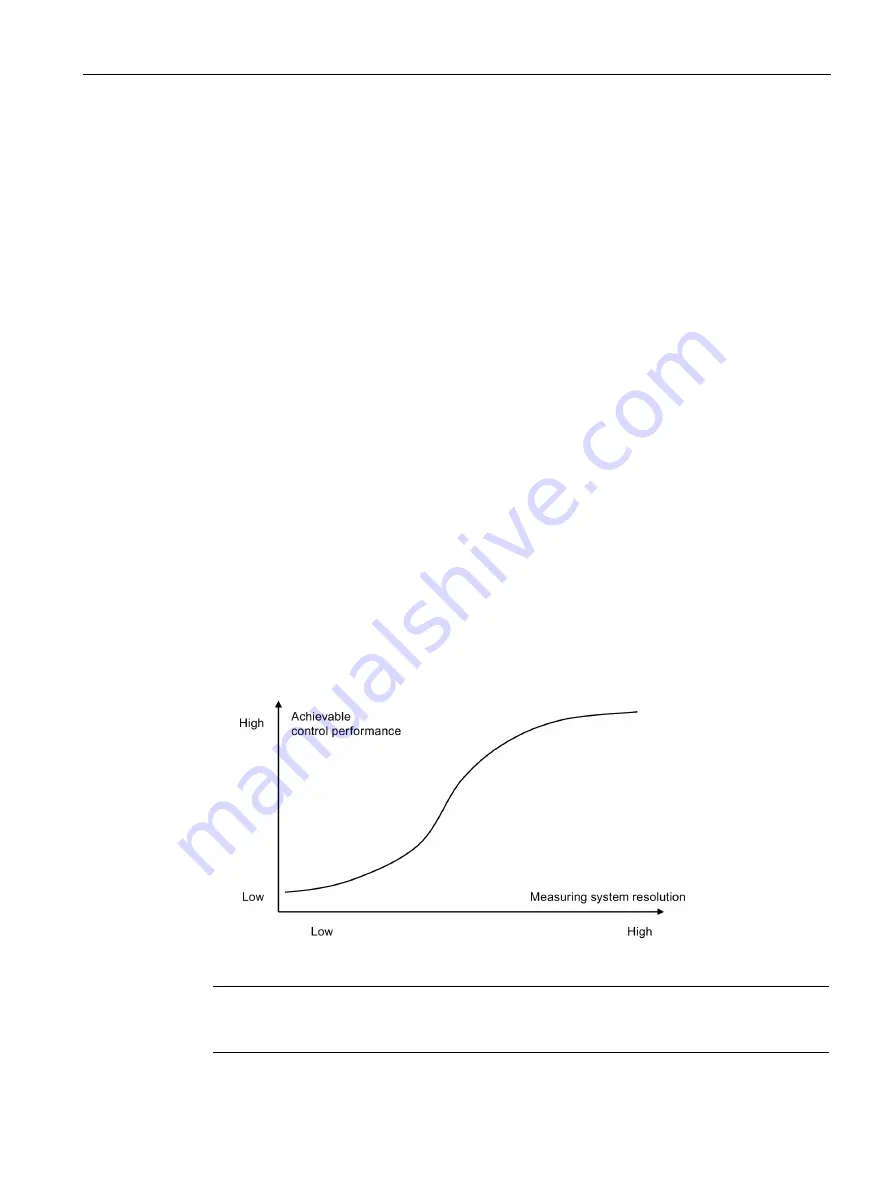
Motor components and options
4.1 Motor components
1FW68 radial segment motors
Configuration Manual, 08/2021, A5E51132930B AA
77
Observe the documentation of the drive system being used and the documentation of the
encoder manufacturer.
Encoder systems available in the market use different scanning principles (magnetic,
inductive, optical, …).
In conjunction with this, high-resolution optical or magnetic systems must have a pulse
clearance (or a grid spacing) of maximum 0.04 mm at the circumference on the
measuring standard.
Systems that do not have a high resolution (e.g. inductive, magnetic) must be designed
to be significantly more rugged and insensitive to pollution. With pulse clearances in the
range of approx. 1 mm on the measuring standard, these systems achieve angular
measuring accuracies that are still sufficient to address positioning accuracy
specifications for a wide range of applications.
In some instances, encoder systems also internally interpolate the measurement signal.
However, when being used on the drive system, this should be avoided as a result of the
highly accurate internal interpolation of the measurement signal in the SINAMICS sensor
modules.
Depending on the mechanical design of the machine regarding elasticity and natural
oscillation, depending on the speed and grid spacing of the measuring standard,
oscillation can be excited and noise generated.
Using a high-resolution optical measuring system, generally, when compared to other
techniques, the best dynamic performance, highest control quality, high noise immunity,
precision and low noise can be achieved. Further, excitation of oscillation can be also
avoided.
Preconditions to achieve this include:
•
The overall mechanical system, including motor and encoder mounting, permits this
•
Extremely stiff dynamic machine design to avoid the excitation of low-frequency
mechanical oscillation
Figure 4-5 Performance-resolution diagram
Note
Siemens does not accept any warranty for the properties/features of third-party
products.
Summary of Contents for SIMOTICS T-1FW68
Page 1: ......
Page 2: ......
Page 14: ...Table of contents 1FW68 radial segment motors 12 Configuration Manual 08 2021 A5E51132930B AA ...
Page 193: ......
Page 194: ......