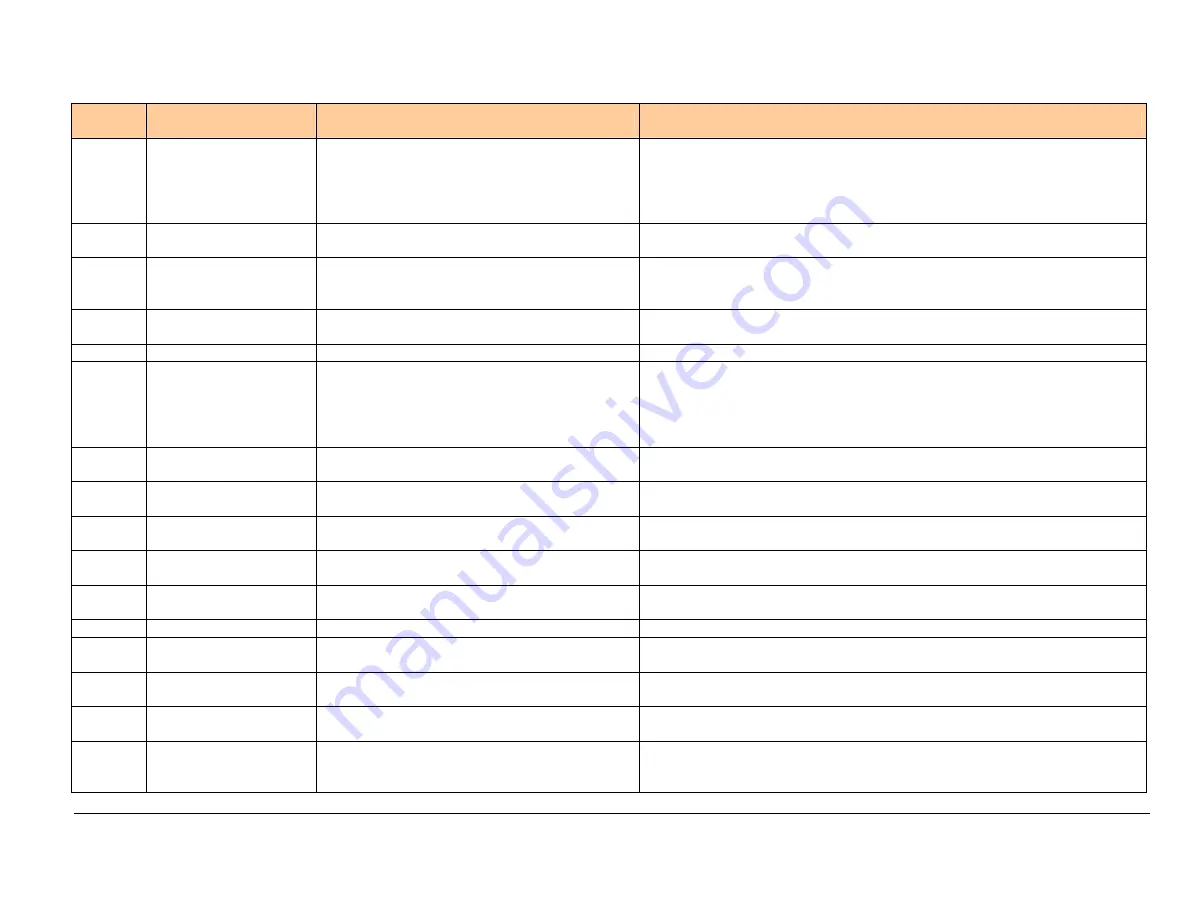
236/248
Building Technologies Division
Basic documentation LMV36...
CC1P7544en
Infrastructure & Citiies Sector
30 Error code list
25.09.2013
Error
code
Diagnostic code
Meaning for the LMV36... system
Remedy
check distance
2. As the motor turns, other metal parts are detected also, in addition to the tappets
improve
mounting.
3. Electromagnetic interference on the sensor lines
check cable routing, improve EMC
7 Invalid
standardized
speed
The standardized speed measured does not lie in the permissible range.
Motor turns too slowly or too fast.
15
Speed deviation µC1 + µC2
The speeds of microcomputer 1 and 2 deviated too much. This can be caused by wrong
standardized speeds (e.g. after restoring a data set to a new unit)
→
repeat standardization and
check the fuel-air ratio
20
Wrong phase of phase manager
Standardization was made in a wrong phase. Permitted are only phases
12
controller OFF,
start standardization again
21
Safety loop / burner flange open
Safety loop or burner flange is open
repeat standardization with safety loop closed
22
Air actuator not referenced
Air actuator has not been referenced or has lost its referencing.
1. Check if the reference position can be approached.
2. Check if actuators have been mixed up.
3. If error only occurs after the start of standardization, the actuator might be overloaded and
cannot reach its destination.
23 VSD
deactivated
Standardization was started with VSD deactivated
activate the VSD and repeat standardization
24
No valid operation mode
Standardization was started without valid operation mode
activate valid operation mode and repeat standardization
25
Pneumatic air-fuel ratio control
Standardization was started with pneumatic air-fuel ratio control
standardization with pneumatic air-fuel ratio control not possible
128
Running command with no preceding standardization
VSD is controlled but not standardized
make standardization
255
No standardized speed available
Motor turns but is not standardized
make standardization
83
#
Speed error VSD
Required speed has not been reached
Bit 0
Valency 1
Lower control range limitation of control
Speed has not been reached because control range limitation has become active
for measures, refer to error code 80
Bit 1
Valency 2...3
Upper control range limitation of control
Speed has not been reached because control range limitation has become active
for measures, refer to error code 80
Bit 2
Valency 4...7
Interruption via disturbance pulses
Speed has not been reached due to too much electromagnetic interference on the sensor line
for measures, refer to error code 81
Bit 3
Valency
8
Curve too steep in terms of ramp speed
Check speed differential between the curvepoints and the modulating operating ramp setting
(parameter 544).
1. Modulating operating ramp 32 seconds