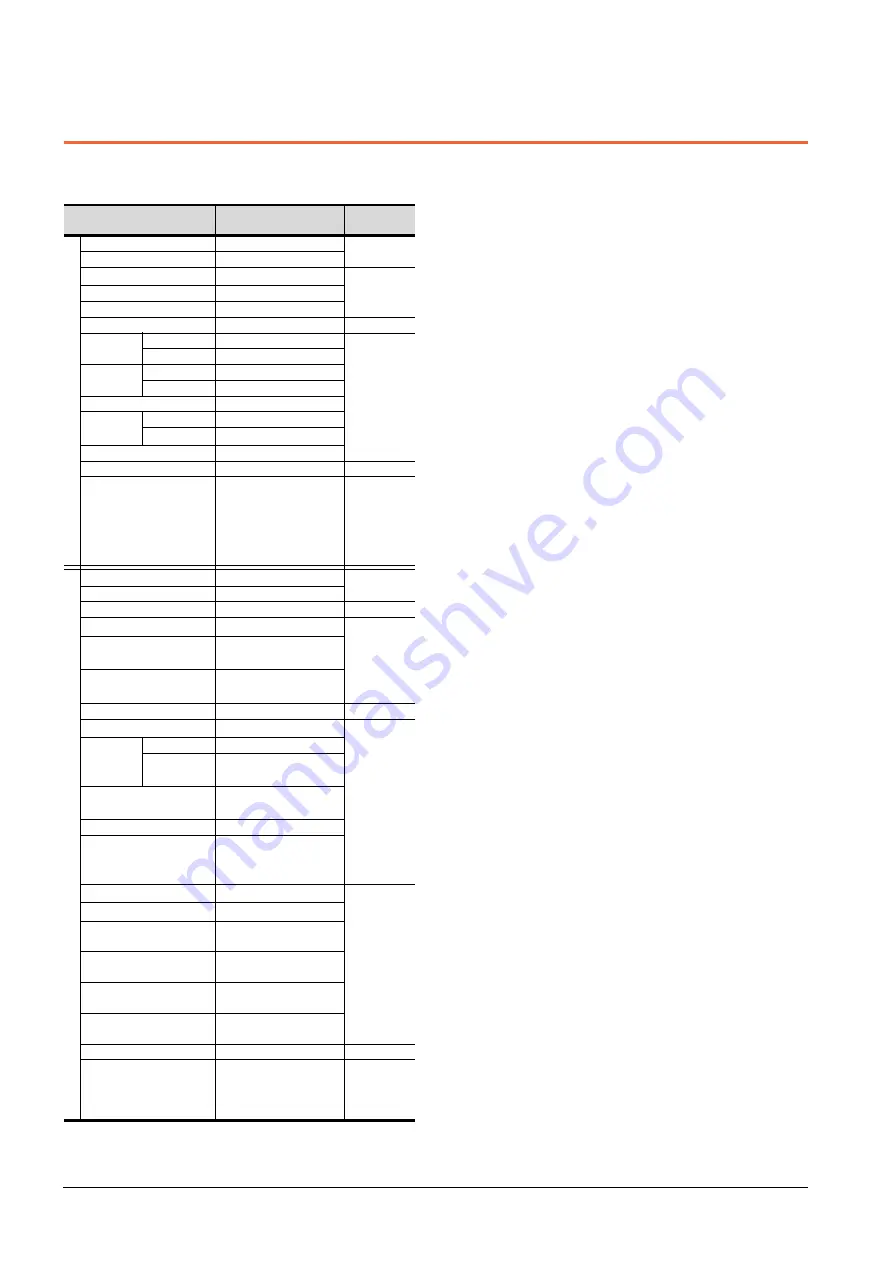
2 - 8
2. DEVICE RANGE THAT CAN BE SET
2.1 MELSEC-Q/QS, Q17nD/M/NC/DR, CRnD-700
2.1
MELSEC-Q/QS, Q17nD/M/NC/DR, CRnD-700
The table below shows the device ranges in [MELSEC-Q/
QS, Q17nD/M/NC/DR, CRnD-700] as the controller type.
*1
Do not set a file register by GT Designer3 when executing
multiple programs with the file of the file register set at [Use
the same file name as the program] by the PLC parameter of
GX Developer.
Otherwise, read/write at GOT will be erroneous.
*2
Available for file register of block No. switched with the RSET
instruction.
*3
Available for file register of block No. of file name switched
with the QDRSET instruction.
*4
Only the intelligent function module on the station connected
to GOT can be specified.
Set within the address range of the buffer memory existing in
the target intelligent function module.
*5
Do not use local devices set in the MELSEC-Q system.
Otherwise, normal monitoring is not performed.
*6
Even though Universal model QCPU processes 64-bit data,
the GOT cannot monitor 64-bit data.
*7
This cannot be monitored when in GOT multi-drop
connection.
*8
For monitoring the internal relay (M) or data register (D) of a
C Controller module, configure the settings related to the
device functions in the device setting tab of the language
controller setting utility.
*9
The device No. must be set in multiples of 16.
(When using the QCPU)
* For details of *1 to *6, refer to 2.2 MELSEC-QnA, MELDAS C6 *.
*7
This is not supported by GT10.
*8
This cannot be monitored when in GOT multi-drop
connection.
(When using the Q Motion)
*9
When setting special internal relay M9000 to M9255, use SM
for the device name and set the value subtracted 9000 for
the device number (0 to 255).
*10
The setting range is D9000 to D9255 when setting the
special data register.
*11
D8192 to D8999 and D9256 to D9999 are out of the valid
setting range.
(When using the QCPU/Q Motion)
*12
Do not use local devices set in the MELSEC-Q (Multi)/Q
Motion system.
Otherwise, normal monitoring is not performed.
Device name
*6
Setting range
Device No.
representation
Bit
d
e
v
ice
Input (X)
X0
to
X3FFF
Hexadecimal
Output (Y)
Y0
to
Y3FFF
Internal relay (M)
*5*8
M0
to
M61439
Decimal
Latch relay (L)
L0
to
L32767
Annunciator (F)
F0
to
F32767
Link relay (B)
B0
to
B9FFFF
Hexadecimal
Timer
*5
Contact (TT)
TT0
to
TT32767
Decimal
Coil (TC)
TC0
to
TC32767
Counter
*5
Contact (CT)
CT0
to
CT32767
Coil (CC)
CC0
to
CC32767
Special relay (SM)
SM0
to
SM2255
Retentive
timer
*5
Contact (SS)
SS0
to
SS32767
Coil (SC)
SC0
to
SC32767
Step relay (S)
S0
to
S32767
Link special relay (SB)
SB0
to
SB7FFF
Hexadecimal
Word device bit
Specified bit of the
following word devices
(Except Timer, Counter,
Retentive timer, Index
register and Buffer
memory)
―
W
o
rd
de
vi
ce
Data register (D)
*5*8
D0
to
D4910079
Decimal
Special data register (SD)
SD0
to
SD2255
Link register (W)
W0
to
W4AEBFF
Hexadecimal
Timer (current value) (TN)
*5
TN0
to
TN32767
Decimal
Counter (current value)
(CN)
*5
CN0
to
CN32767
Retentive timer
(current value) (SN)
*5
SN0
to
SN32767
Link special register (SW)
SW0
to
SW7FFF
Hexadecimal
File register (R)
*1*2
R0
to
R32767
Decimal
Extension
file register
(ER)
*1
Block
0
to
255
Device
ER0
to
ER32767
Extension file register
(ZR)
*1*3
ZR0
to
ZR4849663
Index register (Z)
Z0
to
Z19
Buffer memory
(Intelligent function module)
(G)
*4
G0
to
G65535
Ww
*7
Ww0
to
Ww1FFF
Hexadecimal
Wr
*7
Wr0
to
Wr1FFF
Multiple CPU high speed
transmission memory (U3E0)
U3E010000 to U3E024335
Multiple CPU high speed
transmission memory (U3E1)
U3E110000 to U3E124335
Multiple CPU high speed
transmission memory (U3E2)
U3E210000 to U3E224335
Multiple CPU high speed
transmission memory (U3E3)
U3E310000 to U3E324335
Motion device (#)
#0
to
#12287
Decimal
Bit device word
*9
Converting the above bit
devices into words
(Except Timer, Counter
and Retentive timer)
―
Summary of Contents for GOT2000 Series
Page 2: ......
Page 62: ...1 38 1 PREPARATORY PROCEDURES FOR MONITORING 1 6 Checking for Normal Monitoring ...
Page 64: ......
Page 80: ...2 16 2 DEVICE RANGE THAT CAN BE SET 2 6 MELSEC WS ...
Page 246: ...7 26 7 COMPUTER LINK CONNECTION 7 6 Precautions ...
Page 252: ...8 6 8 BUS CONNECTION 8 1 Connectable Model List ...
Page 256: ...8 10 8 BUS CONNECTION 8 2 System Configuration ...
Page 288: ...8 42 8 BUS CONNECTION 8 4 Precautions ...
Page 324: ...9 36 9 MELSECNET H CONNECTION PLC TO PLC NETWORK MELSECNET 10 CONNECTION PLC TO PLC NETWORK ...
Page 416: ......
Page 510: ...15 46 15 SERVO AMPLIFIER CONNECTION 15 7 Precautions ...
Page 518: ...16 8 16 ROBOT CONTROLLER CONNECTION 16 6 Precautions ...
Page 540: ...17 22 17 CNC CONNECTION 17 7 Precautions ...
Page 541: ...MULTIPLE GOT CONNECTIONS 18 GOT MULTI DROP CONNECTION 18 1 ...
Page 542: ......
Page 567: ...MULTI CHANNEL FUNCTION 19 MULTI CHANNEL FUNCTION 19 1 ...
Page 568: ......
Page 599: ...FA TRANSPARENT FUNCTION 20 FA TRANSPARENT FUNCTION 20 1 ...
Page 600: ......
Page 668: ...20 68 20 FA TRANSPARENT FUNCTION 20 7 Precautions ...
Page 670: ...REVISIONS 2 ...
Page 673: ......