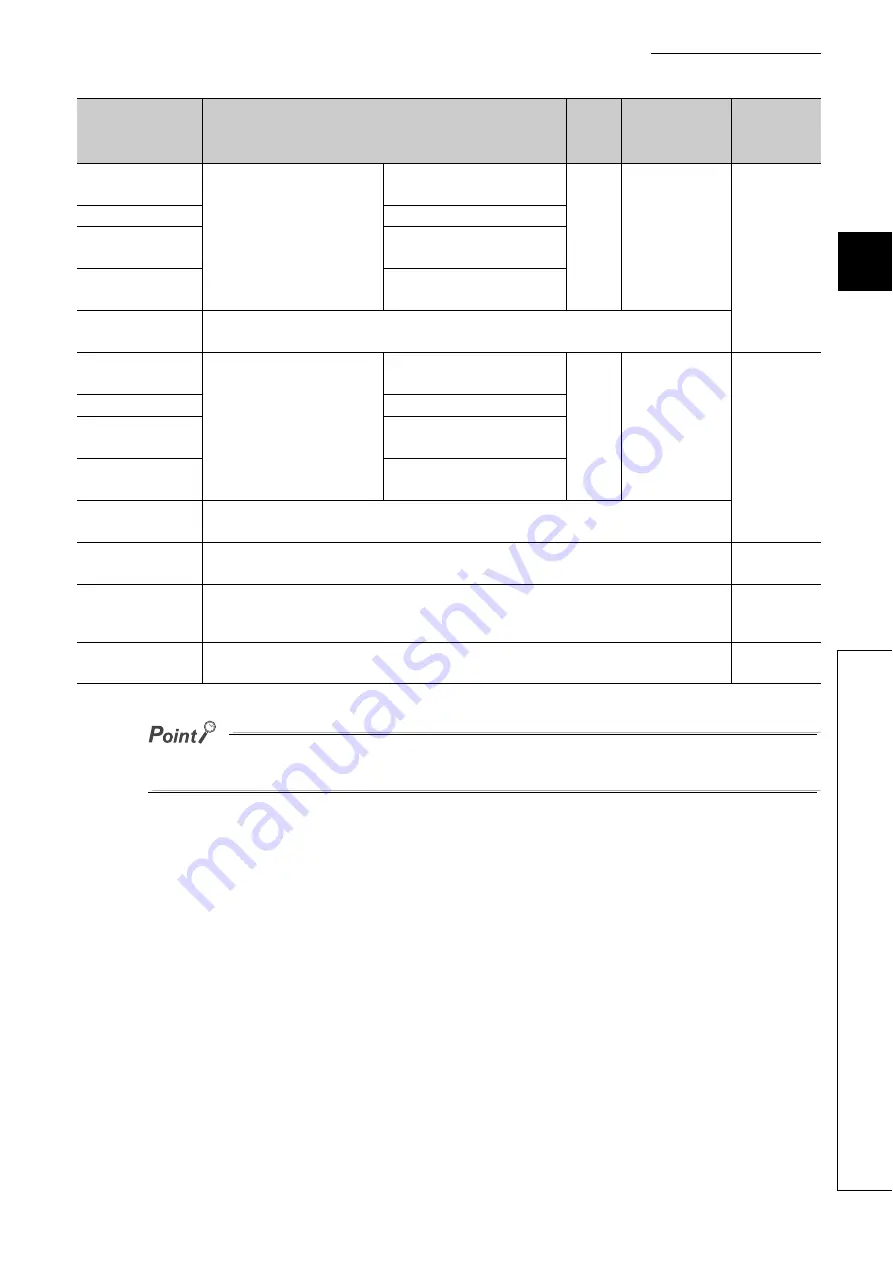
45
CHAPTER 3 SPECIFICATIONS
3
3.
5
Lis
t of
Buf
fer M
e
mory
A
ddress
e
s
*1 Since the version of a master/local module is stored, the initial value depends on the master/local module used.
Do not write data to "System area".
Doing so may cause malfunction of the programmable controller system.
30224
(7610
H
)
PORT2 line error occurrence
rate (max.)
Station No.1
0
Read
to
to
30343
(7687
H
)
Station No.120
30344
(7688
H
)
Station No.0
30345 to 30351
(7689
H
to 768F
H
)
System area
30352
(7690
H
)
PORT2 line error occurrence
rate (present)
Station No.1
0
Read
to
to
30471
(7707
H
)
Station No.120
30472
(7708
H
)
Station No.0
30473 to 30479
(7709
H
to 770F
H
)
System area
30480 to 31739
(7710
H
to 7BFB
H
)
System area
31740 to 32380
(7BFC
H
to 7E7C
H
)
C Controller module parameter area
32381 to 32767
(7E7D
H
to 7FFF
H
)
System area
Address
(Decimal
(Hexadecimal))
Name
Initial
value
Read, write
Refer to