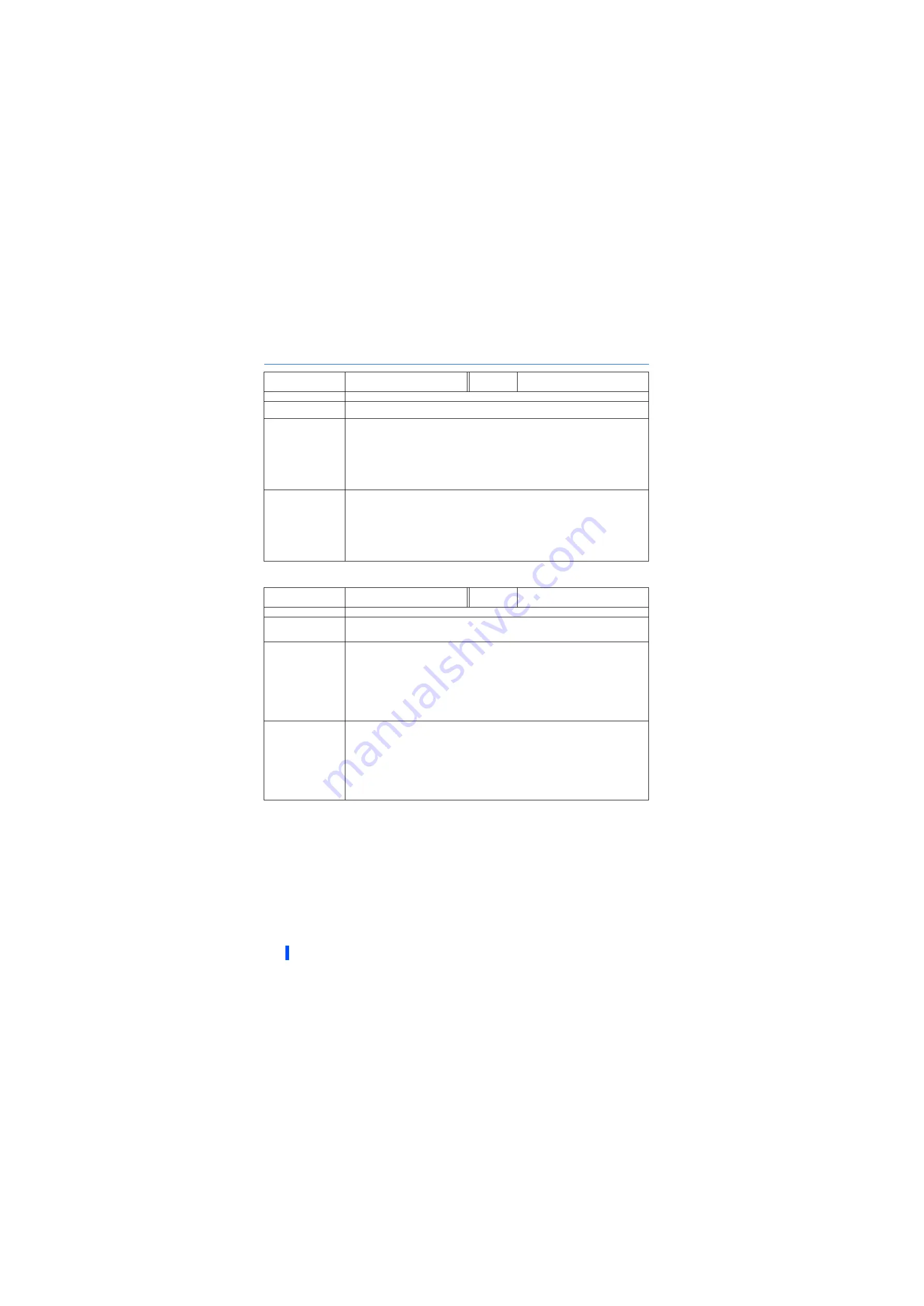
Causes and corrective actions
636
Abbreviation
E.OC2
FR-LU08
FR-PU07
OC During Cnst Spd
Name
Overcurrent trip during constant speed
Description
When the inverter output current reaches or exceeds approximately 235%
of the rated current during
constant-speed operation, the protection circuit is activated and the inverter trips.
Check point
• Check for sudden load change.
• Check for output short-circuit.
• Check if the stall prevention operation level is set too high. Check if the fast-response current limit operation
is disabled.
• Check that the power supply for RS-485 terminal is not shorted (under vector control).
• Check that the rotation direction is not switched from forward to reverse rotation (or from reverse to forward)
during torque control under Real sensorless vector control.
• Check that the inverter capacity matches with the motor capacity. (PM sensorless vector control)
• Check if a start command is given to the inverter while the motor is coasting. (PM sensorless vector control)
Corrective action
• Keep the load stable.
• Check the wiring to make sure that output short circuit does not occur.
• Lower the stall prevention operation level. Activate the fast-response current limit operation.
(Refer to
• Check RS-485 terminal connection (under vector control).
• Prevent the motor from switching the rotation direction from forward to reverse (or from reverse to forward)
during torque control under Real sensorless vector control.
• Choose inverter and motor capacities that match. (PM sensorless vector control)
• Input a start command after the motor stops. (PM sensorless vector control)
Differs according to ratings. The rating can be changed using
Pr.570 Multiple rating setting
. (Refer to
.)
148% for SLD rating, 170% for LD rating, 235% for ND rating (initial setting), and 280% for HD rating
Abbreviation
E.OC3
FR-LU08
FR-PU07
OC During Dec
Name
Overcurrent trip during deceleration or stop
Description
When the inverter output current reaches or exceeds approximately 235%
of the rated current during
deceleration (other than acceleration or constant speed), the protection circuit is activated and the inverter
trips.
Check point
• Check for sudden speed reduction.
• Check for output short-circuit.
• Check for too fast operation of the motor's mechanical brake.
• Check if the stall prevention operation level is set too high. Check if the fast-response current limit operation
is disabled.
• Check that the power supply for RS-485 terminal is not shorted (under vector control).
• Check that the rotation direction is not switched from forward to reverse rotation (or from reverse to forward)
during torque control under Real sensorless vector control.
• Check that the inverter capacity matches with the motor capacity. (PM sensorless vector control)
• Check if a start command is given to the inverter while the motor is coasting. (PM sensorless vector control)
Corrective action
• Set the deceleration time longer.
• Check the wiring to make sure that output short circuit does not occur.
• Check the mechanical brake operation.
• Lower the stall prevention operation level. Activate the fast-response current limit operation. (Refer to
• Check RS-485 terminal connection (under vector control).
• Prevent the motor from switching the rotation direction from forward to reverse (or from reverse to forward)
during torque control under Real sensorless vector control.
• Choose inverter and motor capacities that match. (PM sensorless vector control)
• Input a start command after the motor stops. (PM sensorless vector control)
Differs according to ratings. The rating can be changed using
Pr.570 Multiple rating setting
. (Refer to
.)
148% for SLD rating, 170% for LD rating, 235% for ND rating (initial setting), and 280% for HD rating
Summary of Contents for 800 Series
Page 11: ...MEMO 10 ...
Page 17: ...MEMO 16 ...
Page 95: ...MEMO 94 ...
Page 671: ...MEMO 670 ...
Page 681: ...MEMO 680 ...