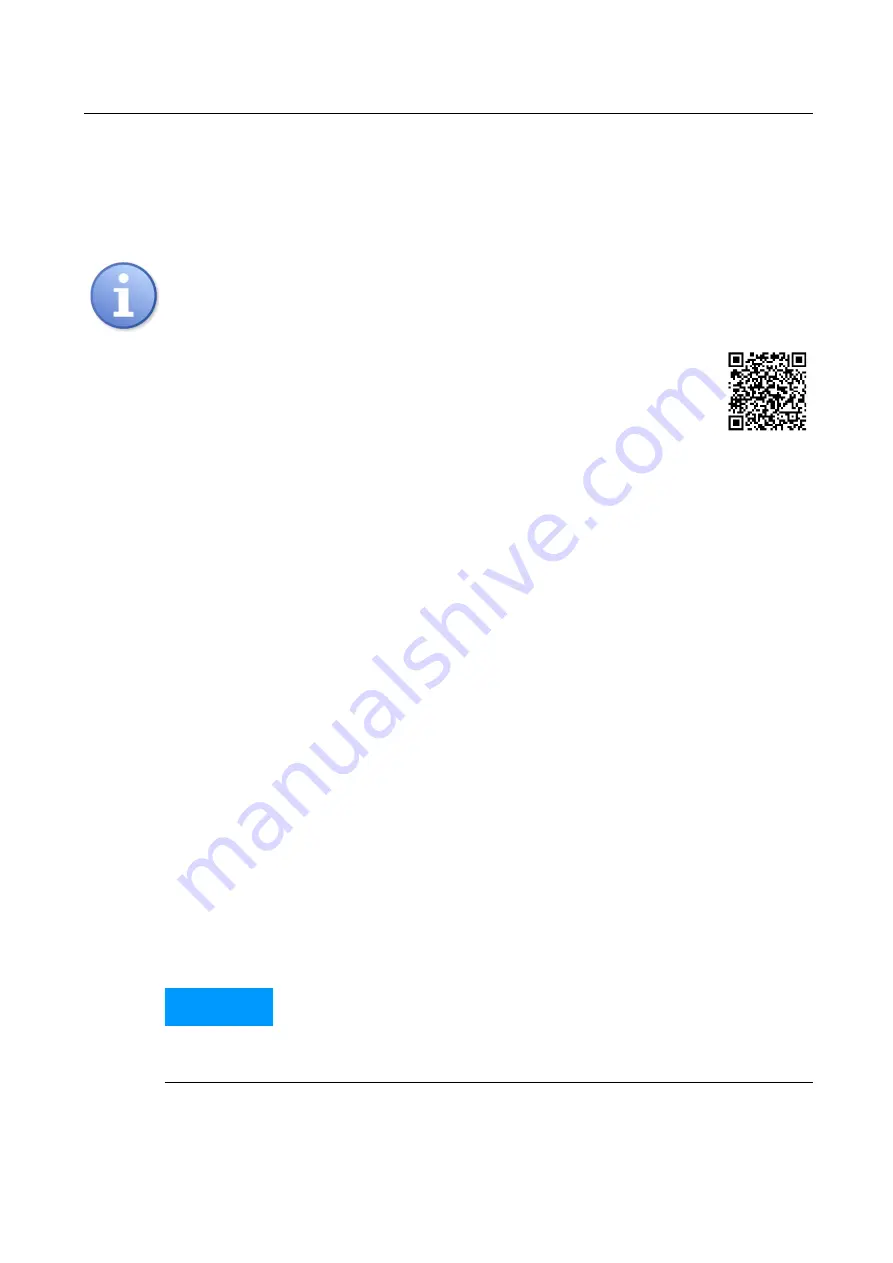
62
BA023001-en
•
Select TP_LINK_xxxx.
•
Enter password.
If no WiFi device is found, the connection must be set up manually using the SSID and
the PIN.
Alternatively, free QR code generators can be found on the Internet, which can be
used to generate a personal QR code for the CONNECT brake tester.
If this is photographed (e.g. on iOS devices) or scanned with a QR code
scanner app, the standard browser is automatically opened and the Inter-
net address entered.
6.3.5
Variant 3: Integration of the test bench into own network
Alternatively, the ZM of the test bench can also be integrated into a company network.
For this purpose, the Ethernet port X12 "EXT" can be configured analogue to a LAN
interface of a PC:
•
DHCP client:
The Ethernet port X12 "EXT" of the ZM can be configured as a DHCP client so that
it is assigned an IP address by the local DHCP server.
•
Static IP address:
The Ethernet port X12 "EXT" can be assigned a fixed IP address and a default
gateway.
This means that the brake tester can be reached within the network by connecting a
computer via network cable to a usual network socket of this network. If this network
also offers WiFi access, it is possible for the test bench to be operated directly via WiFi-
capable terminals:
•
Turn on computer/mobile device, log in after booting, open browser.
•
Establish the browser connection as described above.
6.4
Test procedure
6.4.1
Drive on test bench
NOTICE
Drive slowly (walking speed), centrally and straight on the test bench. The left and
right sensing rollers must be actuated simultaneously.
Summary of Contents for CONNECT Series
Page 19: ...19 BA023001 en 2 3 2 Set up diagram Set up diagram I ...
Page 20: ...20 BA023001 en Set up diagram II ...
Page 22: ...22 BA023001 en 2 4 1 Wiring diagram ...
Page 23: ...23 BA023001 en 2 4 2 Control cabinet structure Basic variant ...
Page 24: ...24 BA023001 en 2 4 3 Control cabinet structure Full equipment ...
Page 25: ...25 BA023001 en ...
Page 53: ...53 BA023001 en ...
Page 138: ...138 BA023001 en 13 Annex 13 1 Naming convention ...