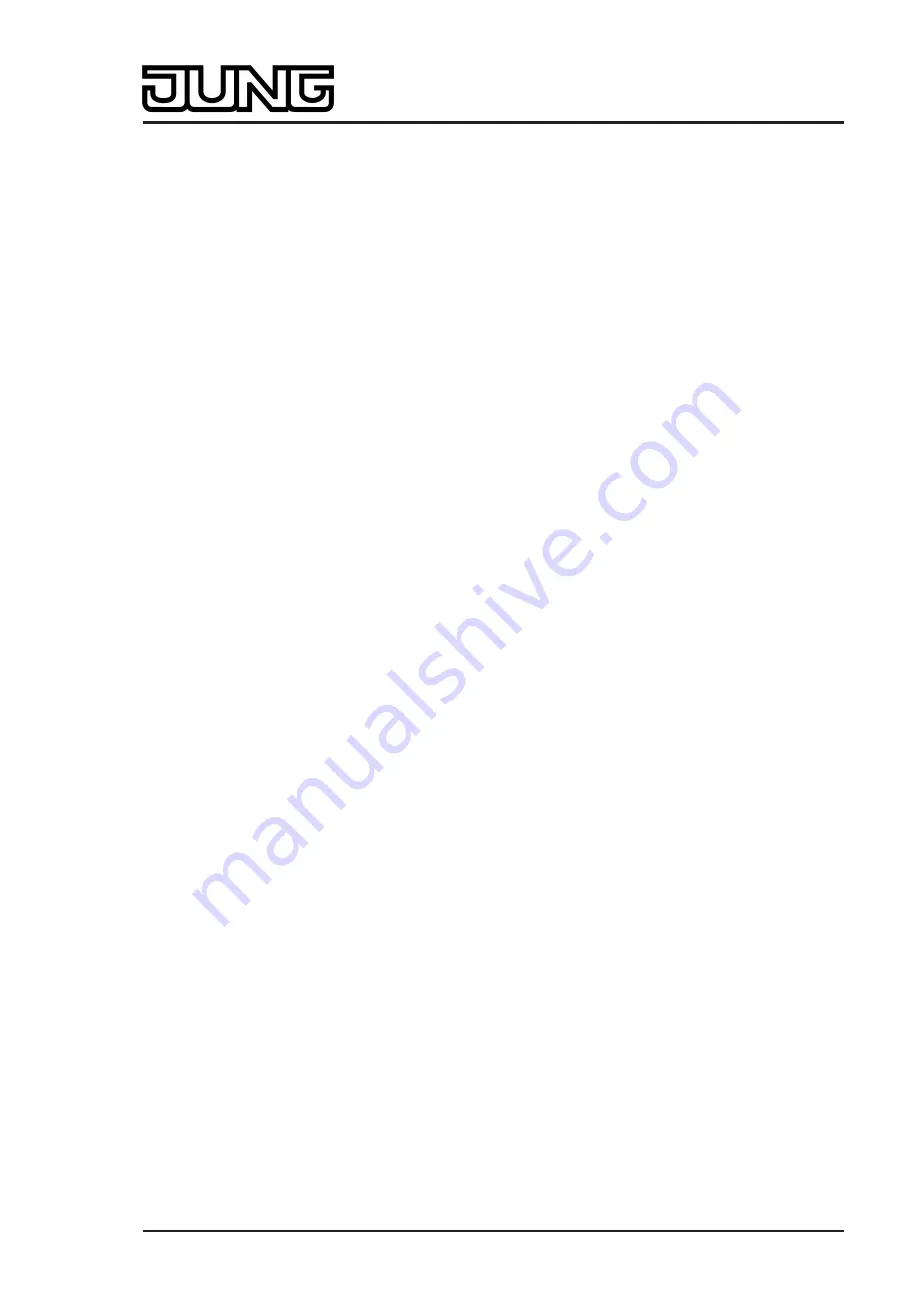
Art. No. SC 1000 KNX
Case 1: Cycle time > 2 x adjusting cycle time of the electrothermal drives used (ETD)
In this case, the switch-on or switch-off times of the PWM signal are long enough for the
actuators to have sufficient time to fully open or fully close within a given time period.
Advantages:
The desired mean value for the command value and thus for the required room temperature will
be set relatively precisely, even for several actuators triggered at the same time.
Disadvantages:
It should be noted, that, due to the full valve lift to be continuously 'swept', the life expectancy of
the actuators can diminish. For very long cycle times (> 15 minutes) with less sluggishness in
the system, the heat emission into the room, for example, in the vicinity of the radiators, can
possibly be non-uniform and be found disturbing.
i
This setting is recommended for sluggish heating systems (such as underfloor heating).
i
Even for a bigger number of triggered actuators, maybe of different types, this setting can
be recommended to be able to obtain a better mean value of the adjusting travels of the
valves.
Case 2: Cycle time < adjusting cycle time of the electrothermal drives used (ETD)
In this case, the switch-on or switch-off times of the PWM signal are too short for the actuators
to have enough time to fully open or fully close within a given period.
Advantages:
This setting ensures continuous water flow through the radiators, thus facilitating uniform heat
emission into the room.
If only one actuator is triggered the controller can continuously adapt the command value to
compensate the mean value shift caused by the short cycle time, thus setting the desired room
temperature.
Disadvantages:
If more than one drive is triggered at the same time the desired mean value will become the
command value, which will result in a very poor adjustment of the required room temperature, or
in adjustment of the latter with major deviations, respectively.
The continuous flow of water through the valve, and thus the continuous heating of the drives
causes changes to the dead times of the drives during the opening and closing phase. The
short cycle time and the dead times means that the required variable (mean value) is only set
with a possibly large deviation. For the room temperature to be regulated constantly after a set
time, the controller must continually adjust the command value to compensate for the mean
value shift caused by the short cycle time. Usually, the control algorithm implemented in the
controller (PI control) ensures that control deviations are compensated.
i
This setting is recommended for quick-reaction heating systems (such as surface
radiators).
2-point feedback control
The 2-point control represents a very simple temperature control. For this type of feedback
control, two hysteresis temperature values are set. The actuators are triggered by the controller
via switch-on and switch-off command value commands (1-bit type). A continuous command
value is not calculated for this type of control.
The room temperature is also evaluated by this type of control in cycles every 30 seconds. Thus
the command values change, if required, only at these times. The disadvantage of a
continuously varying temperature as a result of this feedback control option is in contrast with
the advantage of this very simple 2-point room temperature control. For this reason, quick-
reaction heating or cooling systems should not be triggered by a 2-point feedback control
system, for this can lead to very high overshooting of the temperature, thus resulting in loss of
comfort. When presetting the hysteresis limiting values, you should distinguish between the
operating modes.
Page 173 of 347
Software "Smart Control 501511"
Functional description