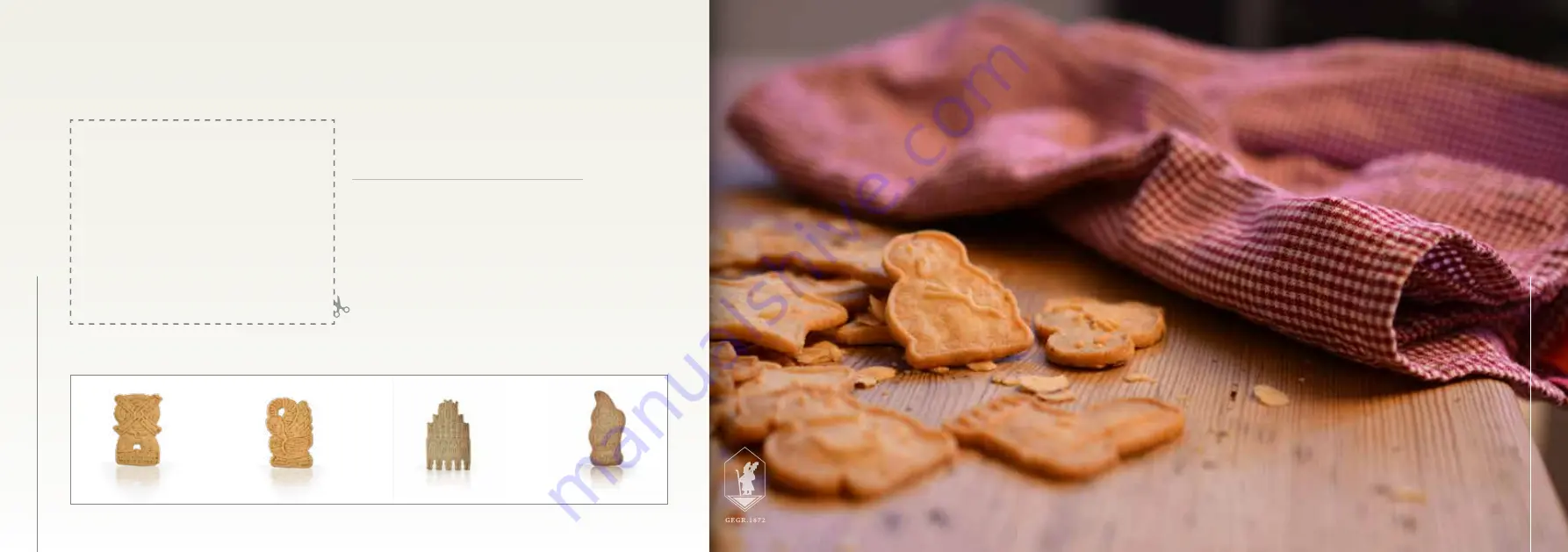
»Speculatius II«
Dough production
Devices: In spiral kneader with centre bar
Step 1:
Mix sugar, spices, salt and butter for 3 min.
Step 2:
Add egg and mix for 2 min.
Step 3:
Add flour and knead it to a smooth dough
Note: Times may vary depending on the amount of dough/ volume of the kneading vessel.
20
21
Ingredients
granulated sugar (fine)
.......................
1 000 g
butter
........................................................
535 g
flour (type 405)
.....................................
1 650 g
egg
............................................................
328 g
spices
..........................................................
37 g
salt
................................................................
6 g
Summary of Contents for F Series
Page 63: ...61 7 5 3 Dimensions Weight F600 1620 980 2220 1158 311 kg 1620 2220 1620 1158...
Page 135: ...133 1 3 2 Click Cross member Clamping screw Sheet transport drive shaft Baking sheet 1 2 3...
Page 179: ...177 If you cannot correct the fault your self contact your dealer or us...
Page 197: ...195 We wish you much joy pleasure with your new machine...
Page 199: ...Do you have any questions Contact us...