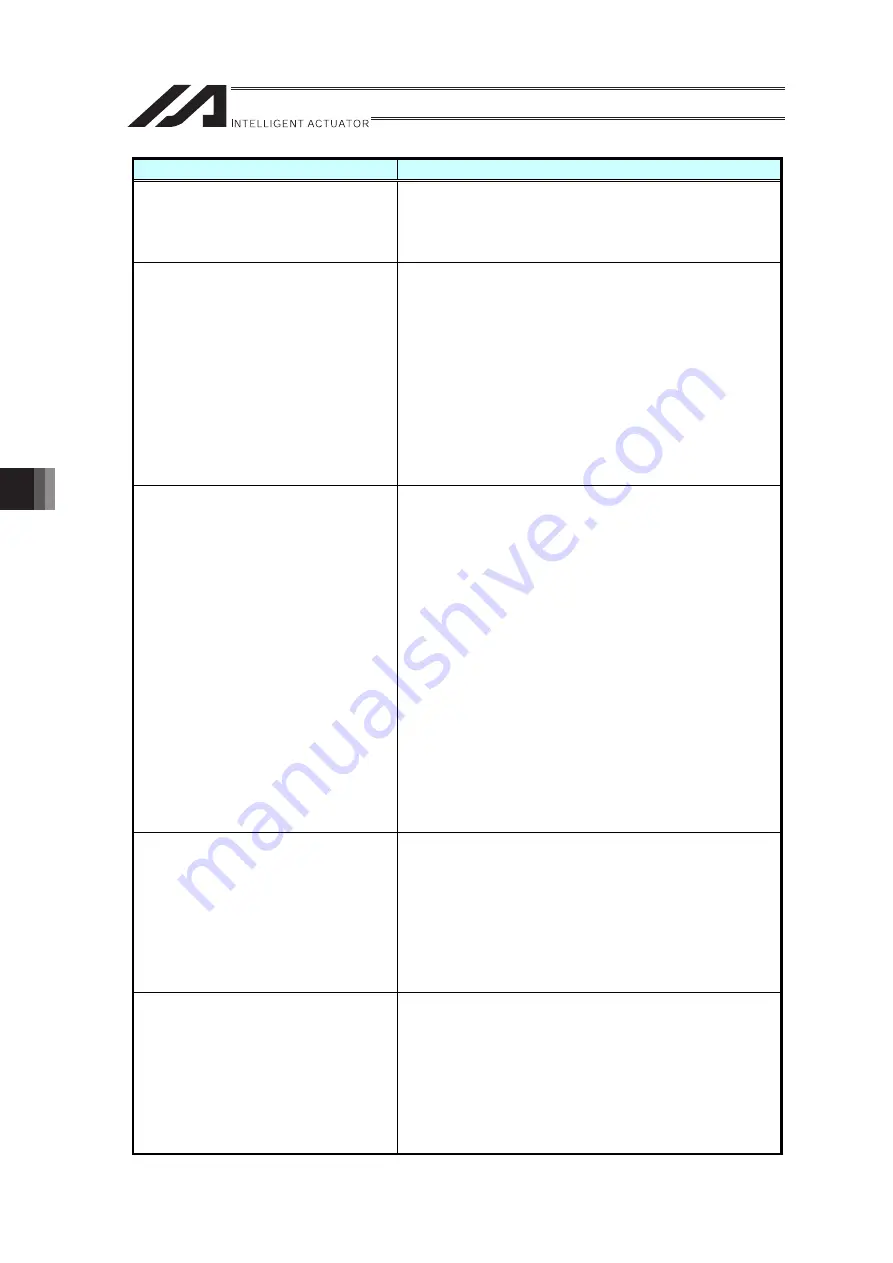
8. T
roubleshooting
170
Phenomenon
Cause/Action
Error No. 4B3 “Extension Motion Control
Axis Pattern Unestablished Error” occurs
[Content and cause]
The extension motion control axis pattern is not established.
[Countermeasure]
Execute the axis pattern setting commands (XAXS and XA16)
to set the valid axis patterns.
Error No. 4B8 “Synchronizing Command
Excess Velocity Error” or Error No. 4B9
“Synchronizing Command Excess
Acceleration/Deceleration Error” occurs
[Content and cause]
The velocity or acceleration/deceleration of the synchronizing
slave axis in operation has exceeded the maximum value set in
the parameter.
(* It also occurs when the safety speed is exceeded if the
safety speed is set valid.)
[Countermeasure]
Take such a counteraction as stated below;
• Set the movement speed of t
he synchronizing master axis
slow, or decrease the acceleration/deceleration
• Decrease the gear ratio if electronic shaft synchronizing
• Revise the cam table profile if electronic cam synchronizing
(Refer to the caution notes for when creating a program or
explanation regarding the electronic cam for details.)
Error No. 4BA “Synchronizing Servo
Command Position Excess Soft limit
Error” occurs
[Content and cause]
The actuator reached a position that it cannot stop in the range
of soft limit with the indicated deceleration while in
synchronizing operation.
[Countermeasure]
Take a counteraction as stated below.
• Narrow the operation range of master axis
• Decrease the gear ratio if electronic shaft synchronizing
• Narrow the slave axis stroke if electronic cam
synchronizing
Also, in case of having the slave axis perform the
synchronizing operation at a position near the soft limit, such
countermeasures as stated below are also effective.
• Set the movement speed of the master axis slow, or
decrease the acceleration/deceleration
• Adjust the setting in the finishing deceleration in
synchronizing operation (Extension Motion Control Each
Axis Parameter No. 15 or Each Axis Parameter No. 209)
• Error No. 4BC “Synchronizing Operation Axis Error
Detection” occurs
(Refer to the caution notes for when creating a program or
explanation regarding the electronic cam for details.)
Error No. 4BC “Synchronizing Operation
Axis Error Detection” occurs
[Content and cause]
There was an error occurred in the axes linked with each other
in synchronizing relation during the synchronizing operation.
[Countermeasure]
Check in the error list and find if there is an error other than
Error No. 4BC is occurred on another slave axis, master axis,
an axis operated with the same commands with the master
axis or a slave axis linked in synchronization in the low-order.
In case that and error except for Error No. 4BC has occurred,
take a counteraction to that error.
Error No. 4C2 “Home-Return Complete
Timeout Error” occurs
[Content and cause]
Home-return operation did not complete in a certain period of
time at the home-return operation of the extension motion
control axis.
[Countermeasure]
Check for a possibility of actuator interference, abnormality in
sliding, adjustment error of servo-motor gain and so on. In case
the timeout occurs even in a normal operation due to long
stroke, extend the setting time in Extension Motion Control
Each Axis Parameter No. 32.
ME0364-2B
Summary of Contents for RA Series
Page 2: ......
Page 4: ...ME0364 2B ...
Page 22: ...1 Outline of Extension Motion Control Feature 14 ME0364 2B ...
Page 40: ...3 Basic Settings 32 ME0364 2B ...
Page 150: ...5 Practical Settings 142 ME0364 2B ...
Page 170: ...6 Parameter Detail 162 ME0364 2B ...
Page 174: ...7 Details of Features 166 ME0364 2B ...
Page 184: ......
Page 185: ......