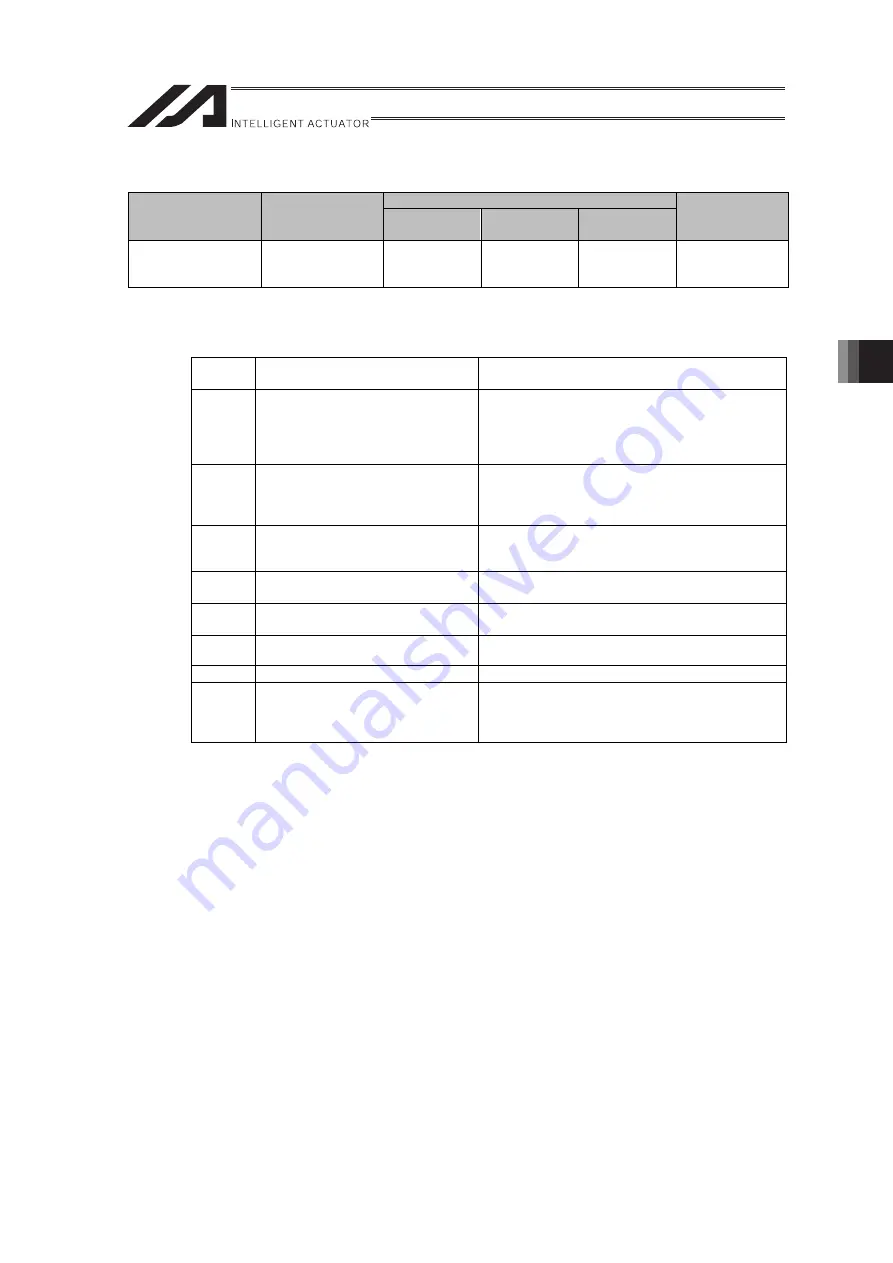
5. Practical Settings
129
[2] ECMD 281/291 (Conversion from Work Coordinates to Each Axis Coordinates in Wrist Unit
Equipped Robot)
Extension condition
(LD, A, O, AB, OB)
Input condition
(I/O/flag)
Command, declaration
Output part
operational type
(output/flag)
Command,
declaration
Operand 1
Operand 2
Optional
Optional ECMD 281/291
Integer
Variable
number
CC
[Function] The position in work coordinate system in a robot equipped with a wrist unit should be
converted into the position in the each axis coordinate system.
■
Operand 2: Contents in Integer Variable No. n
Variable
No.
Data
Contents
n
Top Position Data Number for
Storage of Data Before Conversion
Indicate the position number that the position
data to be converted was stored. (* 1) The work
coordinate system position data to be converted
and the each axis coordinate system current
position data will be stored in the positions in a row.
n+1
Form to be Converted
Indicate the robot form to be converted.
0: Flip 4: Non Flip 8: Form Automatic Select *
* Form to have R-axis angle (absolute value)
minimum selected.
n+2
Top Position Data Number for
Storage of Data After Conversion
Indicate the position number that the converted
each axis coordinate system position data is to
be stored. (* 1)
n+3
Top Position Data Number for
Storage of Work Coordinate Offset
Indicate the position number that the work
coordinate offset was stored. (* 1)
n+4
Top Position Data Number for
Storage of Tool Coordinate Offset
Indicate the position number that the tool
coordinate offset was stored. (* 1)
n+5
Robot Combination Type
Refer to “5.3.6. Settings in Common for
Coordinate Conversion Commands”.
n+6
Wrist Unit Type
0: S Type 1: M Type
n+7
Top Axis Number
Indicate the top axis number of the position that
the data was stored.
* Only ECMD 290 is effective. -1 should always
be indicated for ECMD 280.
* 1 The top position number should be indicated for the standard motion control position.
(Note 1) Indicate the form automatic select when it is not necessary to specify the form for
the form to be converted. In this, the form to have the R-axis angle (absolute
value) minimum will be selected, which enables to have the movement time short.
(Note 2) When the form automatic select is indicated, and if the R-axis is an absolute value
at the same angle, NON FLIP will be selected.
* Work Coordinate Offset
For TTA and MSEL, set the work coordinate offset amount in the work coordinate system number
and execute SLWK Command, and the position will be at the point that is offset by the amount set
in the work coordinate system number.
In the same manner, if the offset amount is set in the position of the work coordinate offset storage
top position data number and the work coordinate offset storage top position data number is
indicated, the position after offset will be figured out.
[Refer to 1.4.5 (2) Positioning on Work Coordinate System in SEL Language Programming Manual]
* Tool Coordinate Offset
For TTA and MSEL, set the tool coordinate offset amount in the tool coordinate system number
and execute SLTL Command, and the position will be at the point that is offset by the amount set
in the tool coordinate system number.
In the same manner, if the offset amount is set in the position of the tool coordinate offset storage
top position data number and the tool coordinate offset storage top position data number is
indicated, the position after offset will be figured out.
[Refer to 1.4.5 (2) Positioning using Tool Coordinate System Offset in SEL Language Programming
Manual]
ME0364-2B
Summary of Contents for RA Series
Page 2: ......
Page 4: ...ME0364 2B ...
Page 22: ...1 Outline of Extension Motion Control Feature 14 ME0364 2B ...
Page 40: ...3 Basic Settings 32 ME0364 2B ...
Page 150: ...5 Practical Settings 142 ME0364 2B ...
Page 170: ...6 Parameter Detail 162 ME0364 2B ...
Page 174: ...7 Details of Features 166 ME0364 2B ...
Page 184: ......
Page 185: ......