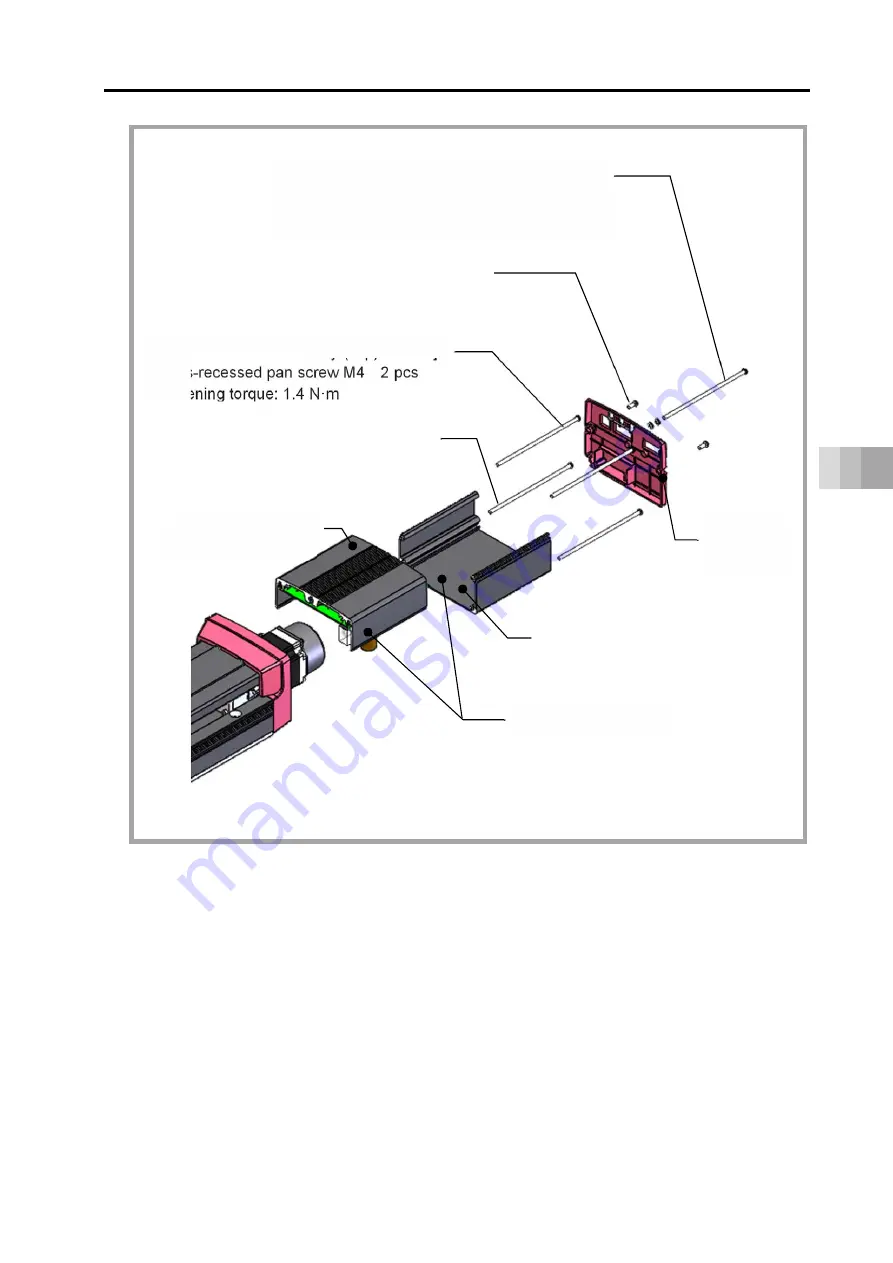
8.6 How to replace components
8-19
8. Maintenan
ce and Inspection
[For grounding connection]
Cross-recessed pan screw M4 1 pc (for FG)
Tightening torque: 1.4 N·m
Spring washer / Plane washer 1pc each
[For end cover assembly fixation]
Cross-recessed tapping screw M4 2 pcs
Tightening torque: 0.8 N·m
[For motor cover assembly (Top) fixation]
Cross-recessed pan screw M4 2 pcs
Tightening torque: 1.4 N·m
End cover
assembly
Motor cover
assembly (Top)
Motor cover assembly
Motor cover assembly (Bottom)
[For motor cover assembly (Bottom)
fixation]
Cross-recessed pan screw M4 2 pcs
Tightening torque: 1.4 N·m
Summary of Contents for ELECYLINDER EC-S13
Page 2: ......
Page 9: ...Chapter 12 Appendix 12 1 Index 12 1 12 2 Revision history 12 5 ...
Page 10: ......
Page 66: ......
Page 116: ...3 38 3 Wiring ...
Page 136: ...4 18 4 Operation ...
Page 138: ......
Page 146: ......
Page 158: ...6 12 6 Parameters ...
Page 160: ......
Page 184: ...7 24 7 Troubleshooting ...
Page 186: ......
Page 230: ...8 6 How to replace components 8 44 8 Maintenance and Inspection Fan unit model number PSA FNB ...
Page 232: ......
Page 238: ...9 6 9 External Dimensions ...
Page 240: ......
Page 244: ...10 4 10 Life ...
Page 246: ......
Page 249: ...Appendix 12 1 Index 12 1 12 2 Revision history 12 5 ELECYLINDER Chapter12 ...
Page 250: ......
Page 256: ......
Page 257: ......