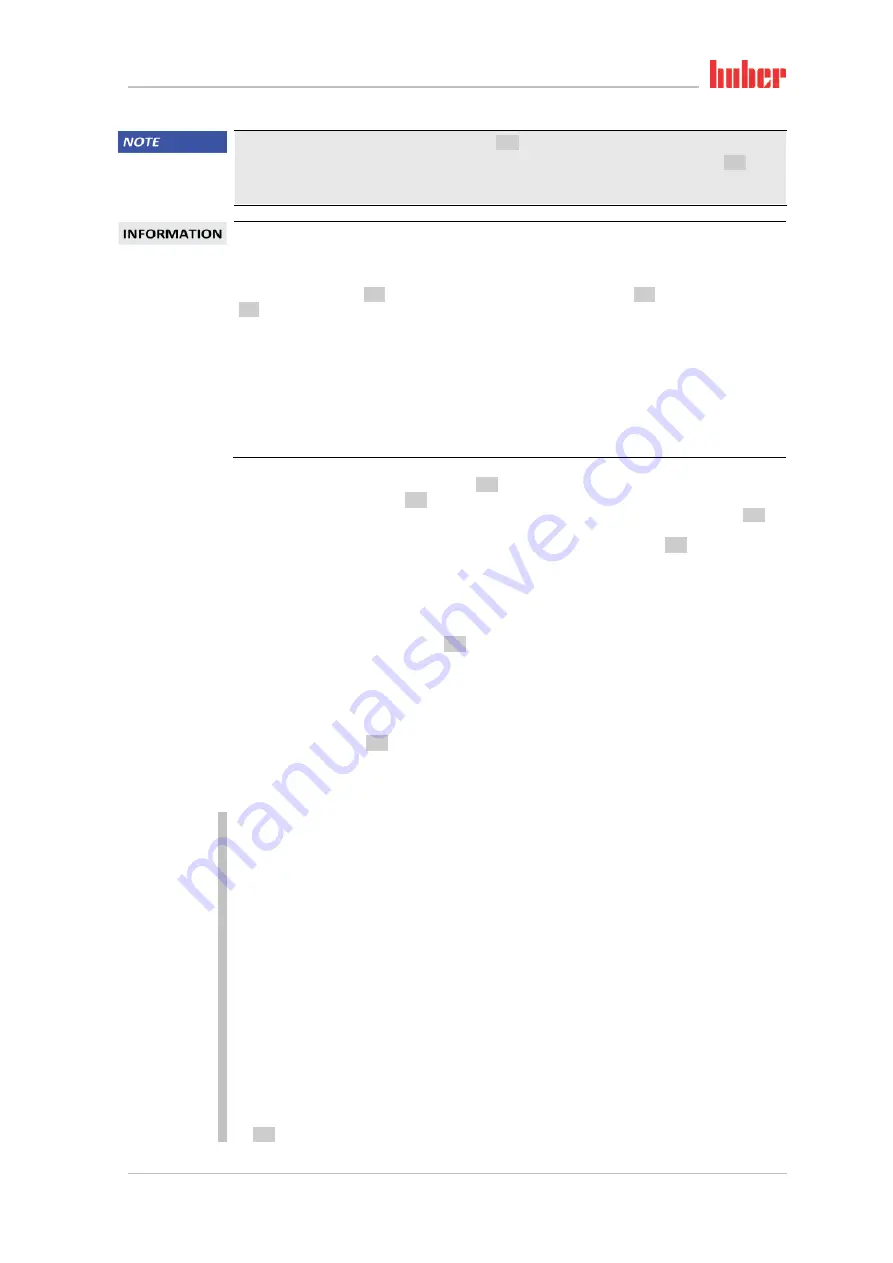
Setup mode
Chapter 4
OPERATION MANUAL
V2.4.0en/22.07.20//17.12
Unistat® T300 Series
69
Inert gas blanket over the >Expansion vessel< [18] over 0.1 bar (g)
MATERIAL DAMAGE CAUSED BY MECHANICAL DAMAGE TO THE >EXPANSION VESSEL< [18]
When using the optional sealing sets for Unistate in connection with a static inert gas overlay, a
pressure limit of 0.1 bar (g) must be used.
When changing from low-boiling thermal fluid (low-boiling components) to higher boiling thermal fluids,
remains of the low-boiling component may remain in the temperature control unit. Depending on the
working temperature, the low-boiling component begins to boil and gas bubbles are formed that cause
the pump pressure to momentarily collapse. This may cause a safety shutdown. The gas bubbles reach
the
>Expansion vessel<
[18] and can escape via the
>Expansion vessel cap<
[22], and the
>Filling port<
[17]. Outgassing will remove residues of the low-boiling component from the thermal fluid.
We recommend inert gas overlay for your temperature control unit. For this we offer the sealing set for
Unistats in the Huber catalog (order No. 9402).
The thermal fluid is protected from environmental influences when using a Unistat. This prevents an
increased accumulation of moisture or the oxidative degradation of the thermal fluid. A further signifi-
cant extension of the useful life of the thermal fluid can be achieved by a static overlay with inert gas.
This is especially true if it is intended to work at the operating temperature limits of the thermal fluid
over an extended period of time. (Hygroscopy, oxidation).
The temperature in the
>Expansion vessel<
[18] is measured by a temperature sensor. The tempera-
ture in the
>Expansion vessel<
[18] may rise due to the expansion of the hot thermal fluid during de-
gassing. A passive cooling device prevents too high a temperature in the
>Expansion vessel<
[18],
thereby protecting the thermal fluid from oxidation too. The factory setting is 45 °C. However, rising
gas bubbles can briefly create temperatures
> 70 °C
in the
>Expansion vessel<
[18]. This is caused by
aging and the nature and quantity of the low-boiling thermal fluid contained in the temperature
control circuit.
Under the category
“Safety”
in the section
“Overtemperature”
, the cut-out value of the installed
temperature sensor can be
set up to 100 °C in the degassing mode. In normal mode, only max. 70 °C
can be set for the
>Expansion vessel<
[18].
Thermal fluids are more or less hygroscopic (water-attracting). This effect increases, the lower the
working temperature. The de-gassing mode described below, which must be
permanently moni-
tored
, also helps to remove any water residues from the temperature control circuit. Using the
optional sealing set (order no. 9402) further reduces the influence of oxidation and hygroscopy in
the
>Expansion vessel<
[18].
PROCEDURE
Activate the menu item “Degassing” after completing the venting operation.
Prerequisite: You have filled the temperature control unit in accordance with the instructions on
page 67 in section
»Filling and venting externally closed application«
and/or cleaned it as per
page 92 in section
»Rinsing the thermal fluid circuit«
.
Go to the “Categories Menu”.
Tap on the category “Temperature Control”.
Tap on the category “Start/Stop”.
Tap on the dialog entry “Start degassing”.
Confirm your choice by tapping on “OK”.
Read the Note and confirm by tapping on “OK”.
Go to the “Home” screen.
Tap on the keypad symbol next to “T
Setpoint
”.
Enter a setpoint using the number keypad that appears. This setpoint
must
be below the boiling
point of the low-boiling thermofluid. The setpoint will be increased in 10 K steps during the de-
gassing process up to the maximum working temperature.
Confirm your entry by tapping on “OK”.
In the display that follows, confirm your entry again by tapping on “OK”.
The correct selection will be displayed graphically and the “setpoint” will be changed immediate-
ly. If tapping on “OK” is not correct, it will be displayed graphically for 2 seconds. The display will
return to the “Home” screen. Try changing the “setpoint” again.
Carry out temperature control to this setpoint until the temperature in the
>Expansion vessel<
[18] no longer rises or even falls.
Summary of Contents for Pilot ONE Unistat T3*0
Page 1: ...Unistat T300 Series...
Page 2: ......
Page 3: ...OPERATION MANUAL Unistat T300 Series...
Page 4: ......
Page 7: ...OPERATION MANUAL V2 4 0en 22 07 20 17 12 Unistat T300 Series 7 Layout of the Home screen...
Page 99: ...Annex Chapter 9 OPERATION MANUAL V2 4 0en 22 07 20 17 12 Unistat T300 Series 99 9 Annex...