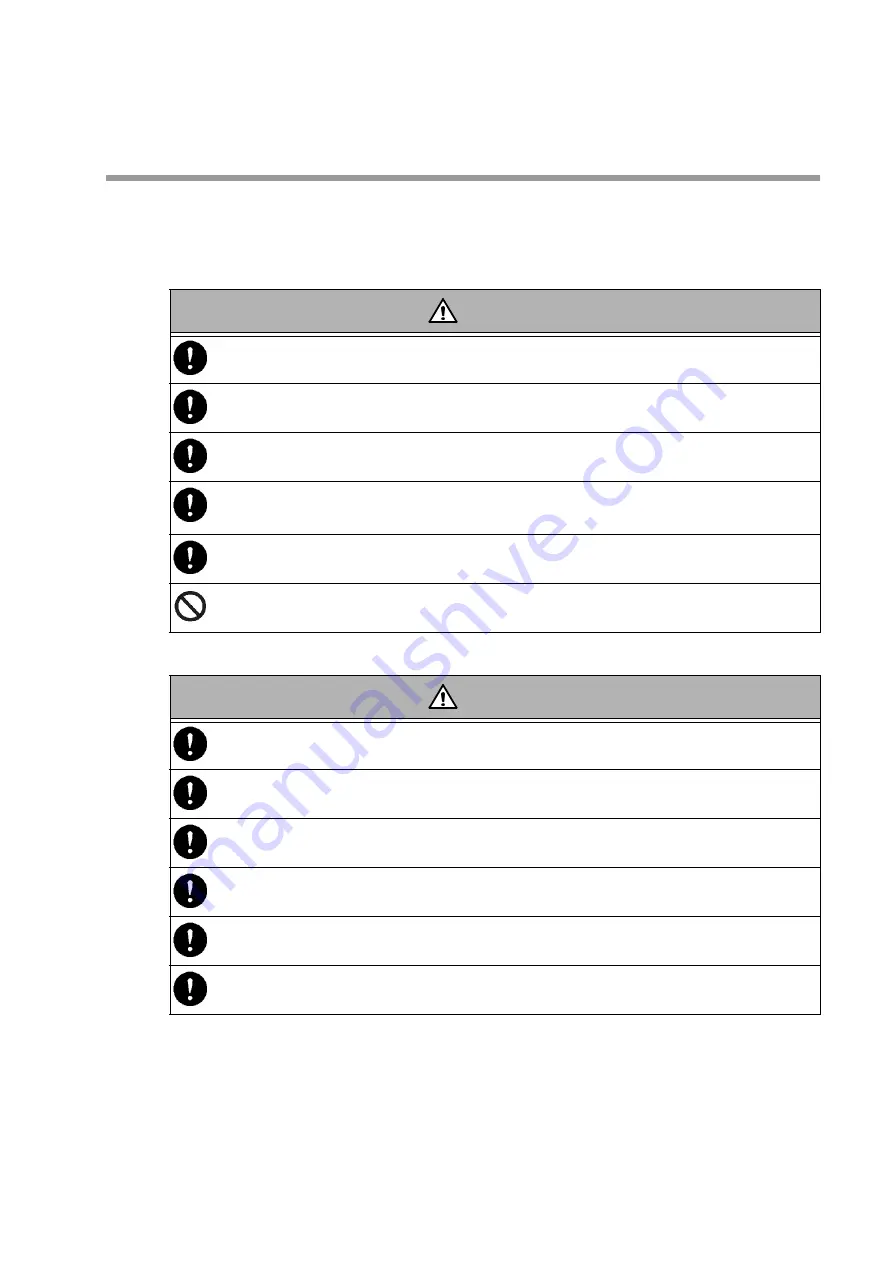
Safety Precautions
This section provides precautions to enable you to use the product safely and correctly and to
prevent injury and damage. The terms of DANGER, WARNING, and CAUTION indicate the
degree of imminency and hazardous situation. Read the precautions carefully as it contains
important safety messages.
WARNING
To connect any load exceeding the contact capacity or any induction load (e.g., a motor or a pump),
be sure to use a power relay exceeding the load rating.
If there is a possibility of a lightning strike, install an arrester on the output side of the converter and on
the side of receiving instruments.
Be sure to ground the grounding terminal (class D grounding).
Electric shock hazard
Be sure to check that no power is supplied before starting work.
An unexpected motion may result in damage to the unit or injury. Be sure to turn OFF the power at the
time of replacement.
Do not turn ON the automatic cleaner while a turbidity detector is filled with water and a valve is
closed. The automatic cleaner may become faulty.
CAUTION
The operation of this equipment at any voltage outside the rated range may damage the equipment.
It is recommended that any fluctuations in power supply voltage fall within a range of ±10%.
When the power source of the instrument is OFF, the C-NC contact is short-circuited. Therefore, be
careful about the connection of load.
If there is any corrosive gas in the installation environment, send clean instrumentation air through the
air purge inlet on the HU-200TB SS-120.
Operation outside the rated range can cause a fault. Therefore, check the power supply voltage.
Wear protective equipment and safety glasses when using chemicals.
Replace desiccants at regular intervals. In particular, cooled water cannot be correctly measured due
to condensation.