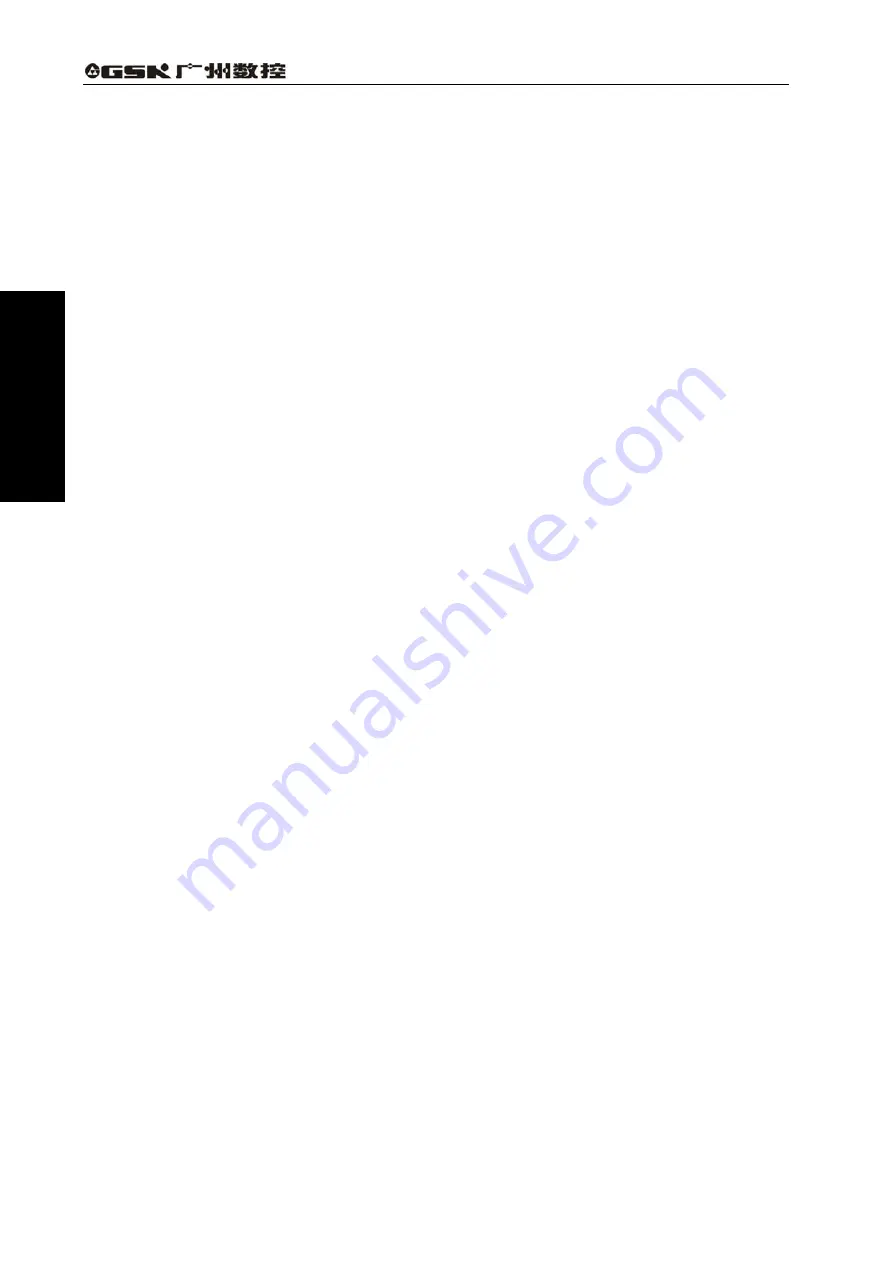
GSK983Ma Milling Machine Center CNC System User Manual
38
Part 1 Programming
Note 1: The G code with is a start G code of each group. Namely, when the power is turned on or the
resetting key is controlled when the system parameter of G code is specified, the G codes are set
up therefore. As for the G22 and G23, the G22 is selected when the power is turned on, G22 or
G23 (one of them is effective before resetting) is then set up.
The selection of start G codes state, such as G00, G01, G43, G44, G49, G90, G91 or G94
,
G95, which
is determined by the parameter 008.
The effective one between G20 and G21 is selected before the power is turned off or the resetting
key is pressed.
Note 2: G codes in group 00 are not modal, which are only valid in its block.
Note 3: When the G codes in the above table are specified, or when an undefined optional G code is
specified to a control device, the alarm (No.0/0) may occur, but the G38 and G39 are ignored.
Note 4: Some G codes can be specified at the same block even if they are not shared the same group.
When two or more G codes in a same group are specified at the block, the last specified G codes
are effective.
Note 5: In the canned cycle mode, if any of the G codes in group 01 are specified, the canned cycle will
automatically cancelled, and the system is then on the state of G80. However, G codes in group
01 are not affected by any G codes in the canned cycle.
Note 6: G70 and G71 can be separately replaced the G20 and G21 (particular G code) by setting the BIT 5
(GSP) of parameter 008.
Note 7: G codes of each group are displayed.
3.5.1 Plain Selection (G17, G18, G19)
Select a plain for circular interpolation and tool compensation by the commands.
G17……XY plain
G18……ZX plain
G19……YZ plain
The movement command is regardless of the plain selection of G17/G18/G19, for example,
when the G17 Z _ is specified, the Z moves.
3.5.2 Positioning (G00)
Use this code, tool positioning is performed at each point of address X, Y, Z or A, B, C, U, V and
W programming, the coordinate value must be specified in the absolute command. The distance from
start to end must be specified in the increment command, and the tool is separately moved at the
rapid traverse rate of each axis, the tool path in positioning is not always a straight line.
Two axes (2 addresses) can be programmed at the same time in a block, but, only one can be
performed for the 4
th
axis.
Specify a G00 positioning
G00
α
_____
β
_____
;
(
α
·
β
=X
、
Y or Z
)
For example: the rapid traverse feedrate is: X axis 9600mm/min
Summary of Contents for GSK983Ma
Page 124: ......
Page 143: ......
Page 185: ......
Page 209: ...Chapter Four Operation 197 Part 2 Operation ...
Page 239: ...Chapter Four Operation 227 Part 2 Operation ...
Page 242: ......
Page 279: ......
Page 296: ...GSK983Ma Milling Machine Center CNC System User Manual 284 Part 2 Operation ...
Page 371: ...Appendix 11 USB Interface Parameter Transfer Operation ...