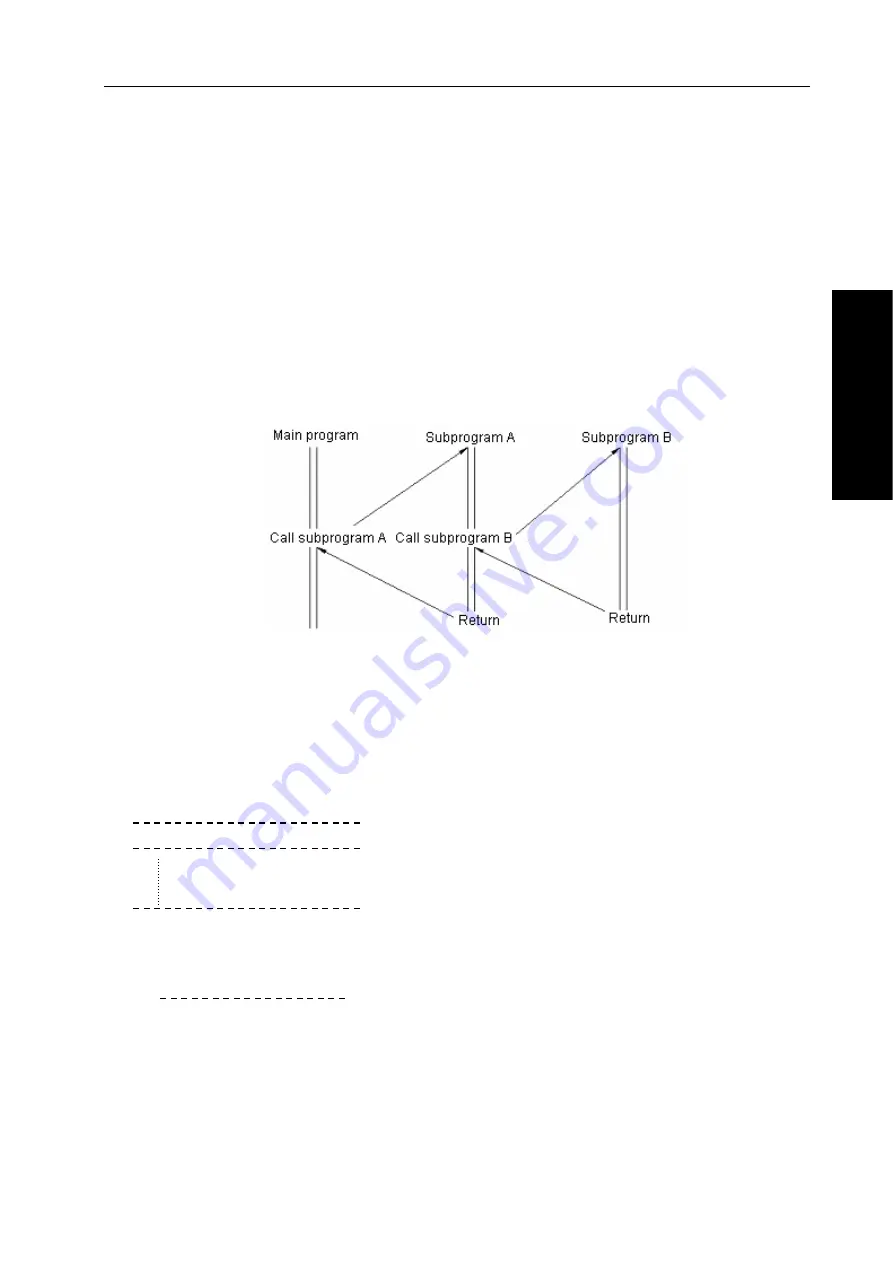
Chapter Three Programming
143
Part 1 Programming
3.8.5 The 2nd Miscellaneous Function (B function)
The working-table indexing can be appointed by the address B and the followed 3 digits.
Different manufacturers have different specifications for the indexing value corresponded with the B
code.
3.9 Sub-program
Some fixed sequence or the repetition area are include in the block, which can be regarded as
sub-program to store the memory, so that the programming can be simplified.
The sub-program can be called in the automatic mode; one sub-program can be called another
one.
When the main program calls a sub-program, which is regarded as single call, the double
sub-program call is as follows:
One sub-program can be repeatedly called by one calling command and one calling command
can be repeatedly called 9999 times.
3.9.1 The Manufacture of the Sub-program
The sub-program is produced by the following format
O
(:)
××××
;
;
;
;
M99
;
The sub-program number after “O” (EIA) or “:” (ISO) at the beginning of the sub-program, single
block may not specify the M99 at the end of the sub-program.
For example:
X M99
;
Refer to the operation from Section 5.17 to 5.19 to how to store the sub-program into the
memory.
Note: In order to compile the NC system with other system, the sub-program of the former block can also be
written into “N××××” instead of the (:) after O.
The system registers the number after the N which is regarded as the sub-program.
Summary of Contents for GSK983Ma
Page 124: ......
Page 143: ......
Page 185: ......
Page 209: ...Chapter Four Operation 197 Part 2 Operation ...
Page 239: ...Chapter Four Operation 227 Part 2 Operation ...
Page 242: ......
Page 279: ......
Page 296: ...GSK983Ma Milling Machine Center CNC System User Manual 284 Part 2 Operation ...
Page 371: ...Appendix 11 USB Interface Parameter Transfer Operation ...