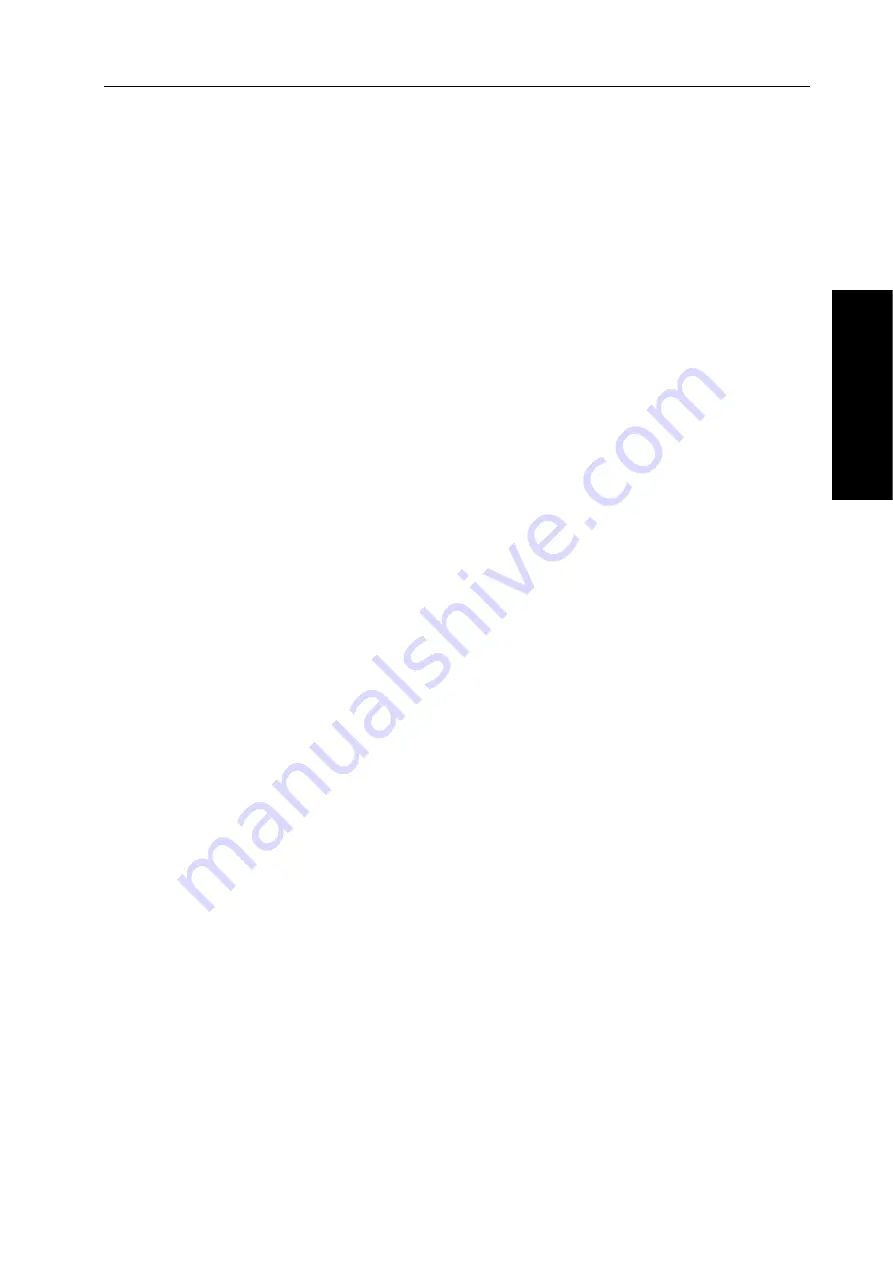
Chapter Three Programming
189
Part 1 Programming
3.11.3 Performance of the Tool Life Management
3.11.3.1 The Calculation of the Tool Life
(1) When tool life is determined in time (min)
Now, T
(
△△△△ △△△△
=
tool life administration invalidation number
+
tool group number) and
M06 are instructed in succession. M06 is specified in machine program again. In cutting method, the
actual time of tool usage is calculated by specified time interval (4s). The time for single block stop,
Feedrate, rapid traverse (positioning), dwell, etc is not included. The maximum set life value is
4300min.
(2) When tool life is determined in number of cycles
Whenever a cycle starting operation is performed, it operates until M02 or M30 is instructed and
NC reset. Then the counter for the used tool group increases by 1. The counter increases by 1 even a
group is instructed for several times in the same program. Life value is up to 9999. Each group of
calculated life and contents of counter will not lose after power failure.
Note: For specifying life in number of cycles, EXTERNAL RESET (ERS) or RESET AND REWIND (RRW)
signal is input in NC when M02 or M30 is executed.
3.11.3.2 The Signals Both the Tool Change and Tool Change Reset
Another tool will be selected in the predetermined order after the end of tool life. When the last
tool in the same tool group has reached its service life, a tool change signal will be given. The tool to
be changed is displayed on LCD. Then the relevant group number is specified and tool change reset
signal input or MDI panel (see 3.11.4.3) operated. All data such as life counter *,@, etc (see 3.11.4.2)
are cleared. All tool groups are changed and reset when tool change signal is automatically released
at the end of tool life. After machining is restored, the group starts selection from the first tool.
Note: For specifying tool life in time, tool change signal is output once it has reached service life and
machining goes on until the end of program. For specifying tool life in number of cycles, tool change
signal is output in case of M02 or M30 reset at the end of tool life.
3.11.3.3 New Tool Selection Signal
When a new tool is selected from a group, tool T code and new tool selection signal are output at
the same time. When a new tool is selected, the signal may be used for the automatic measurement
of tool compensation.
3.11.3.4 Tool Skip Signal
It is possible to forcibly change a tool even it has not reached its service life.
(I) Set the group where the tool is and input tool skip signal. Use the next T code instruction to select
the next tool in the group.
(II) Input tool skip signal without specifying a group number but assuming the selected tool is
specified. Follow (i) for other issues.
Following (I) or (II) shall be set by parameter. Service life starts from 0 no matter which method is
followed. However, output a tool change signal when the tool skip signal inputs the last tool.
Note: When STL or SPL or both of them are lit, it indicates that what is input is neither tool change signal nor
tool skip signal.
3.11.4 The Display and Input of the Tool Data
3.11.4.1 The Display and Modification of the Tool group Number
In the part program storage and edition area, tool group data may be displayed and modified like
Summary of Contents for GSK983Ma
Page 124: ......
Page 143: ......
Page 185: ......
Page 209: ...Chapter Four Operation 197 Part 2 Operation ...
Page 239: ...Chapter Four Operation 227 Part 2 Operation ...
Page 242: ......
Page 279: ......
Page 296: ...GSK983Ma Milling Machine Center CNC System User Manual 284 Part 2 Operation ...
Page 371: ...Appendix 11 USB Interface Parameter Transfer Operation ...