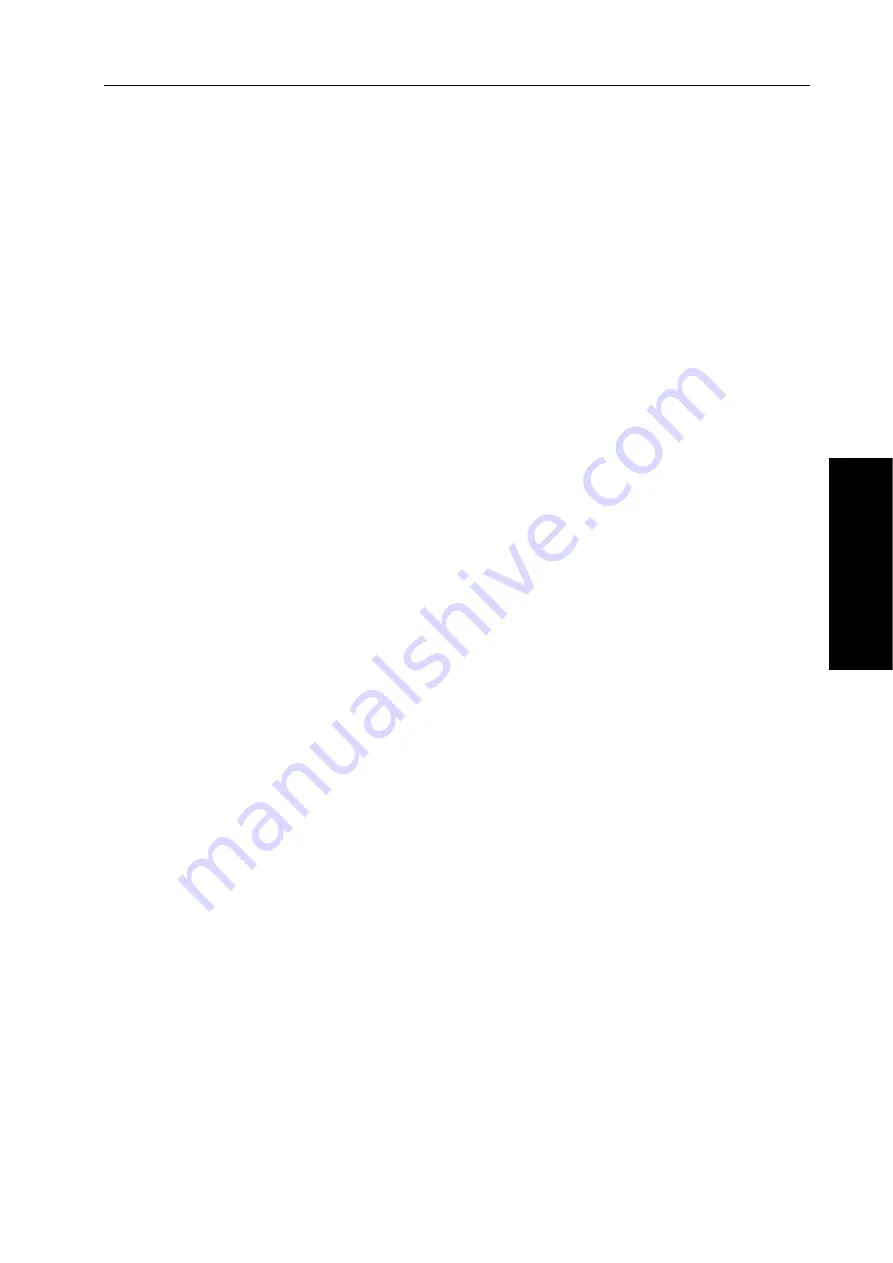
Chapter 8 Spindle Speed Function
117
Ⅲ
Function
Signal type
:
NC
→
PLC
Signal function
:
it means whether the PLC axis is in-position status. The signal becomes 1
when the PLC controlling axis is in-position status. When it is in the axis
movement’s deceleration status, the system executes in-position check;
when it does not reach the position width range, the next command is not
executed.
(10
)
Alarming signal
(
PMC axis control
)
Signal symbol
:
EIALg
(
F130.2
,
F133.2
,
F136.2
,
F139.2
,)
Signal type
:
NC
→
PLC
Signal function
:
it means the alarm statuses relevant with the PLC axis control. The signal
becomes when the PLC controlling axis sends the servo alarm, overtravel
alarm or an alarm occurs. Executing the following operations can release the
alarm, the reset signal ECLRg is set to 1
,
the signal becomes 0. Resolve the
alarm reason about the servo alarm, and reset the CNC. For the overtravel
alarm, move the axis in the stored travel limit, and reset the CNC. In
overtravel alarm, make the axis movement’s commands(including
(
EC0g
~
EC6g
)
)in the stored travel limit.
(
11
)
Axis moving signal
(
PMC axis control
)
Signal symbol
:
EGENg
(
F130.4
,
F133.4
,
F136.4
,
F139.4
)
Signal type
:
NC
→
PLC
Signal function
:
it means the axis’ movement state.
(12) Zero return end signal
Signal symbol
:
reference point return completion signal ZP1
~
ZP5
(
F094.0
~
F094.4
)
Signal type
:
NC
→
PLC
Signal function
:
reference point return signal definitions of PLC axis and CNC controlled axis
are the same. The last digit means the controlled axis’ serial number. The signal becomes
when the reference point return completion and in-position are performed. The signal
becomes “0” when the reference point moving out, emergency stop is performed or the servo
alarm occurs.
8.3 Cs Contour Control Mode
General
The servo spindle can position, and also execute interpolation with other servo axes, and
can command the linear interpolation between the spindle and the servo axis.
Controlling the servo spindle’s spindle speed is called the spindle rotation control (the speed
command S makes the spindle rotate); controlling the spindle’s position is called the spindle
contour control (the movement command makes the spindle rotate). The spindle’s contour
control function is called Cs contour control function.
Switching the spindle rotating control and Cs contour control is determined by PLC sending
output signals. Cs contour controlled axis’ manual run and automatic run are the same with the
general servo axis. (about the reference point return, refer to Function, Section 4.1.
8.3.1 Cs Contour Controlled Axis Setting
When (No37#7 SCS) =“1”
,
Cs contour control function is valid. It can execute the spindle’s Cs
contour control. The axis executing Cs contour control is taken as one axis in the CNC controlled
axes.
(
the 5
th
axis is fixed to be Cs contour axis and the CNC controlled axes are set to 5, which
cannot be changed
)
8.3.2 Switch Spindle Rotation Control/Cs Contour Control
1
. Switch the spindle rotation control mode into Cs contour control mode: when Cs contour control
switch signal CON
(
G033
#
4
)
is “1”
,
the spindle becomes Cs contour controlled axis. the system
is switched into Cs contour control in the spindle rotation, the spindle immediately stops and
executes switch.
2
. Switch Cs contour control mode into the spindle rotation control mode: Cs contour control switch
Summary of Contents for 980TC3 Series
Page 13: ...1 Programming Ⅰ Programming Ⅰ ...
Page 71: ...59 Operation Ⅱ Ⅱ Operation ...
Page 97: ...85 III Ⅲ Function III Function ...
Page 149: ...137 Installation and Connection Ⅳ Ⅳ Installation and Connection ...
Page 209: ...197 附 录 Appendix ...