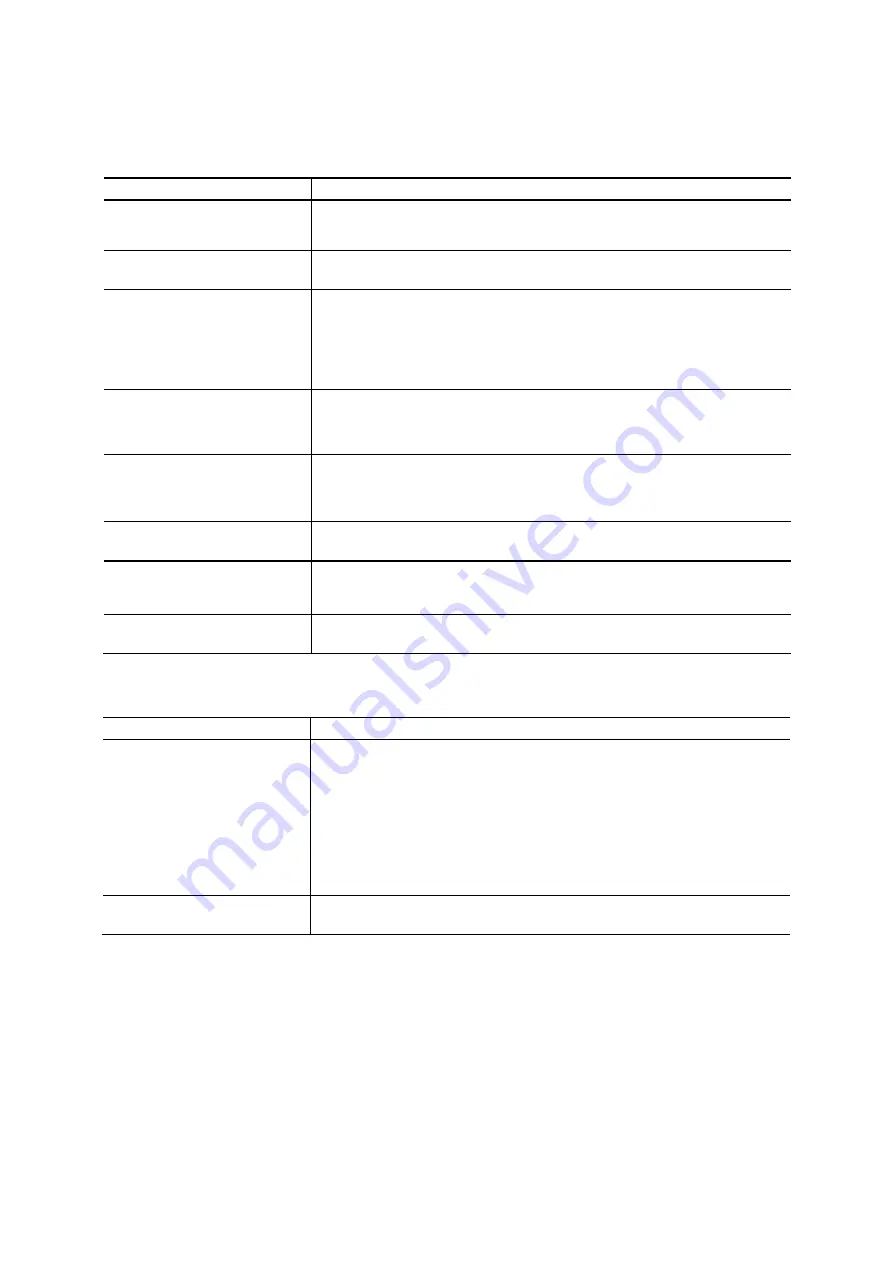
6-16
[ 10 ]
0h4
Motor protection (PTC/NTC thermistor)
Problem Temperature of the motor has risen abnormally.
Possible Causes
What to Check and Suggested Measures
(1) The temperature around the
motor exceeded the motor's
specification range.
Measure the temperature around the motor.
Î
Lower the temperature.
(2) Cooling system for the motor
defective.
Check if the cooling system of the motor is operating normally.
Î
Repair or replace the cooling system of the motor.
(3) Overload.
Measure the output current.
Î
Reduce the load (e.g. Use the heat sink overheat early warning (E01 through E07) or
the overload early warning (E34) and reduce the load before the overload protection
is activated.). (In winter, the load tends to increase.)
Î
Lower the temperature around the motor.
Î
Increase the motor sound (Carrier frequency) (F26).
(4) The activation level (H27) of
the PTC thermistor for motor
overheat protection was set
inadequately.
Check the PTC thermistor specifications and recalculate the detection voltage.
Î
Modify the data of function code H27.
(5) Settings for the PTC/NTC
thermistor are improper.
Check the setting of the thermistor mode selection (H26) and the slider position of
terminal [C1] property switch SW5.
Î
Change the H26 data in accordance with the thermistor used and set the SW5 to the
PTC/NTC position.
(6) Excessive torque boost
specified. (F09*)
Check whether decreasing the torque boost (F09*) does not stall the motor.
Î
If no stall occurs, decrease the F09* data.
(7) The V/f pattern did not match
the motor.
Check if the base frequency (F04*) and the rated voltage at base frequency (F05*) match
the values on the motor's nameplate.
Î
Match the function code data with the values on the motor's nameplate.
(8) Incorrect setting of function
code data.
Although no PTC/NTC thermistor is used, the thermistor mode is enabled (H26).
Î
Set the H26 data to "0" (Disable).
[ 11 ]
dbh
Braking resistor overheated
Problem The electronic thermal protection for the braking resistor has been activated.
Possible Causes
What to Check and Suggested Measures
(1) Braking load is too heavy.
Reconsider the relationship between the braking load estimated and the real load.
Î
Lower the real braking load.
Î
Review the selection of the braking resistor and increase the braking capability
(Modification of related function code data (F50, F51, and F52) is also required.)
(2) Specified deceleration time is
too short.
Recalculate the deceleration torque and time needed for the load currently applied, based
on a moment of inertia for the load and the deceleration time.
Î
Increase the deceleration time (F08, E11, E13, E15, and H56).
Î
Review the selection of the braking resistor and increase the braking capability.
(Modification of related function code data (F50, F51, and F52) is also required.)
(3) Incorrect setting of function
code data F50, F51, and F52.
Recheck the specifications of the braking resistor.
Î
Review data of function codes F50, F51, and F52, then modify them.
Note:
The inverter issues an overheat alarm of the braking resistor by monitoring the magnitude of the braking load, not by
measuring its surface temperature.
When the braking resistor is frequently used so as to exceed the settings made by function codes F50, F51, and F52, therefore, the
inverter issues an overheat alarm even if the surface temperature of the braking resistor does not rise. To squeeze out full
performance of the braking resistor, configure function codes F50, F51, and F52 while actually measuring the surface temperature of
the braking resistor.
Summary of Contents for FRENIC-MEGA
Page 36: ...2 6 Unit inch mm Refer to Section 2 3 3 9...
Page 356: ...MEMO...