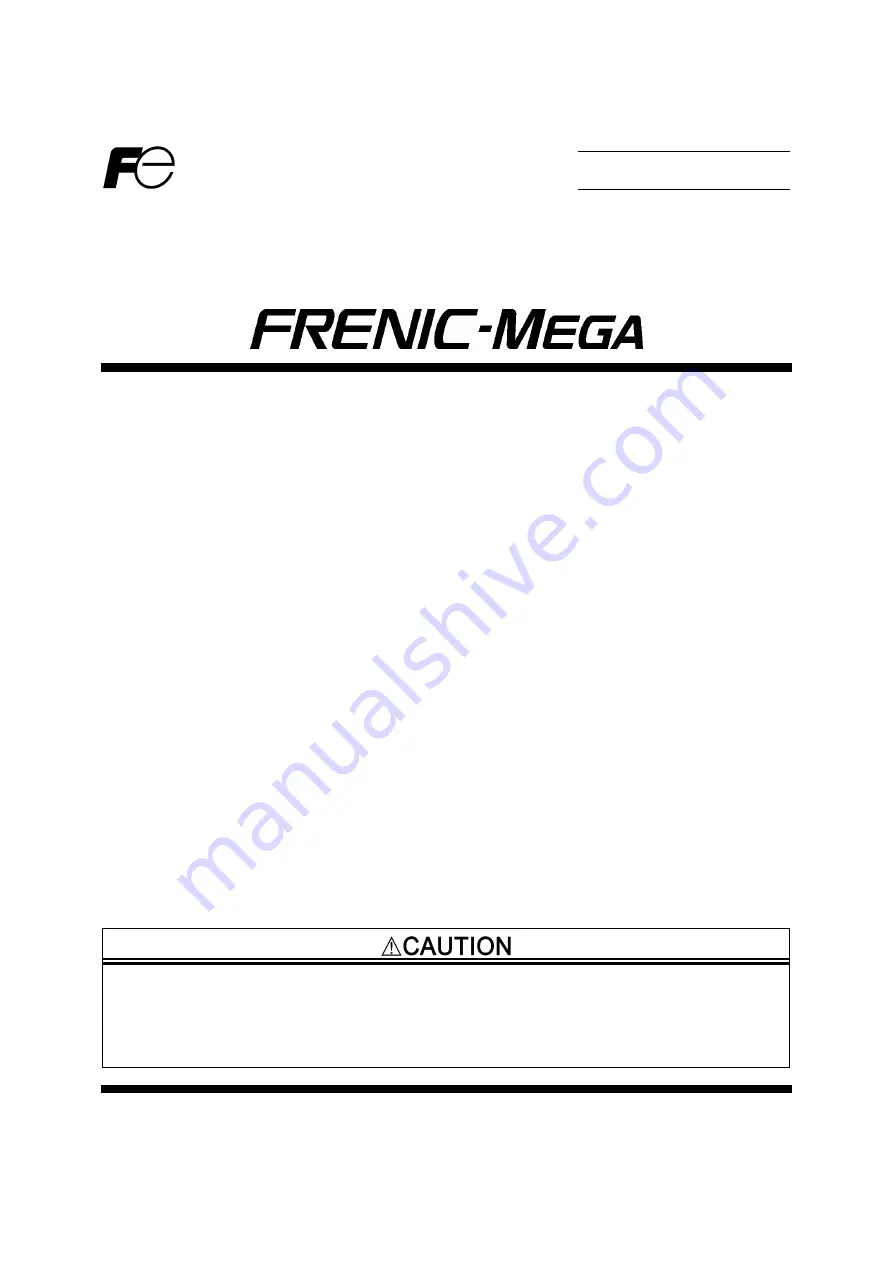
Instruction Manual
High Performance, Multifunction Inverter
This product is designed to drive a three-phase induction motor. Read through this manual to become familiar with proper
handling and correct use.
Improper handling might result in incorrect operation, short life cycle, or failure of this product as well as the motor.
Deliver this manual to the end user of this product. Keep this manual in a safe place until this product is discarded.
For instructions on how to use an optional device, refer to the instruction and installation manuals for that optional device.
Fuji Electric Co., Ltd.
Fuji Electric Corp. of America
INR-SI47-1457a-E
Summary of Contents for FRENIC-MEGA
Page 36: ...2 6 Unit inch mm Refer to Section 2 3 3 9...
Page 356: ...MEMO...