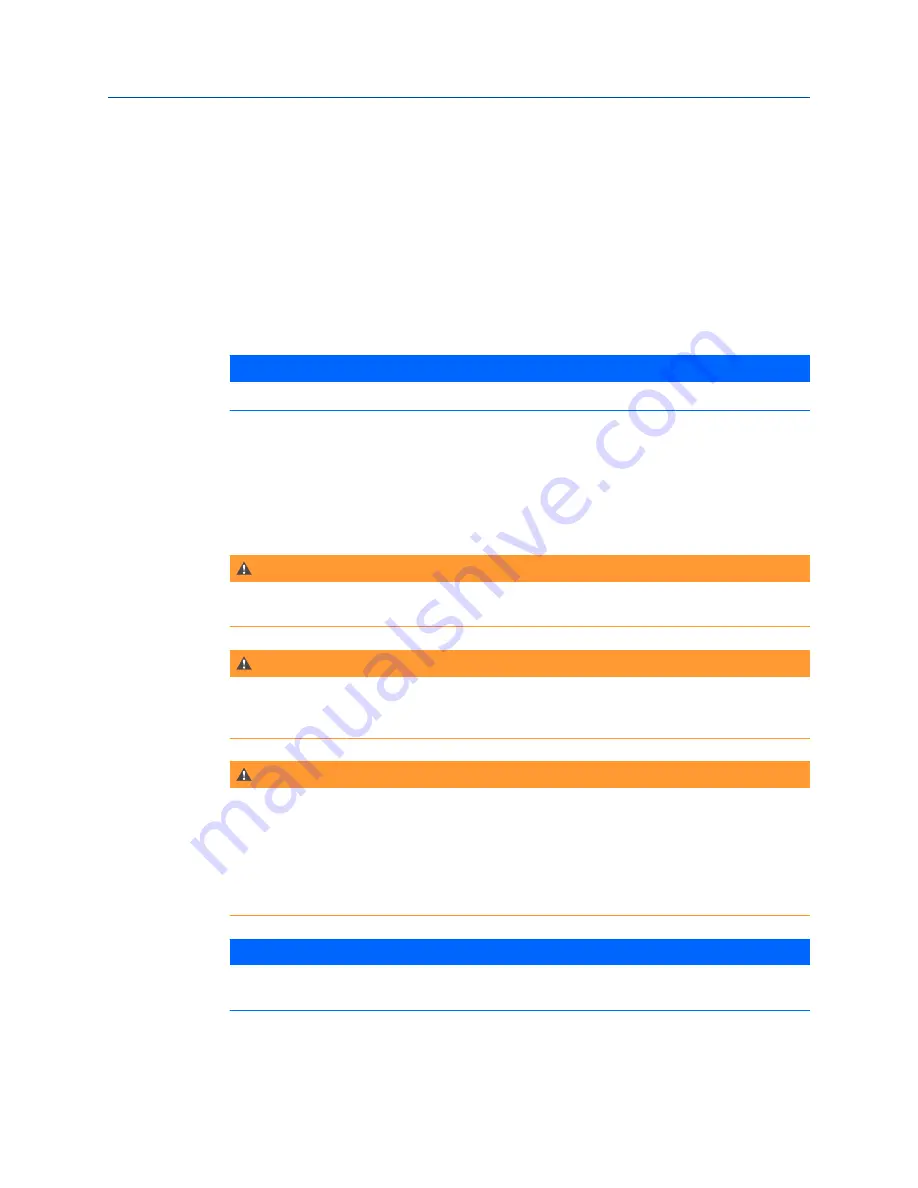
b. Oxygen
c. Pressure
d. Water vapor
e. Logic input
You can set these parameters in Mode
5
.
describes each of these parameters.
During normal operation, the plant status registers as
ON
. However, if the plant status
input is lost, the status changes to
OFF
, and the averaging data (seconds, minutes, hours,
days) is not updated.
NOTICE
During normal operation, do not link terminals PS1 and PS2 together.
2.7
Electrical connections
All equipment wiring must conform to local and national codes. Read and observe the
following instructions before making electrical connections.
WARNING!
ELECTRIC SHOCK
Disconnect and lock out power before connecting the power supply to the analyzer.
WARNING!
ELECTRIC SHOCK
Install all protective covers and safety ground leads after installation. Failure to install covers
and ground leads could result in serious injury or death.
WARNING!
ELECTRIC SHOCK
To meet the safety requirements of IEC 1010 (EC requirement) and ensure safe operation of this
equipment, connect to the main electrical power supply through a circuit breaker (min. 10 A)
which will disconnect all current-carrying conductors during a fault situation.This circuit
breaker should also included a mechanically operated isolating switch. If not, then locate
another external means of disconnecting the supply from the equipment close by. Circuit
breakers or switches must comply with a recognized standard, such as IEC 947.
NOTICE
To maintain proper earth grounding, ensure a positive connection exists between the
transmitter housing and earth. The connecting ground wire must be 14 AWG minimum.
Install
18
Rosemount CCO 5500
Summary of Contents for Rosemount CCO 5500
Page 4: ......
Page 8: ...Contents iv Rosemount CCO 5500 ...
Page 28: ...System Wiring Diagram Figure 2 7 Install 20 Rosemount CCO 5500 ...
Page 32: ...Install 24 Rosemount CCO 5500 ...
Page 88: ...Operation 80 Rosemount CCO 5500 ...
Page 98: ...Maintenance 90 Rosemount CCO 5500 ...
Page 108: ...Troubleshooting 100 Rosemount CCO 5500 ...
Page 110: ...Spare parts 102 Rosemount CCO 5500 ...
Page 122: ...Return equipment to the factory 114 Rosemount CCO 5500 ...
Page 123: ...Return equipment to the factory Reference Manual 115 ...