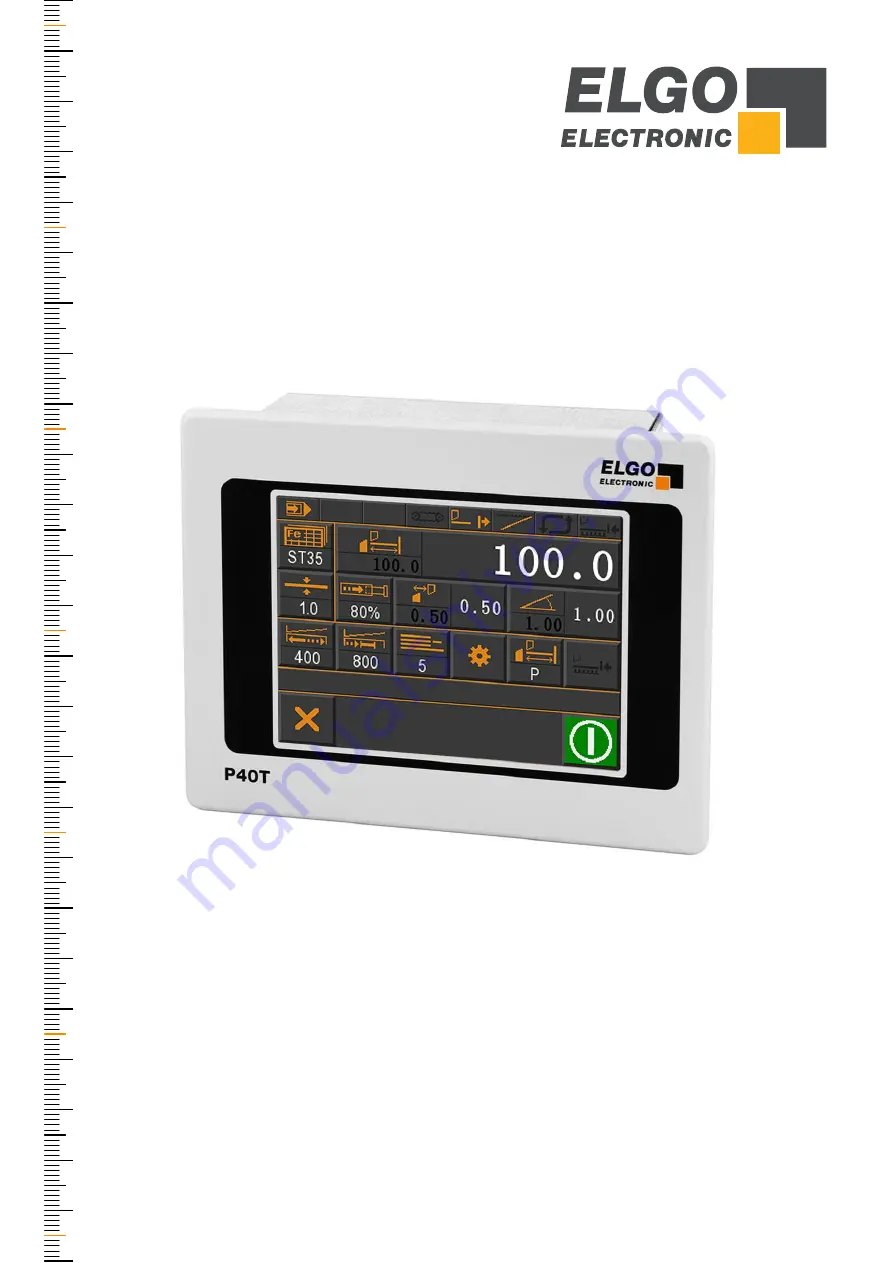
Operating Manual
SERIES
P40T-002
Programmable Touch Screen Controller for
Guillotine Shears
TFT-Display with touch operation
Manual inching, single and program mode
Integrated program memory and auto-cutting machine
Material depending calculation of gap, angle & pressure
Sheet support and return to the front function
Analog inputs and outputs
Digital outputs up to 2 A
799000681 / Rev. 7 / 2019-05-13
Translation of the original operating manual
Summary of Contents for P40T-002 Series
Page 49: ...Service Mode Parameter Level 49 11 11Sub Menu Times System Figure 33 System Times ...
Page 83: ... 83 Notes ...
Page 84: ... 84 Notes ...
Page 85: ... 85 Notes ...