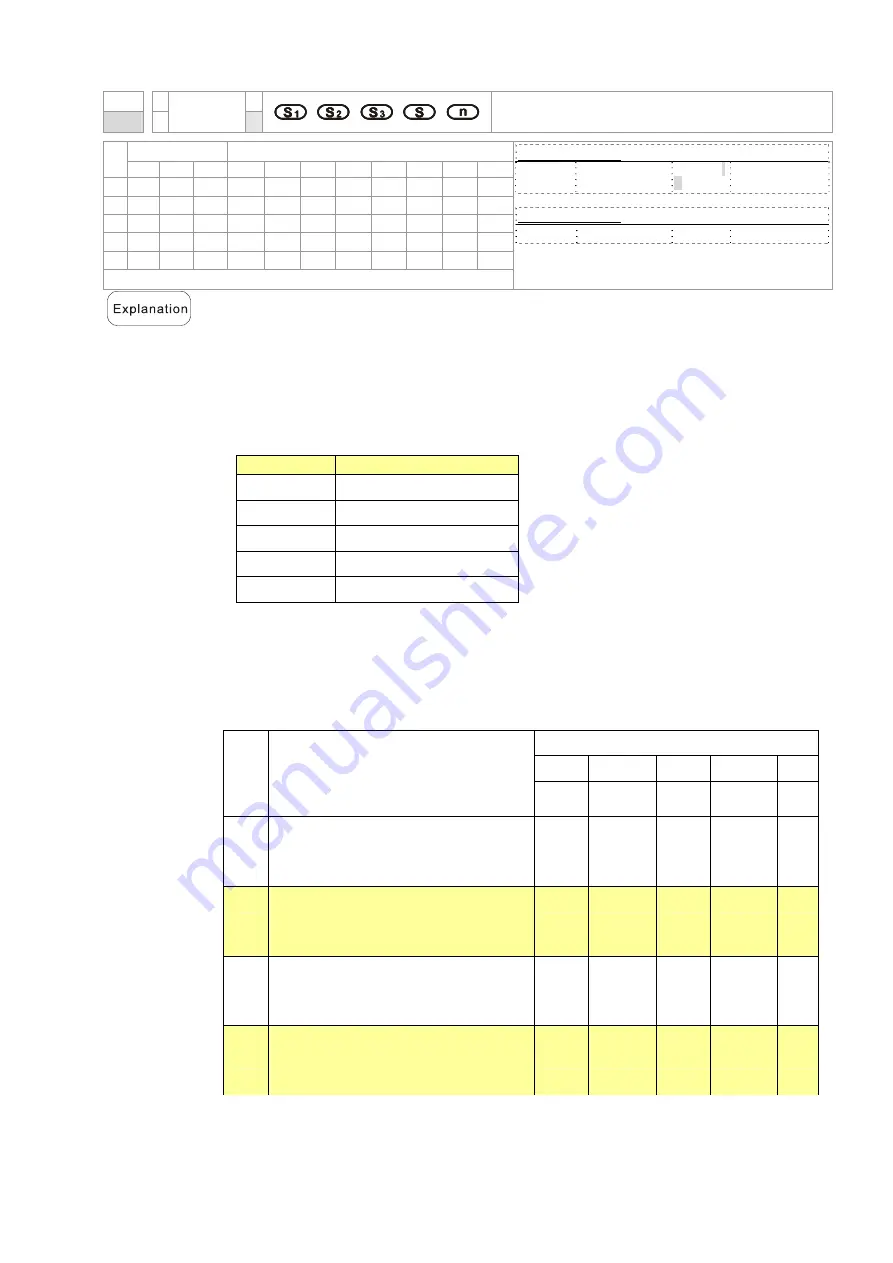
Chapter 16 PLC Function
CT2000 Series
16-68
API
MODRW
MODBUS data read/write
150
P
Bit device
Word device
16-bit command (5 STEP)
MODRW
Continuous
execution type
MODRW
P
Pulse
execution type
32-bit command
-
-
-
-
Flag signal:
M1077 M1078 M1079
X Y M K H KnX
KnY
KnM
T
C
D
S1
*
*
*
S2
*
*
*
S3
*
*
*
S
*
n
*
*
*
S1: online device address. S2: communications function code. S3: address of
data to read/write. S: register for data to be read/written is stored. N: length of data
to be read/written.
COM1 must be defined as controlled by the PLC (set P9-31 = -12) before using
this command, and the corresponding communications speed and format must
also be set (set P09-01 and P09-04). S2: communications function code.
Currently only supports the following function code; the remaining function code
cannot be executed.
Function
Description
H 02
Input read
H 03
Read word
H 06
Write single word
H 0F
Write multiple coils
H10 Write
single
word
After executing this command, M1077, M1078 and M1079 will be immediately
changed to 0.
As an example, when CT2000 must control another converter and PLC, if the
converter has a station number of 10 and the PLC has a station number of 20, see
the following example:
Control slave device converter
Seria
l No.
Example
MODRW command
S1 S2 S3 S4 n
Node
ID
Function
code
Addres
s
Register
Leng
th:
1
Reads 4 sets of data comprising the
converter slave device parameters
P01-00 to P01-03, and saves the read
data in D0 to D3
K10
H3 H100 D0 K4
2
Reads 3 sets of data comprising the
converter slave device addresses
H2100 to H2102, and saves the read
data in D5 to D7
K10
H3
H2100
D5
K3
3
Reads 3 sets of data comprising the
converter slave device parameters
P05-00 to P05-03, and writes the
values as D10 to D12
K10
H10 H500 D10 K3
4
Writes 2 sets of data comprising the
converter slave device addresses
H2000 to H2001, and writes the values
as D15 to D16
K10
H10
H2000
D15
K2
Summary of Contents for CT2000 Series
Page 5: ...Chapter 1 Introduction CT2000 Series 1 2 Model Name VFD 750 CT 43 F 00 A6 Serial Number...
Page 22: ...Chapter 1 Introduction CT2000 Series 1 19 Digital Keypad KPC CC01 KPC CE01 Unit mm inch...
Page 23: ...Chapter 1 Introduction CT2000 Series 1 20 This page intentionally left blank...
Page 41: ...Chapter 4 Wiring CT2000 Series 4 6 This page intentionally left blank...
Page 71: ...Chapter 7 Optional Accessories CT2000 Series 7 18 Wall Mounting Embedded Mounting...
Page 87: ...Chapter 8 Optional Cards CT2000 Series 8 8 PG Card intallation...
Page 88: ...Chapter 8 Optional Cards CT2000 Series 8 9 Disconneting the extension card...
Page 92: ...Chapter 8 Optional Cards CT2000 Series 8 13 PG2 Wiring Diagram...
Page 95: ...Chapter 8 Optional Cards CT2000 Series 8 16 PG2 Wiring Diagram...
Page 117: ...Chapter 8 Optional Cards CT2000 Series 8 38 This page intentionally left blank...
Page 259: ...Chapter 12 Description of Parameter Settings CT2000 Series 12 1 03 11...
Page 260: ...Chapter 12 Description of Parameter Settings CT2000 Series 12 1 03 12...
Page 263: ...Chapter 12 Description of Parameter Settings CT2000 Series 12 1 03 15...
Page 266: ...Chapter 12 Description of Parameter Settings CT2000 Series 12 1 03 18...
Page 397: ...Chapter 13 Warning Codes CT2000 Series 13 8 This page intentionally left blank...
Page 407: ...Chapter 14 Fault Codes and Descriptions CT2000 Series 14 10 This page intentionally left blank...
Page 489: ...Chapter 16 PLC Function CT2000 Series 16 48 LD X1 Load Contact a of X1 OUT Y1 Drive Y1 coil...
Page 592: ...Chapter 16 PLC Function CT2000 Series 16 151...
Page 594: ...Chapter 16 PLC Function CT2000 Series 16 153...
Page 597: ...Chapter 16 PLC Function CT2000 Series 16 156 This page intentionally left blank...