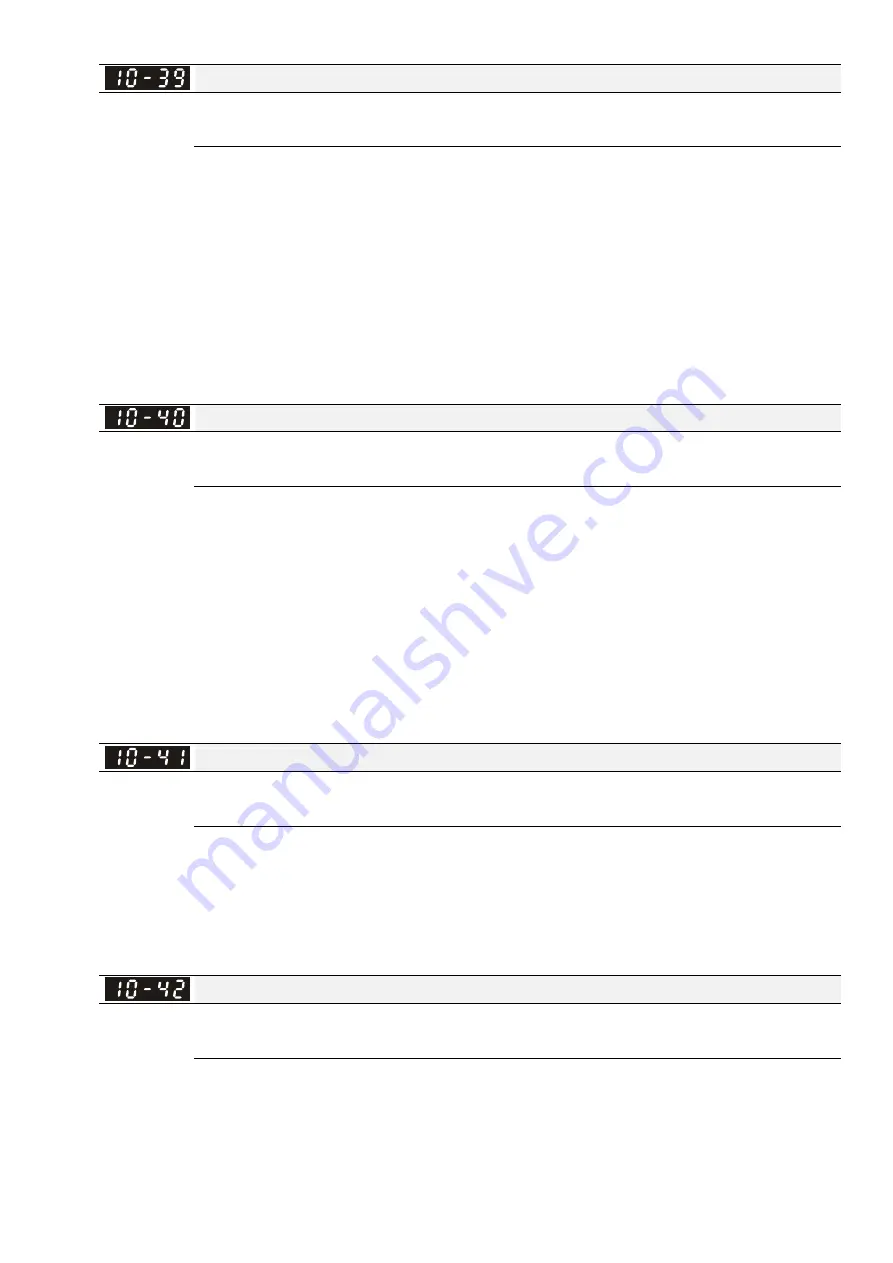
Chapter 12 Description of Parameter Settings
CT2000 Series
12.2-00-10
Frequency Point when switch from I/F Mode to PM Sensorless Mode
Factory
Setting:20.00
Settings 0.00~599.00Hz
The parameter is the switch point which is from low frequency to high frequency. It will
influence high/low frequency area of speed observer.
If the switch point is too low, motor will generate not enough back emf to let the speed
estimator measure the right rotator’s position and speed, and cause stall and oc when the
frequency of switch point is running.
If the switch point is too high, the active area of I/F will too wide, and then it will generate
larger current to make it cannot save energy. (The reason is that if the current of Pr10-31
sets too high, and the high switch point will make the drive keeps outputting with the setting
value of Pr10-31)
Frequency Point when Switch from PM Sensorless Observation to I/F Mode
Factory Setting: 20.00
Settings 0.00~599.00Hz
The parameter is the switch point which is from high frequency to low frequency. It will
influence high/low frequency area of speed observer.
If the switch point is too low, motor will generate not enough back emf to let the speed
estimator measure the right rotator’s position and speed, and cause stall and oc when the
frequency of switch point is running.
If the switch point is too high, the active area of I/F will too wide, and then it will generate
larger current to make it cannot save energy. (The reason is that if the current of Pr10-31
sets too high, and the high switch point will make the drive keeps outputting with the setting
value of Pr10-31)
I/F Mode and Low Pass-filter time of Id
Factory Setting: 0.2
Settings 0.0~6.0 sec
The parameter is the filter time of Pr10-31. This can make the magnetic field of I/F increases
to current command value progressively and smoothly.
If Id has to be higher slowly, then increase the parameter to avoid Step of current occurring
on start-up. If decrease (the minimum is 0) it, the speed of current to rise will be fast, and
occurs Step.
Voltage pulse width
Factory
Setting:10
Settings 0~50 ms
The angle detection is 3:6-pulse. The parameter influences the value of pulse during the
angle detection. The larger the pulse is, the higher of the accuracy of rotator’s position. But it
might cause oc easily.
Increase the parameter when the running direction and the command are opposite while
start-up. If oc occurs in the start-up moment, then decrease the parameter.
Summary of Contents for CT2000 Series
Page 5: ...Chapter 1 Introduction CT2000 Series 1 2 Model Name VFD 750 CT 43 F 00 A6 Serial Number...
Page 22: ...Chapter 1 Introduction CT2000 Series 1 19 Digital Keypad KPC CC01 KPC CE01 Unit mm inch...
Page 23: ...Chapter 1 Introduction CT2000 Series 1 20 This page intentionally left blank...
Page 41: ...Chapter 4 Wiring CT2000 Series 4 6 This page intentionally left blank...
Page 71: ...Chapter 7 Optional Accessories CT2000 Series 7 18 Wall Mounting Embedded Mounting...
Page 87: ...Chapter 8 Optional Cards CT2000 Series 8 8 PG Card intallation...
Page 88: ...Chapter 8 Optional Cards CT2000 Series 8 9 Disconneting the extension card...
Page 92: ...Chapter 8 Optional Cards CT2000 Series 8 13 PG2 Wiring Diagram...
Page 95: ...Chapter 8 Optional Cards CT2000 Series 8 16 PG2 Wiring Diagram...
Page 117: ...Chapter 8 Optional Cards CT2000 Series 8 38 This page intentionally left blank...
Page 259: ...Chapter 12 Description of Parameter Settings CT2000 Series 12 1 03 11...
Page 260: ...Chapter 12 Description of Parameter Settings CT2000 Series 12 1 03 12...
Page 263: ...Chapter 12 Description of Parameter Settings CT2000 Series 12 1 03 15...
Page 266: ...Chapter 12 Description of Parameter Settings CT2000 Series 12 1 03 18...
Page 397: ...Chapter 13 Warning Codes CT2000 Series 13 8 This page intentionally left blank...
Page 407: ...Chapter 14 Fault Codes and Descriptions CT2000 Series 14 10 This page intentionally left blank...
Page 489: ...Chapter 16 PLC Function CT2000 Series 16 48 LD X1 Load Contact a of X1 OUT Y1 Drive Y1 coil...
Page 592: ...Chapter 16 PLC Function CT2000 Series 16 151...
Page 594: ...Chapter 16 PLC Function CT2000 Series 16 153...
Page 597: ...Chapter 16 PLC Function CT2000 Series 16 156 This page intentionally left blank...