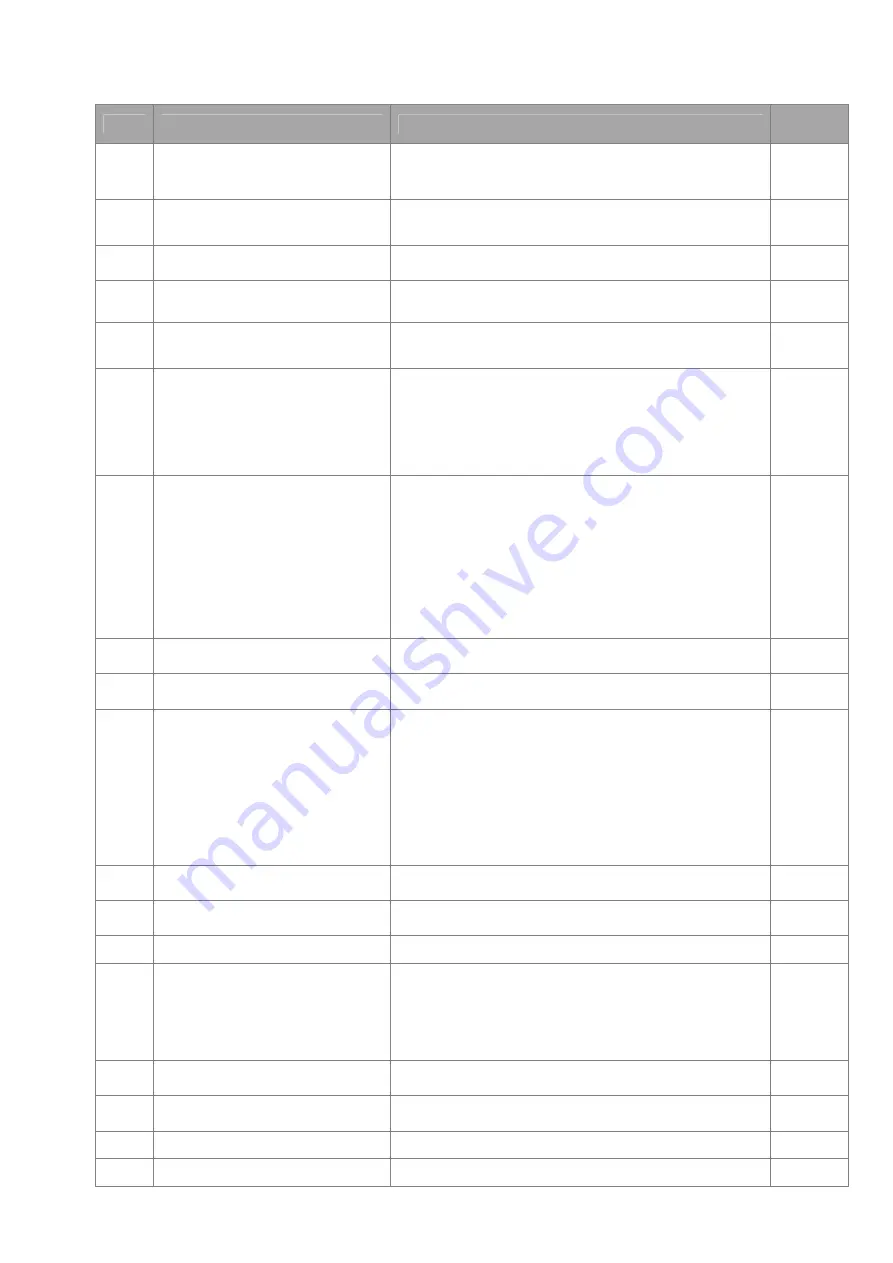
Chapter 11 Summary of Parameter Settings
CT2000 Series
11-22
06 Protection Parameters
Pr.
Explanation
Settings
Factory
Setting
06-00
Low Voltage Level
460V:
Frame A to D: 300.0~440.0Vdc
Frame E and frames above E: 380.0~440.0V
360.0
400.0
06-01 Over-voltage
Stall
Prevention
0: Disabled
460V: 0.0~900.0Vdc
760.0
06-02 Selection for Over-voltage Stall
Prevention
0: Traditional over-voltage stall prevention
1: Smart over-voltage prevention
0
06-03 Over-current Stall Prevention
during Acceleration
Light duty: 0~160%(100%: drive’s rated current)
Heavy duty: 0~180%(100%: drive’s rated current)
120
150
06-04 Over-current Stall Prevention
during Operation
Light duty: 0~160%(100%: drive’s rated current)
Heavy duty: 0~180%(100%: drive’s rated current)
120
150
06-05
Accel. /Decel. Time Selection of
Stall Prevention at Constant
Speed
0: by current accel/decel time
1: by the 1st accel/decel time
2: by the 2nd accel/decel time
3: by the 3rd accel/decel time
4: by the 4th accel/decel time
5: by auto accel/decel
0
06-06 Over-torque Detection Selection
(OT1)
0: No function
1: Over-torque detection during constant speed
operation, continue to operate after detection
2: Over-torque detection during constant speed
operation, stop operation after detection
3: Over-torque detection during operation, continue to
operate after detection
4: Over-torque detection during operation, stop
operation after detection
0
06-07 Over-torque Detection Level
(OT1)
10~250% (100%: drive’s rated current)
120
06-08 Over-torque Detection Time
(OT1)
0.0~60.0 sec.
0.1
06-09 Over-torque Detection Selection
(OT2)
0: No function
1: Over-torque detection during constant speed
operation, continue to operate after detection
2: Over-torque detection during constant speed
operation, stop operation after detection
3: Over-torque detection during operation, continue to
operation after detection
4: Over-torque detection during operation, stop
operation after detection
0
06-10 Over-torque Detection Level
(OT2)
10~250% (100%: drive’s rated current)
120
06-11 Over-torque Detection Time
(OT2)
0.0~60.0 sec.
0.1
06-12 Current
Limit
0~250% (100%: drive’s rated current
)
150
06-13 Electronic Thermal Relay
Selection (Motor 1)
0: Inverter motor
(fan doesn’t run with the axel synchronously )
1: Standard motor
(fan runs with the axel synchronously)
2: Electronic thermal relay disabled
2
06-14 Electronic Thermal Characteristic
for Motor 1
30.0~600.0 sec.
60.0
06-15 Heat Sink Over-heat (OH)
Warning
0.0~110.0
℃
85.0
06-16 Stall Prevention Limit Level
0~100% (Pr.06-03, Pr.06-04)
50
06-17 Present Fault Record
0: No fault record
0
Summary of Contents for CT2000 Series
Page 5: ...Chapter 1 Introduction CT2000 Series 1 2 Model Name VFD 750 CT 43 F 00 A6 Serial Number...
Page 22: ...Chapter 1 Introduction CT2000 Series 1 19 Digital Keypad KPC CC01 KPC CE01 Unit mm inch...
Page 23: ...Chapter 1 Introduction CT2000 Series 1 20 This page intentionally left blank...
Page 41: ...Chapter 4 Wiring CT2000 Series 4 6 This page intentionally left blank...
Page 71: ...Chapter 7 Optional Accessories CT2000 Series 7 18 Wall Mounting Embedded Mounting...
Page 87: ...Chapter 8 Optional Cards CT2000 Series 8 8 PG Card intallation...
Page 88: ...Chapter 8 Optional Cards CT2000 Series 8 9 Disconneting the extension card...
Page 92: ...Chapter 8 Optional Cards CT2000 Series 8 13 PG2 Wiring Diagram...
Page 95: ...Chapter 8 Optional Cards CT2000 Series 8 16 PG2 Wiring Diagram...
Page 117: ...Chapter 8 Optional Cards CT2000 Series 8 38 This page intentionally left blank...
Page 259: ...Chapter 12 Description of Parameter Settings CT2000 Series 12 1 03 11...
Page 260: ...Chapter 12 Description of Parameter Settings CT2000 Series 12 1 03 12...
Page 263: ...Chapter 12 Description of Parameter Settings CT2000 Series 12 1 03 15...
Page 266: ...Chapter 12 Description of Parameter Settings CT2000 Series 12 1 03 18...
Page 397: ...Chapter 13 Warning Codes CT2000 Series 13 8 This page intentionally left blank...
Page 407: ...Chapter 14 Fault Codes and Descriptions CT2000 Series 14 10 This page intentionally left blank...
Page 489: ...Chapter 16 PLC Function CT2000 Series 16 48 LD X1 Load Contact a of X1 OUT Y1 Drive Y1 coil...
Page 592: ...Chapter 16 PLC Function CT2000 Series 16 151...
Page 594: ...Chapter 16 PLC Function CT2000 Series 16 153...
Page 597: ...Chapter 16 PLC Function CT2000 Series 16 156 This page intentionally left blank...