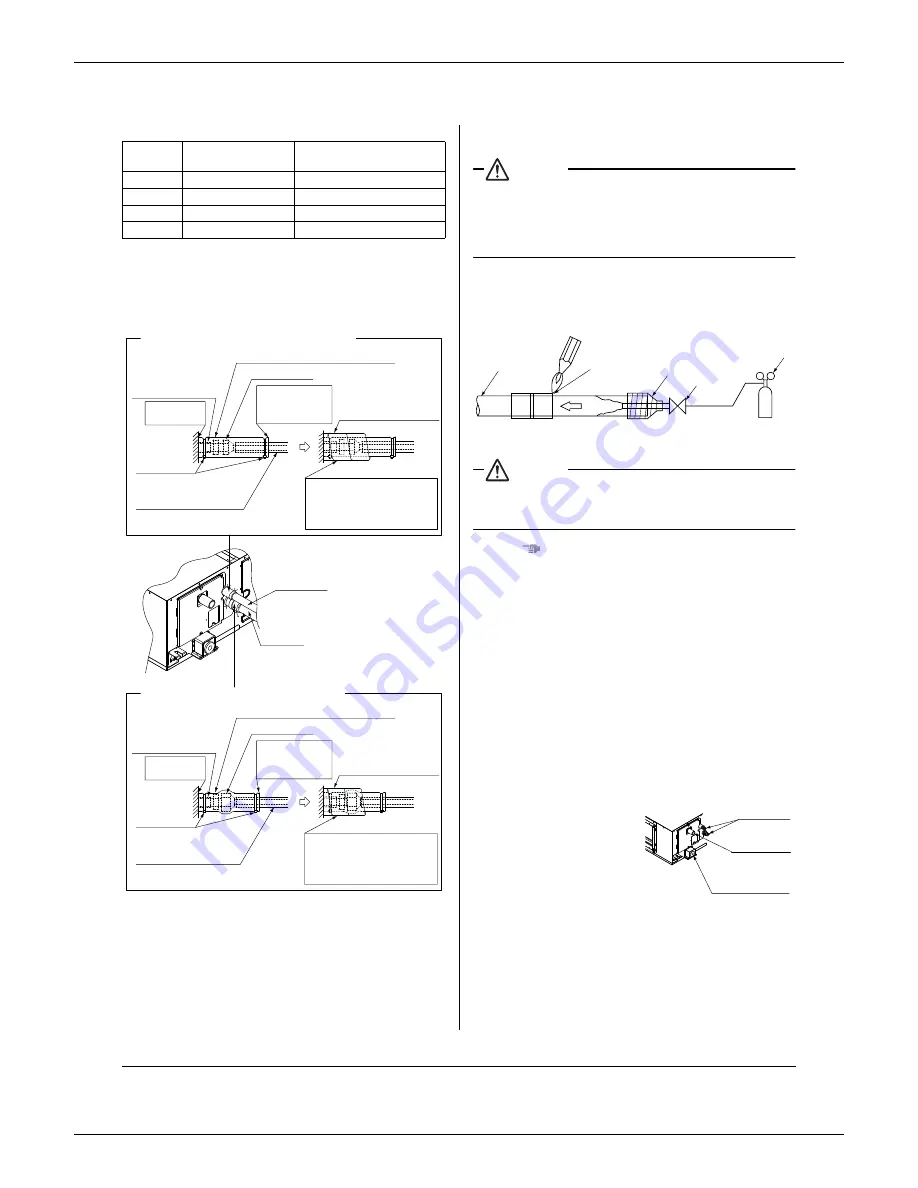
Installation of indoor unit
EDUS281120_a
194
RZR-P, RZQ-P(9)
3PN14093-12A
8
English
Table 2
(2) On completion of installation work,
check that there is no
gas leakage
.
(3) Refer to the following illustration and be sure to perform
heat insulation work on the piping joints after gas leakage
checks.
(Refer to Fig. 6)
• Use the insulation for fitting (4) and (5) provided to the
liquid piping and gas piping, respectively, and conduct
heat insulation work.
(Tighten both edges of the insulation for fitting (4) and (5)
for each joint with the clamp (8).)
• Make sure that the joint of the insulation for fitting (4) and
(5) for the joint on the liquid piping and gas piping side
faces upward.
• Wrap the middle sealing material (7) around the insula-
tion for fitting (4) and (5) for the joint (flare nut part).
CAUTION
• Be sure to perform the heat insulation of the local piping
up to the piping joint.
If the piping is exposed, dew condensation may result. Fur-
thermore, a burn may be caused if a human body comes in
contact with the piping.
• Perform nitrogen substituent or apply nitrogen into the
refrigerant piping (see NOTE 1) in the case of refrigerant
piping blazing (see NOTE 2). Then perform the flare con-
nection of the indoor unit.
(Refer to Fig. 7)
CAUTION
• Do not use any antioxidant at the time of piping blazing.
The piping may be clogged with a residual antioxidant and
parts may malfunction.
NOTE
1. At the time of blazing, set the pressure of nitrogen to
approximately 2.9 PSI (close to the pressure of a breeze
coming in contact with the cheek) with a pressure-reduc-
ing valve.
2. Do not use flux at the time of blazing and connecting the
refrigerant piping. Use a copper phosphorus brazing alloy
(BCuP-2/BCu 93P-710/795), which does not require flux,
for blazing.
(Flux has a bad influence on the refrigerant piping. Chlo-
rine-based flux will cause piping corrosion. Furthermore, if
it contains fluorine, the flux will deteriorate refrigerant oil.)
• As for the branching of the refrigerant piping or refrigerant,
refer to the installation manual provided with the outdoor unit.
7.
DRAIN PIPING WORK
(1) Conduct drain piping work.
Check that the piping
ensures proper draining.
• Make sure that the diam-
eter of the piping exclud-
ing the rising part is the
same as or larger than
the diameter of the con-
necting pipe (vinyl chloride pipe with an outer diameter
of 1-1/4 in. and a nominal inner diameter of 31/32 in.).
• Make sure that the piping is short enough
with a down-
ward slope of at least 1/100
and that there is no air
bank formed. No drain trap is required.
Pipe size
Further tightening angle
Recommended arm length of
tool
φ
1/4
60 to 90 degrees
Approx. 5-7/8 in.
φ
3/8
60 to 90 degrees
Approx. 7-7/8 in.
φ
1/2
30 to 60 degrees
Approx. 9-13/16 in.
φ
5/8
30 to 60 degrees
Approx. 11-13/16 in.
Heat
i
n
su
lat
i
on pro
c
ed
u
re for ga
s
p
i
p
i
ng
I
ns
ul
a
t
i
o
n
ma
t
eria
l
fo
r
p
i
p
ing
(o
n
u
ni
t
side
)
I
ns
ul
a
t
i
o
n
ma
t
eria
l
fo
r
p
i
p
ing
(f
ie
l
d
s
upply)
Ma
k
e
s
u
re
th
a
t
th
e
seam
f
a
c
es
up
ward.
Cl
am
p (8)
(
a
cc
ess
o
r
y)
G
as
p
i
p
e
L
i
qu
id
p
i
p
e
Fl
are
n
ut
j
o
in
t
A
tt
a
ch
ed
to
th
e
s
u
r
f
a
c
e.
I
ns
ul
a
t
i
o
n
fo
r
f
i
tt
ing
(5) (
a
cc
ess
o
r
y)
Midd
l
e
sea
l
ing
p
ad
(7)
(
a
cc
ess
o
r
y)
Wra
p th
e
ins
ul
a
t
i
o
n
ma
t
eria
l
ar
ou
nd
th
e
po
r
t
i
o
n
f
r
o
m
th
e
s
u
r
f
a
c
e
of th
e
main
u
ni
t to th
e
upp
er
p
ar
t of th
e
fl
are
n
ut
j
o
in
t
.
I
ns
ul
a
t
i
o
n
ma
t
eria
l
fo
r
p
i
p
ing
(f
ie
l
d
s
upply)
Wra
p th
e
ins
ul
a
t
i
o
n
ma
t
eria
l
ar
ou
nd
th
e
po
r
t
i
o
n
f
r
o
m
th
e
s
u
r
f
a
c
e
of th
e
main
u
ni
t to th
e
upp
er
p
ar
t of th
e
fl
are
n
ut
j
o
in
t
.
F
i
g
.
6
Heat
i
n
su
lat
i
on pro
c
ed
u
re for l
i
q
ui
d p
i
p
i
ng
I
ns
ul
a
t
i
o
n
ma
t
eria
l
fo
r
p
i
p
ing
(o
n
u
ni
t
side
)
Ma
k
e
s
u
re
th
a
t
th
e
seam
f
a
c
es
up
ward.
Cl
am
p (8)
(
a
cc
ess
o
r
y)
Main
u
ni
t
Fl
are
n
ut
j
o
in
t
A
tt
a
ch
ed
to
th
e
s
u
r
f
a
c
e.
I
ns
ul
a
t
i
o
n
fo
r
f
i
tt
ing
(4) (
a
cc
ess
o
r
y)
Midd
l
e
sea
l
ing
p
ad
(7)
(
a
cc
ess
o
r
y)
Ni
t
r
o
gen
Re
f
rigeran
t
p
i
p
ing
P
ar
t to
be
bra
z
ed
T
a
p
ing
P
ress
u
re
-
red
uc
ing
v
a
lv
e
h
ands
v
a
lv
e
Ni
t
r
o
gen
F
i
g
.
7
Re
f
rigeran
t
p
i
p
ing
D
rain
s
ock
e
t
S
ock
e
t fo
r
main
t
enan
c
e
(
wi
th
r
u
bber
c
a
p)
Summary of Contents for SkyAir RZQ-P Series
Page 1: ...Cooling Only 60Hz Heat Pump 60Hz RZR P RZQ P 9 series EDUS281120_a AMERICAS ...
Page 31: ...Dimensions and service space EDUS281120_a 30 RZR P RZQ P 9 BRC2A71 Unit in 3D047341 ...
Page 33: ...Dimensions and service space EDUS281120_a 32 RZR P RZQ P 9 BRC7E818 for FAQ 3D049736 Unit in ...
Page 34: ...EDUS281120_a Dimensions and service space RZR P RZQ P 9 33 BRC4C82 for FBQ 3D049611 Unit in ...
Page 38: ...EDUS281120_a Dimensions and service space RZR P RZQ P 9 37 3D064213A ...
Page 39: ...Dimensions and service space EDUS281120_a 38 RZR P RZQ P 9 3D064213A ...
Page 41: ...Dimensions and service space EDUS281120_a 40 RZR P RZQ P 9 3D047381B ...
Page 47: ...Wiring diagrams EDUS281120_a 46 RZR P RZQ P 9 FAQ18PVJU FAQ24PVJU 3D046039D ...
Page 61: ...Safety devices list EDUS281120_a 60 RZR P RZQ P 9 8 3 FAQ FAQ18PVJU FAQ24PVJU 4D047085B ...
Page 91: ...Capacity tables EDUS281120_a 90 RZR P RZQ P 9 RZR36PVJU RZR42PVJU 3D071685 ...
Page 92: ...EDUS281120_a Capacity tables RZR P RZQ P 9 91 RZQ36PVJU9 RZQ42PVJU9 C 3D047383B ...
Page 101: ...Sound Levels Reference EDUS281120_a 100 RZR P RZQ P 9 FBQ18PVJU FBQ24PVJU FBQ30PVJU FBQ36PVJU ...
Page 102: ...EDUS281120_a Sound Levels Reference RZR P RZQ P 9 101 FBQ42PVJU ...
Page 104: ...EDUS281120_a Sound Levels Reference RZR P RZQ P 9 103 RZQ42PVJU9 RZR42PVJU 4D072769 ...