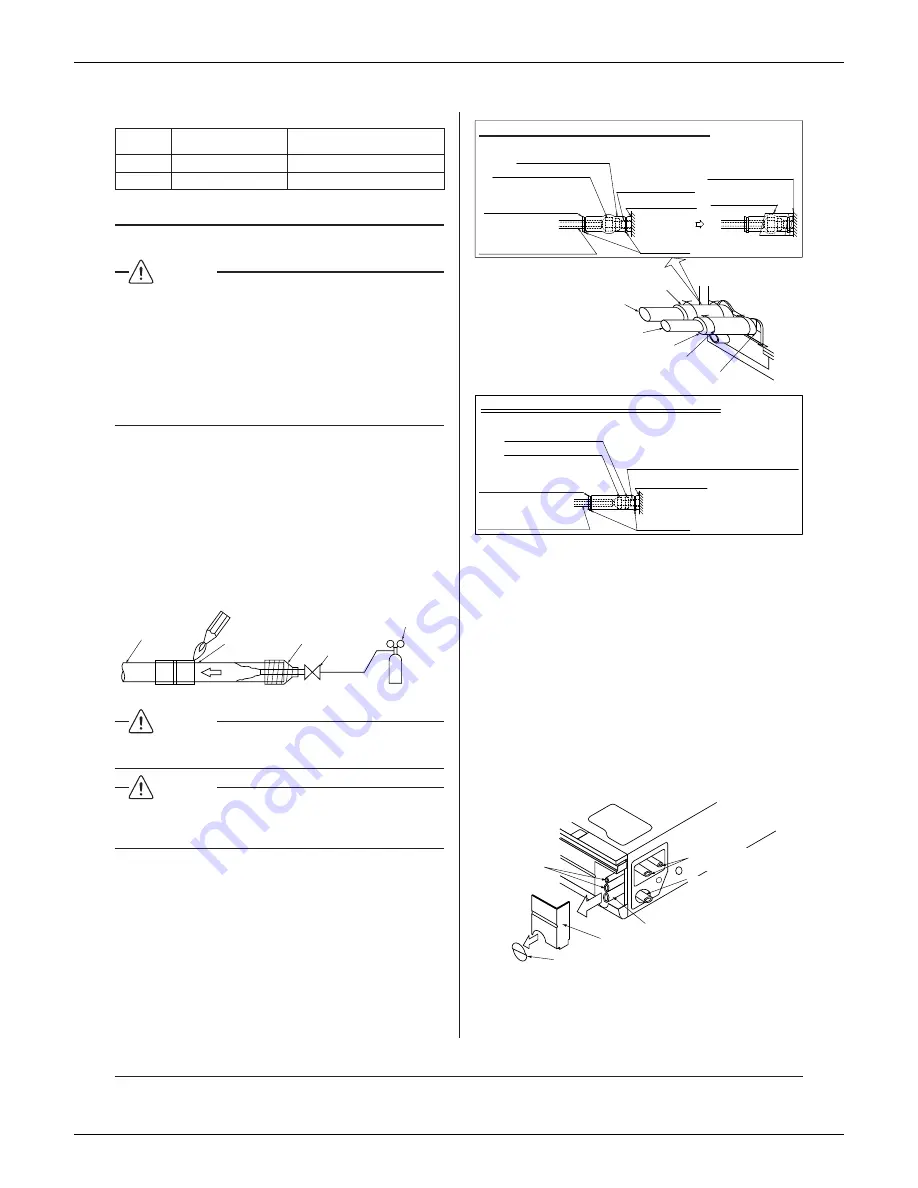
Installation of indoor unit
EDUS281120_a
144
RZR-P, RZQ-P(9)
3PN06240-12Q
8
English
Table 3
Pipe size
(in.)
Further tightening angle
Recommended arm length of tool
(in.)
φ
3/8
60 to 90 degrees
Approx. 7 7/8
φ
5/8
30 to 60 degrees
Approx. 11 13/16
After the work is fi nished, make sure to check that there
is no gas leak.
BRAZING REFRIGERANT PIPING
6-3
DANGER
CAUTION TO BE TAKEN WHEN BRAZING REFRIGERANT
PIPING
“Do not use fl ux when brazing refrigerant pipe. Therefore, use
the phosphor copper brazing fi ller metal (BCuP) which does not
require fl ux.”
(Flux has an extremely negative effect on refrigerant piping sys-
tems. For instance, if chlorine based fl ux is used, it will cause
pipe corrosion. If the fl ux contains fl uorine, it will damage the
refrigerant oil.)
Before brazing local refrigerant pipe, nitrogen gas shall be
•
blown through the pipe to expel air from the pipe.
If you brazing is done without nitrogen gas blowing, a large
amount of oxide fi lm develops inside the pipe, and could
cause system malfunction.
When brazing the refrigerant pipe, only begin brazing after
•
having carried out nitrogen substitution or while inserting
nitrogen into the refrigerant pipe. Once this is done, connect
the indoor unit with a fl ared or a fl anged connection.
Nitrogen should be set to 2.9 psi with a pressure-reducing
•
valve if brazing while inserting nitrogen into the pipe.
(Refer to Fig. 15)
Refrigerant pipe
Part to be
brazed
Taping
Pressure-reducing
valve
hands valve
Nitrogen
Nitrogen
Fig. 15
DANGER
Use of oxygen may cause an explosion resulting in serious
•
injury or death. Only use nitrogen gas.
CAUTION
Be sure to insulate any fi eld piping all the way to the piping
•
connection inside the unit. Any exposed piping may cause
condensate or a burn if touched.
PIPING INSULATION
6-4
Make absolutely sure to execute thermal insulation works on
•
the pipe-connecting section after checking gas leakage by
thoroughly studying the following fi gure and using the insula-
tion pipe cover (6) and (7). (Fasten both ends with the clamps
(4).)
(Refer to Fig. 16)
Wrap the small sealing pad (9) only around the insulation for
•
the joints on the gas piping side.
(Refer to Fig. 16)
Insulation pipe cover for gas pipe (6)
Gas pipe
Liquid pipe
Insulation pipe cover for liquid pipe (7)
Clamp (4) (× 4)
Attach to the bottom
(For both gas pipe and liquid pipe)
Procedure for thermal insulation of liquid-side pipe
Insulation pipe cover for
liquid pipe (7)
Orient so that the end of
the wrapped insulation
material is facing up
Flare nut connection
Insulation pipe cover (main unit)
Attach to base
Main unit
Main unit
Clamp (4)
Clamp (4)
Insulation pipe cover
(Locally procured)
Procedure for thermal insulation of gas-side pipe
Insulation pipe cover
for gas pipe (6)
Insulation pipe
cover (main unit)
Attach to base
Orient so that the end of
the wrapped insulation
pipe cover is facing up
Flare nut connection
Insulation pipe cover
(Locally procured)
Wind around the
pipe, beginning at
the base.
Small sealing
pad (9)
Fig. 16
For piping facing back.
(1)
Remove the rear metal plate for pipe.
(Refer to Fig. 17)
The fi gure of the direction of back shows when both the pip-
•
ing and drain pipe are set backward.
When setting the piping to face up or right, attach the rear
metal plate for refrigerant pipe and plug a hole for drain pipe.
(See “4 PREPARATIONS BEFORE INSTALLATION” (3-3) on
page 6)
For piping facing up.
(2)
When setting the piping to face up, the L-shaped branch
•
pipe kit sold separately is required.
Removing the top penetration lid and use the L-shaped branch
•
pipe kit sold separately to set the pipe.
(Refer to Fig. 18, 19)
For piping facing right.
(3)
Cut out a slit hole on the decoration panel (right) and set the
•
pipe.
(Refer to Fig. 17)
Ri
g
ht-facin
g
drain pipe
Ri
g
ht-facin
g
refri
g
erant
pipin
g
Decoration panel (ri
g
ht) removable part
If only settin
g
the drain pipe to
face ri
g
ht, cut this section only.
Fig. 17
Rear-facin
g
refri
g
erant pipe
Rear ri
g
ht-facin
g
drain pipe
Summary of Contents for SkyAir RZQ-P Series
Page 1: ...Cooling Only 60Hz Heat Pump 60Hz RZR P RZQ P 9 series EDUS281120_a AMERICAS ...
Page 31: ...Dimensions and service space EDUS281120_a 30 RZR P RZQ P 9 BRC2A71 Unit in 3D047341 ...
Page 33: ...Dimensions and service space EDUS281120_a 32 RZR P RZQ P 9 BRC7E818 for FAQ 3D049736 Unit in ...
Page 34: ...EDUS281120_a Dimensions and service space RZR P RZQ P 9 33 BRC4C82 for FBQ 3D049611 Unit in ...
Page 38: ...EDUS281120_a Dimensions and service space RZR P RZQ P 9 37 3D064213A ...
Page 39: ...Dimensions and service space EDUS281120_a 38 RZR P RZQ P 9 3D064213A ...
Page 41: ...Dimensions and service space EDUS281120_a 40 RZR P RZQ P 9 3D047381B ...
Page 47: ...Wiring diagrams EDUS281120_a 46 RZR P RZQ P 9 FAQ18PVJU FAQ24PVJU 3D046039D ...
Page 61: ...Safety devices list EDUS281120_a 60 RZR P RZQ P 9 8 3 FAQ FAQ18PVJU FAQ24PVJU 4D047085B ...
Page 91: ...Capacity tables EDUS281120_a 90 RZR P RZQ P 9 RZR36PVJU RZR42PVJU 3D071685 ...
Page 92: ...EDUS281120_a Capacity tables RZR P RZQ P 9 91 RZQ36PVJU9 RZQ42PVJU9 C 3D047383B ...
Page 101: ...Sound Levels Reference EDUS281120_a 100 RZR P RZQ P 9 FBQ18PVJU FBQ24PVJU FBQ30PVJU FBQ36PVJU ...
Page 102: ...EDUS281120_a Sound Levels Reference RZR P RZQ P 9 101 FBQ42PVJU ...
Page 104: ...EDUS281120_a Sound Levels Reference RZR P RZQ P 9 103 RZQ42PVJU9 RZR42PVJU 4D072769 ...