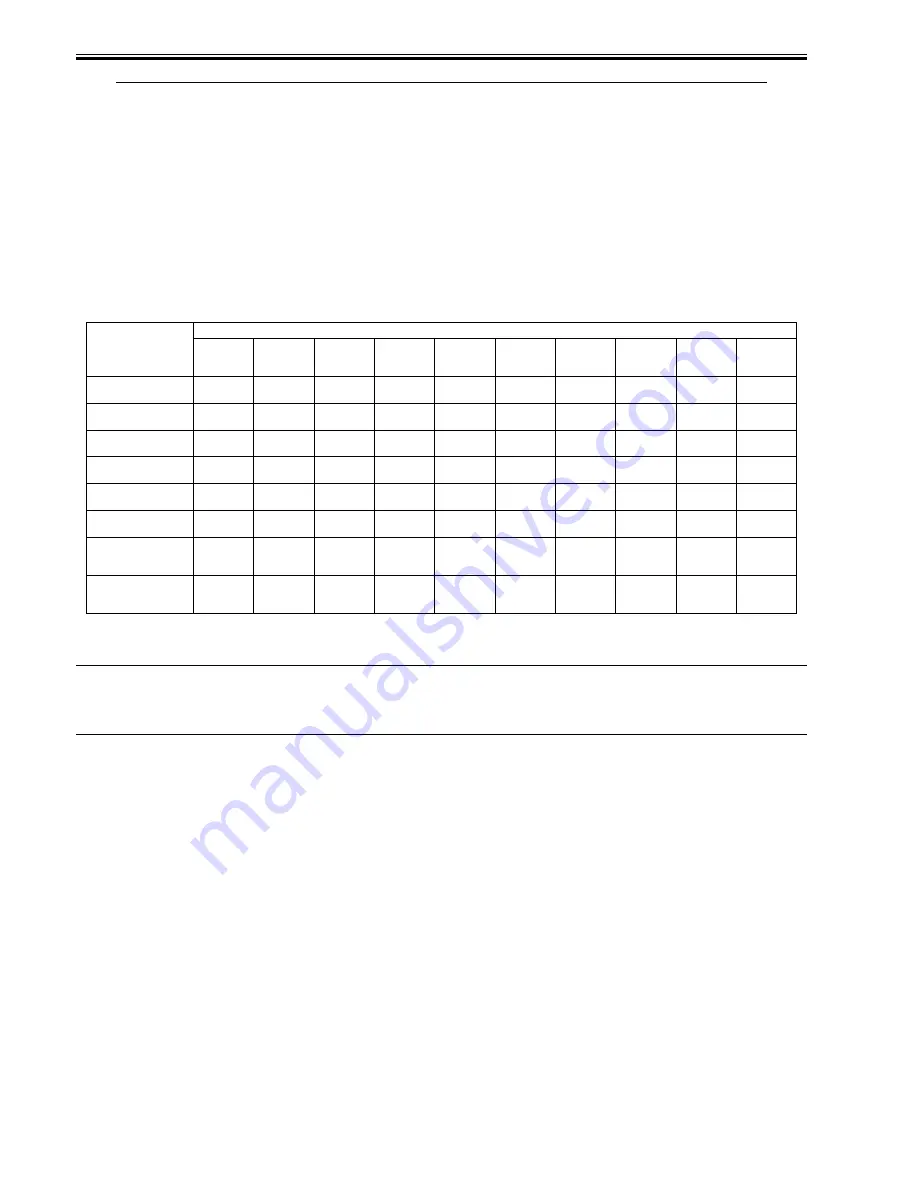
Chapter 7
7-12
UN16: color displacement sensor A (also serves as patch image sensor)
UN15: color displacement sensor B
7.3.2 Timing of Image Stabilization Control
0013-8483
/ / / / iR C3380i / iR C3380 / iR C2880i / iR C2880
The items that are executed as part of image stabilization control differ depending on the condition of the machine (environment or deterioration of parts associated
with the image formation system). The following table shows the items:
T-7-11
*1: The down-time interval includes the time during which the drum unit rotates idly (10 sec).
*2: This item is executed when the ongoing sleep state lasts more than 8 hr (otherwise, nothing will take place).
*3: At times, ATR control and color displacement may be executed by interrupting the ongoing print job.
MEMO:
- When the user mode "auto gradation adjustment $ full adjustment" is selected, PASCAL control, D-half control and ARCDAT control are implemented in this
order to adjust the image gradation density (full adjustment).
- When the user mode "auto gradation adjustment $ quick adjustment" is selected, D-half control and ARCDAT control are implemented in this order to adjust
image gradation density (quick adjustment).
7.3.3 Drum Film Thickness Detection
0013-8484
/ / / / iR C3380i / iR C3380 / iR C2880i / iR C2880
To form an optimum image against the possible wear on the photosensitive drum, the machine checks the thickness of the drum film. The check is made for every
drum (color), and the result is recorded in EEPROM of the DC controller.
The DC controller is referred when this data detects the primary charging AC bias, the primary transfer bias, and the ATR control target value.
1. Start-Up Timing
at power-on, when closing/opening the front cover, at time of printing
2. Particulars of Control
The DC controller goes through the following to detect the thickness of the drum film:
1) computes the drum count based on "length of time during which the photosensitive drum has rotated" and "length of time during which the primary charging AC
bias is applied."
2) adds the count obtained in 1 above to the count stored in EEPROM.
3) identifies the count as indicating any of the following 3 in terms of the drum film thickness detection data based on the latest count obtained in 2 above: initial
condition, normal condition, final condition.
4) in the event of there being a difference as the result of comparison of the latest drum film thickness data against the stored drum film thickness data, the new data
is written over the existing data; in the absence of a difference, on the other hand, no write operation will take place and the new data will be discarded.
[3]Color Dmax control
determines the best level of laser power
[4]Black Dmax control
determines the best level of developing bias
[5]PASCAL control
determines the best gradation table
[6]Dhalf control
determines the best gradation table
[7]Abridged Dhalf control
determines the best gradation table (abridged)
[8]Color displacement correction control
determines the correction value of color displacement
[9]ATVC control
determines the best level of transfer bias
Condition
Items
Down-time
(Max)
Drum film
thickness
detection
ATR control Color D-max
control
Black D-max
control
PASCAL
control
D-half
control
Abridged D-
half control
Color
displacemen
t control
ATVC
control
Power-on
22 sec
(approx.)
Yes
Yes
Yes
Yes
Drum unit replacement
(w/ new)
215 sec
(approx.) *1
Yes
Yes
Yes
Yes
Yes
Yes
Yes
Return from sleep state
*2
22 sec
(approx.)
Yes
Yes
Yes
Yes
Initial rotation
10 sec
(approx.)
Yes
Yes
Yes
Printing *3
15 sec
(approx.)
Yes
Yes
Yes
Post-rotation
55 sec
(approx.)
Yes
Yes
Yes
Yes
Yes
Yes
When user-specific
calibration is performed
(full correction)
100 sec
(approx.)
Yes
Yes
Yes
Yes
Yes
When user-specific
calibration is performed
(quick correction)
55 sec
(approx.)
Yes
Yes
Yes
Yes
Item
Description
Summary of Contents for iR C3380 series
Page 1: ...Aug 29 2006 Service Manual iR C3380 2880 Series...
Page 2: ......
Page 6: ......
Page 23: ...Chapter 1 Introduction...
Page 24: ......
Page 26: ......
Page 52: ......
Page 53: ...Chapter 2 Installation...
Page 54: ......
Page 127: ...Chapter 3 Basic Operation...
Page 128: ......
Page 130: ......
Page 136: ......
Page 137: ...Chapter 4 Main Controller...
Page 138: ......
Page 160: ......
Page 161: ...Chapter 5 Original Exposure System...
Page 162: ......
Page 188: ...Chapter 5 5 24 F 5 68 4 Remove the original sensor 2 hook 1 F 5 69...
Page 189: ...Chapter 6 Laser Exposure...
Page 190: ......
Page 192: ......
Page 206: ......
Page 207: ...Chapter 7 Image Formation...
Page 208: ......
Page 256: ......
Page 257: ...Chapter 8 Pickup Feeding System...
Page 258: ......
Page 262: ......
Page 303: ...Chapter 9 Fixing System...
Page 304: ......
Page 306: ......
Page 321: ...Chapter 10 Externals and Controls...
Page 322: ......
Page 326: ......
Page 336: ...Chapter 10 10 10 F 10 10 2 Remove the check mark from SNMP Status Enabled...
Page 337: ...Chapter 10 10 11 F 10 11...
Page 359: ...Chapter 11 MEAP...
Page 360: ......
Page 362: ......
Page 401: ...Chapter 12 RDS...
Page 402: ......
Page 404: ......
Page 411: ...Chapter 13 Maintenance and Inspection...
Page 412: ......
Page 414: ......
Page 416: ...Chapter 13 13 2 F 13 1 8 9 1 2 3 3 5 6 7 10 11 12 13 14 4...
Page 421: ...Chapter 14 Standards and Adjustments...
Page 422: ......
Page 424: ......
Page 431: ...Chapter 15 Correcting Faulty Images...
Page 432: ......
Page 434: ......
Page 459: ...Chapter 16 Self Diagnosis...
Page 460: ......
Page 462: ......
Page 481: ...Chapter 17 Service Mode...
Page 482: ......
Page 484: ......
Page 571: ...Chapter 18 Upgrading...
Page 572: ......
Page 574: ......
Page 603: ...Chapter 19 Service Tools...
Page 604: ......
Page 606: ......
Page 609: ...Aug 29 2006...
Page 610: ......