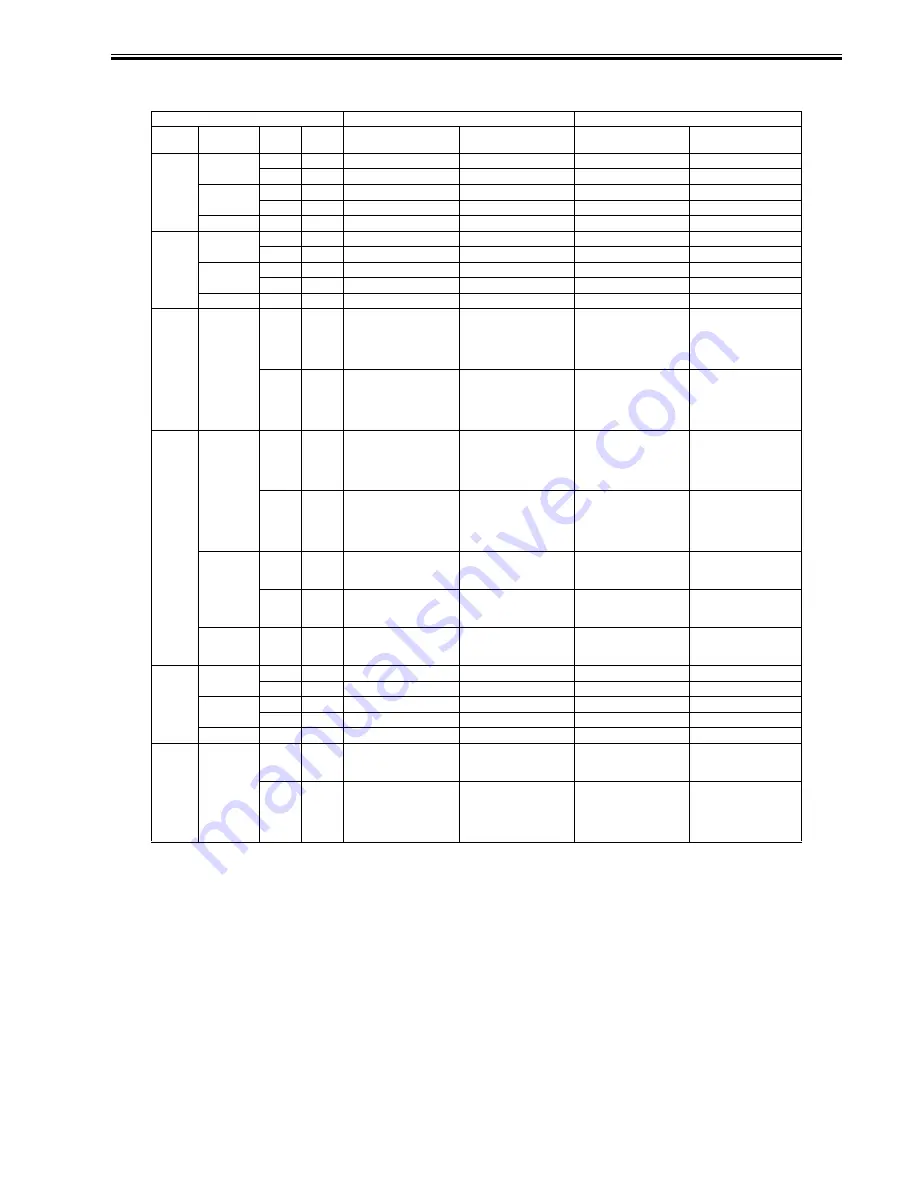
Chapter 8
8-11
* Size: S=LTR (216 mm) or shorter, L=longer than 216 mm
T-8-5
* size: S=LTR (216mm) or shorter, L=longer than 216mm
8.3.4 Reversing Accelerating Control of Large Size Paper
0014-5567
/ / / / iR C3380i / iR C3380 / iR C2880i / iR C2880
This machine executes fixing arch control (details will be explained later at fixing control). In the case of executing reversing of the large size paper, after the paper
leading edge turns on the reversing sensor [2], the paper trailing edge is pulled by fixing, resulting in failure to correctly measure time until the paper stops at the
reversing point.
So, the following controls are performed for reversing the large size paper.
When the paper leading edge turns on the reversing sensor [2], and if the trailing edge point, which is calculated from the paper size, does not pass over the secondary
transfer roller [5] [6] (in the case of executing arch control of fixing), drop the speed of the delivery-2/-3 motors to 135mm/s. Because 135mm/s is the lower speed
for fixing arch control, the paper will not be pulled from the point of the fixing to the reversing. When the trailing edge passes over the secondary transfer roller [5]
[6], the fixing arch control is completed. And then, the fixing speed is returned to 143mm/s, so as the speed of the delivery-2/-3 motors.
Afterwards, the paper feeding speed accelerates to 460mm/s when the trailing edge is at the point of +10mm from the fixing rear roller [4], and starts to decelerate
at the point of 43.8mm from the reversing roller [1] (30mm from the reversing roller = reversing point [3], the distance from when the delivery-3 motor starts at
460mm/s until it completely stops = 13.8mm) to let it stop at the reversing point.
The followings show the timing for reversing accelerating control according to the paper size (after turning on the reversing sensor until the delivery-3 motor is
stopped).
Delivery-3 motor
Buffer motor
Outlet
Paper type
Size*
Speed
(mm/s)
Acceleration point
Deceleration point
Acceleration point
Deceleration point
Primary
delivery
Plain paper
S
337
-
-
-
-
L
337
-
-
-
-
Heavy paper
S
71.5
-
-
-
-
L
71.5
-
-
-
-
Transparency S
71.5
-
-
-
-
Secondary
delivery
Plain paper
S
460
-
-
-
-
L
460
-
-
-
-
Heavy paper
S
71.5
-
-
-
-
L
71.5
-
-
-
-
Transparency S
71.5
-
-
-
-
Tertiary
delivery
Plain paper
S
460
Detect the paper leading
edge with the reversing
sensor
Detect the paper trailing
edge at 17.5mm
upperstream of delivery-3
roller (detected by the
delivery 3 sensor)
-
-
L
460
Detect the paper trailing
edge at 10mm downstream
of inside delivery roller
(detected with inside
delivery sensor)
Detect the paper trailing
edge at 17.5mm
upperstream of delivery-3
roller (detected by the
delivery 3 sensor)
-
-
Finisher
Y1/Saddle
finisher
Y2
Plain paper
S
337
-
-
Detect the paper trailing
edge at 10mm downstream
of fixing rear roller
(detected with the inside
delivery sensor)
N/A
L
337
-
-
Detect the paper trailing
edge at 10mm downstream
of fixing rear roller
(detected with the inside
delivery sensor)
N/A
Heavy paper
S
143
-
-
Detect the paper leading
edge with the buffer inlet
sensor
N/A
L
143
-
-
Detect the paper leading
edge with the buffer inlet
sensor
N/A
Transparency
S
143
-
-
Detect the paper leading
edge with the buffer inlet
sensor
N/A
Finisher
Z1
Plain paper
S
143
-
-
-
-
L
143
-
-
-
-
Heavy paper
S
71.5
-
-
-
-
L
71.5
-
-
-
-
Transparency
S
71.5
-
-
-
-
Duplexing Plain
paper
S
460
Detect the paper leading
edge with the reversing
sensor
N/A
-
-
L
460
Detect the paper trailing
edge at 10mm downstream
of inside delivery roller
(detected with inside
delivery sensor)
N/A
-
-
Summary of Contents for iR C3380 series
Page 1: ...Aug 29 2006 Service Manual iR C3380 2880 Series...
Page 2: ......
Page 6: ......
Page 23: ...Chapter 1 Introduction...
Page 24: ......
Page 26: ......
Page 52: ......
Page 53: ...Chapter 2 Installation...
Page 54: ......
Page 127: ...Chapter 3 Basic Operation...
Page 128: ......
Page 130: ......
Page 136: ......
Page 137: ...Chapter 4 Main Controller...
Page 138: ......
Page 160: ......
Page 161: ...Chapter 5 Original Exposure System...
Page 162: ......
Page 188: ...Chapter 5 5 24 F 5 68 4 Remove the original sensor 2 hook 1 F 5 69...
Page 189: ...Chapter 6 Laser Exposure...
Page 190: ......
Page 192: ......
Page 206: ......
Page 207: ...Chapter 7 Image Formation...
Page 208: ......
Page 256: ......
Page 257: ...Chapter 8 Pickup Feeding System...
Page 258: ......
Page 262: ......
Page 303: ...Chapter 9 Fixing System...
Page 304: ......
Page 306: ......
Page 321: ...Chapter 10 Externals and Controls...
Page 322: ......
Page 326: ......
Page 336: ...Chapter 10 10 10 F 10 10 2 Remove the check mark from SNMP Status Enabled...
Page 337: ...Chapter 10 10 11 F 10 11...
Page 359: ...Chapter 11 MEAP...
Page 360: ......
Page 362: ......
Page 401: ...Chapter 12 RDS...
Page 402: ......
Page 404: ......
Page 411: ...Chapter 13 Maintenance and Inspection...
Page 412: ......
Page 414: ......
Page 416: ...Chapter 13 13 2 F 13 1 8 9 1 2 3 3 5 6 7 10 11 12 13 14 4...
Page 421: ...Chapter 14 Standards and Adjustments...
Page 422: ......
Page 424: ......
Page 431: ...Chapter 15 Correcting Faulty Images...
Page 432: ......
Page 434: ......
Page 459: ...Chapter 16 Self Diagnosis...
Page 460: ......
Page 462: ......
Page 481: ...Chapter 17 Service Mode...
Page 482: ......
Page 484: ......
Page 571: ...Chapter 18 Upgrading...
Page 572: ......
Page 574: ......
Page 603: ...Chapter 19 Service Tools...
Page 604: ......
Page 606: ......
Page 609: ...Aug 29 2006...
Page 610: ......