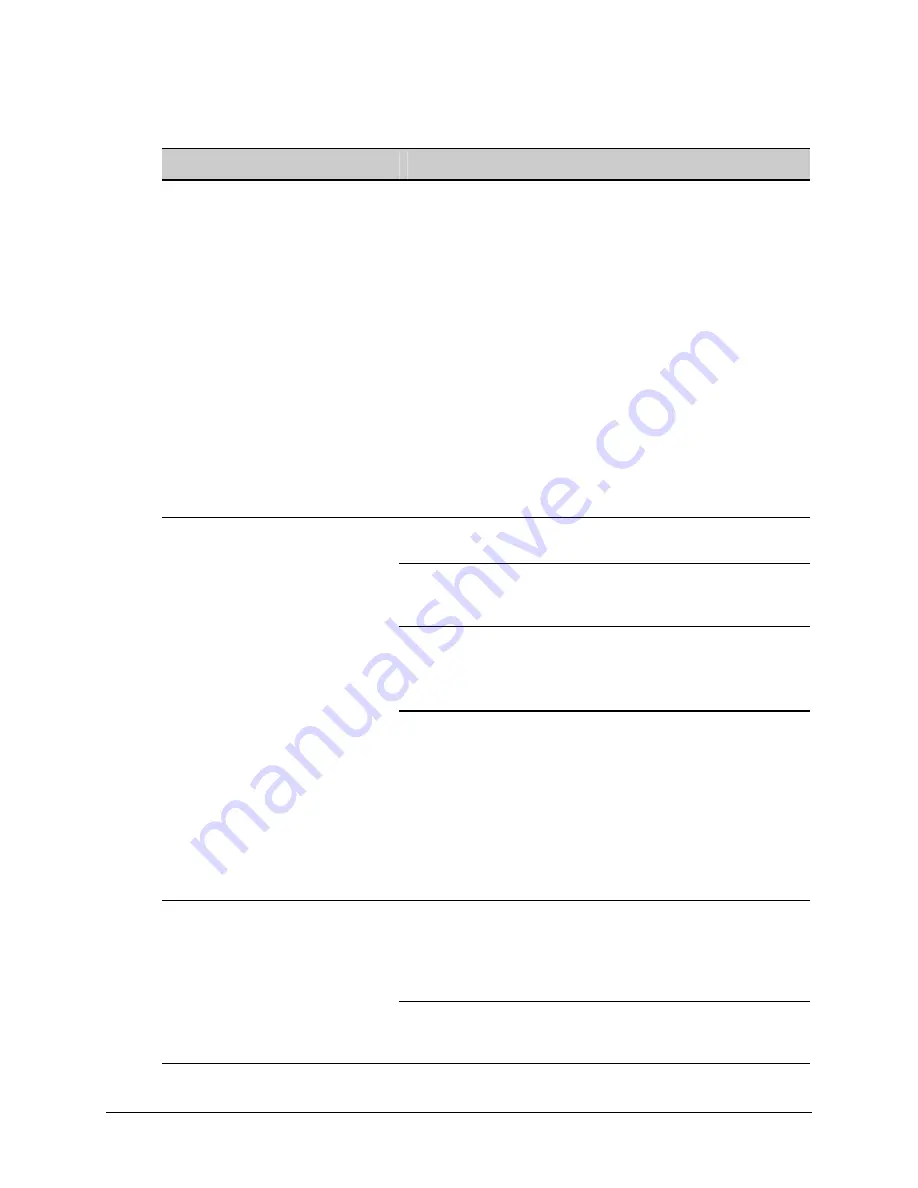
62
| Chapter 3: Operation
Define Wash ASPIRATE (ASPIR) Program Options
Option & Description
Models
Action/Comments
Aspirate Height
Represents the height
between the bottom of
the
aspirate
tubes and
the carrier surface on
which the plate rests
when
aspirating
the
microwells.
The aspirate tubes are
longer than the dispense
tubes. See
Figures 18
to
20
.
All
The Aspirate Height range is 12 to 180.
The washer display shows the
corresponding measurement in
millimeters for each option.
12 is the closest to the carrier surface;
180 is the furthest from this surface.
It is not recommended that the aspirate
tubes touch the well bottoms.
Use the
Adjust Utility
(see page 92) to
determine at what setting the aspirate
tubes hit the bottom of the well, and
choose a setting 2 to 4 steps higher in
your wash program.
Note:
Due to hardware variations, the
180 value may be out of range for some
washers; it is recommended, therefore,
that the highest value be closer to
175
.
ELx405,
Magna
The range is -30 to 30.
Select,
Select CW,
HT/96-tube
The range is -55 to 55 with 96-well
plates.
Select,
Select CW,
HT/96-tube
HT/192-tube
The range –25 to 25 with 384-well plates.
Note:
For higher throughput of the HT
with 384-well plates, use the 192-tube
manifold.
Horizontal Aspr Pos
Horizontal Aspirate
Position represents the
left and right position of
the aspirate tubes when
the carrier is beneath the
manifold.
The washer display shows the corresponding
measurement in millimeters for each option.
A
negative offset
positions the aspirate tubes toward
the left side of the well. A
positive offset
positions the
aspirate tubes toward the right side of the well. A setting
of
0
indicates no offset (0.000 mm).
It is recommended that aspirate tubes be positioned
close to the sides of a flat-bottom well, and in the center
of a round-bottom well. Use
UTIL
to experiment with
settings.
Magna
Appears only on the Magna model, if
96bead
(instead of
96
) was selected for
Plate Type
.
A range of –20 to 20 may be selected; the
default is 0.
Magnet Aspirate Height
The height of the magnet
carrier during aspiration.
Use the
Adjust Utility
(see page 92) to determine the
height of the magnet carrier in relation to the microplate
carrier.
Bio-Tek Instruments, Inc.
Summary of Contents for ELx405
Page 2: ......
Page 4: ...ii Preface Bio Tek Instruments Inc...
Page 6: ...iv Preface Bio Tek Instruments Inc...
Page 70: ...40 Chapter 2 Installation Bio Tek Instruments Inc...
Page 168: ...138 Chapter 4 Preventive Maintenance Bio Tek Instruments Inc...
Page 200: ...170 Chapter 5 Performance Verification Qualification Tests Bio Tek Instruments Inc...
Page 214: ...184 Appendix A Troubleshooting Bio Tek Instruments Inc...
Page 250: ...220 Index Bio Tek Instruments Inc...