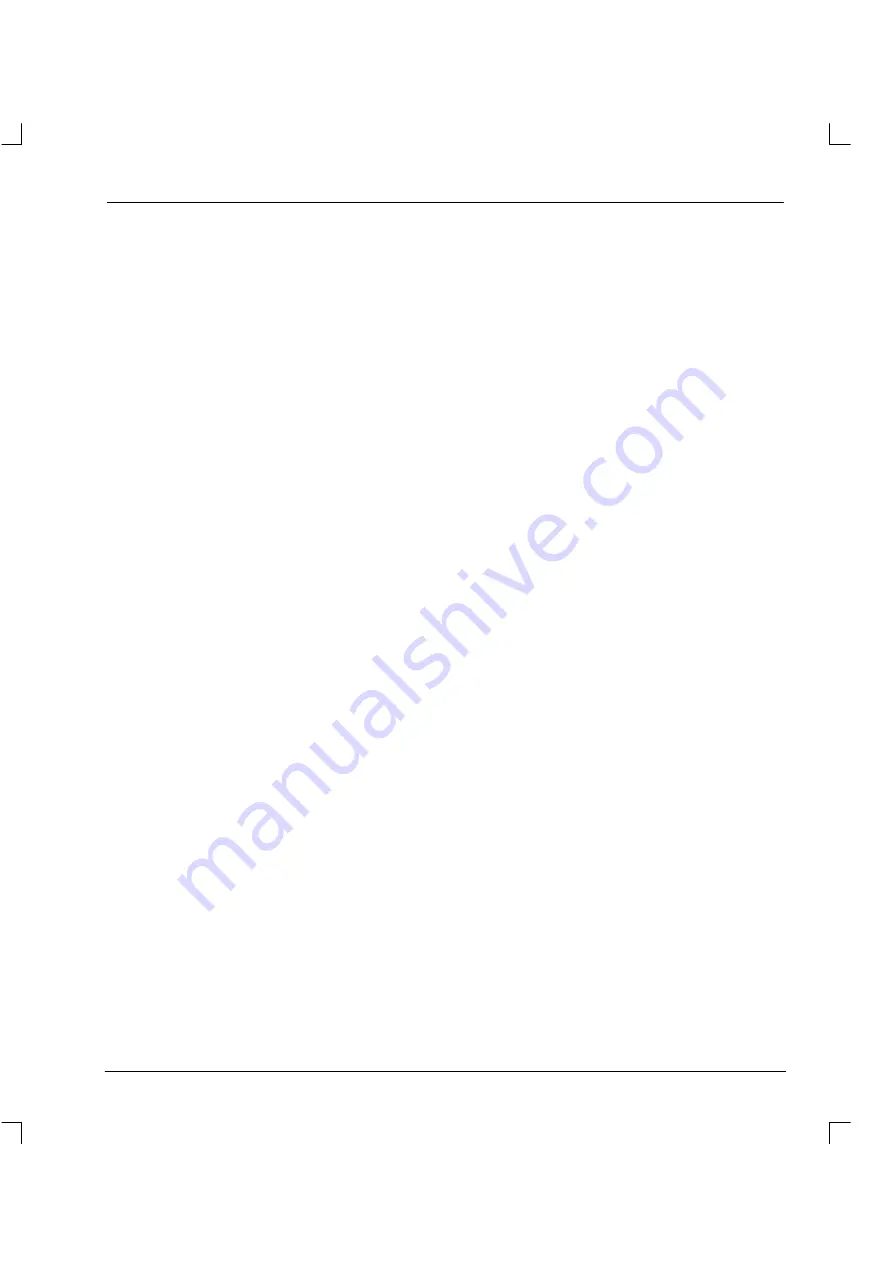
99
A.1.1
Closed loop control
It is possible that control could be achieved by applying a signal proportional to the position error alone,
but this is a rather simplistic approach. If it is imagined that there is a small error between demanded
and actual position, a proportional controller will simply multiply the error by a constant (the Proportional
gain) and apply the resultant to the motor. If the gain is too high this may cause overshoot, which will
result in the motor vibrating back and forth around the desired position. As the gain is increased, the
MintDrive will present more resistance to positional error, but oscillations will increase in magnitude until
the system becomes unstable. To reduce the onset of instability a damping term is incorporated in the
servo loop algorithm, called velocity feedback gain. Velocity feedback acts to resist rapid movement of
the motor and hence allows the Proportional gain to be set higher before vibration occurs.
Alternatively, derivative gain (the derivative of the error) can be used for damping.
With Proportional gain and velocity feedback (or derivative action) it is possible for a motor at rest at a
set point to exhibit a small positional error (called following error). The MintDrive multiplies the error by
the proportional term to produce an applied corrective torque (in current control), but for very small
errors the torque may not be large enough to overcome static friction. This error can be overcome by
incorporating an integral term in the loop calculations. Integral action involves summing the error over
time, so that motor torque is gradually increased until the positional error falls to zero. The speed at
which integral action works is controlled by the integral gain. Integral action is useful to eliminate steady
state positional errors, but will result in reduced dynamic response for the system. For this reason, a
software selectable option
KINTMODE
is provided so that the user can select that the integrator is
switched off during periods of constant velocity. With integral gain, it is possible for the output to wind up
to 100% demand. This effect can be limited using the
KINTLIMIT
keyword which limits the effect of the
integral gain at a defined percentage of the demand output.
The final term in the control loop is velocity feed forward. This is useful for increasing the response and
reducing the following error, especially with velocity controlled servos.
In summary, the following rules can be used as a guide:
H
KPROP: Increasing KPROP will speed up the response and reduce the effect of disturbances and
load variations. The side effect of increasing KPROP is that it also increases the overshoot, and if
set too high it will cause the system to become unstable. The aim is to set the Proportional gain as
high as possible without getting overshoot, instability or ’hunting’ on an encoder edge when
stationary (the motor will buzz).
H
KVEL: This gain has a damping effect, and can be increased to reduce any overshoot. If KVEL
becomes too large it will amplify any noise on the velocity measurement and introduce oscillations.
H
KINT: This gain has a de-stabilizing effect, but a small amount can be used to reduce any steady
state errors. (By default, KINTMODE is set to ignore the KINT term).
H
KINTLIMIT: The integration limit determines the maximum value of the effect of integral action.
This is specified as a percentage of the full scale demand.
H
KVELFF: This is a feed forward term and as such has a different effect on the servo system than the
previous gains. KVELFF is outside the closed loop and therefore does not have an effect on
system stability. This gain allows a faster response to demand speed changes with lower following
errors, for example you would increase KVELFF to reduce the following error during the slew
section of a trapezoidal move. The trapezoidal test move can be used to fine-tune this gain.
H
KDERIV: This gain has a damping effect. The Derivative action has the same effect as the velocity
feedback if the velocity feedback and feedforward terms are equal, but scaled by a factor of 16.
H
KACCEL: This term is designed to reduce velocity overshoots on high acceleration moves. Due to
the quantization of the positional data and the speed of the servo loop, for the acceleration feed
forward term to affect the servo loop the acceleration of the axis must exceed 1,000,000 encoder
counts per second.
Summary of Contents for MintDrive
Page 2: ...MN1274 06 2001 Installation Manual Installation Manual...
Page 3: ......
Page 13: ...xii...
Page 56: ...43 Figure 22 Auxiliary encoder circuit...
Page 91: ...78...
Page 97: ...84...
Page 109: ...96...
Page 111: ...98 Figure A 1 MintDrive Closed Loop System Motor Speed Filter 16 Sample Filter...
Page 119: ...106...
Page 141: ...128...
Page 147: ...134...
Page 154: ......