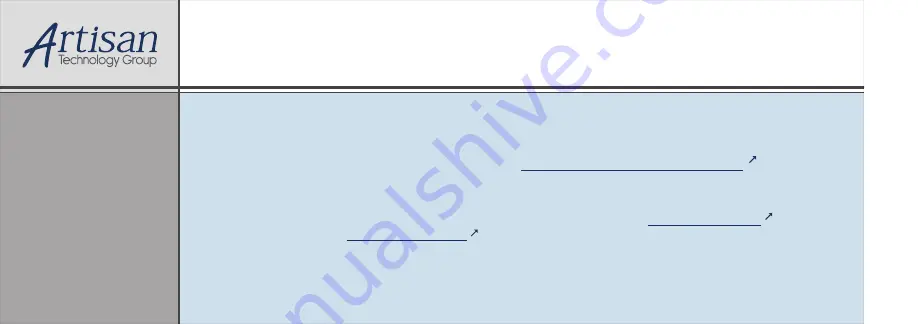
Artisan Technology Group
is your source for quality
new and certified-used/pre-owned equipment
•
FAST SHIPPING AND
DELIVERY
•
TENS OF THOUSANDS OF
IN-STOCK ITEMS
• EQUIPMENT DEMOS
•
HUNDREDS OF
MANUFACTURERS
SUPPORTED
• LEASING/MONTHLY
RENTALS
• ITAR CERTIFIED
SECURE ASSET
SOLUTIONS
SERVICE CENTER REPAIRS
Experienced engineers and technicians on staff
at our full-service, in-house repair center
WE BUY USED EQUIPMENT
Sell your excess, underutilized, and idle used equipment
We also offer credit for buy-backs and trade-ins
www.artisantg.com/WeBuyEquipment
REMOTE INSPECTION
Remotely inspect equipment before purchasing with
our interactive website at
www.instraview.com
LOOKING FOR MORE INFORMATION?
Visit us on the web at
www.artisantg.com
for more
information on price quotations, drivers, technical
specifications, manuals, and documentation
Contact us:
(888) 88-SOURCE | [email protected] | www.artisantg.com
SM
View
Instra
Summary of Contents for UNIDEX 600 Series
Page 19: ...Table of Contents U600 User s Guide xviii Aerotech Inc Version 1 4...
Page 27: ...Preface U600 User s Guide xxvi Aerotech Inc Version 1 4...
Page 163: ...AerPlot U600 User s Guide 6 6 Aerotech Inc Version 1 4...
Page 169: ...AerReg U600 User s Guide 8 4 Aerotech Inc Version 1 4...
Page 177: ...AerPlotIO U600 User s Guide 10 4 Aerotech Inc Version 1 4...
Page 179: ...Filter U600 User s Guide 11 2 Aerotech Inc Version 1 4...
Page 219: ...PrmSetup U600 User s Guide 13 2 Aerotech Inc Version 1 4...
Page 223: ...Glossary of Terms U600 User s Guide A 4 Aerotech Inc Version 1 4...
Page 353: ......